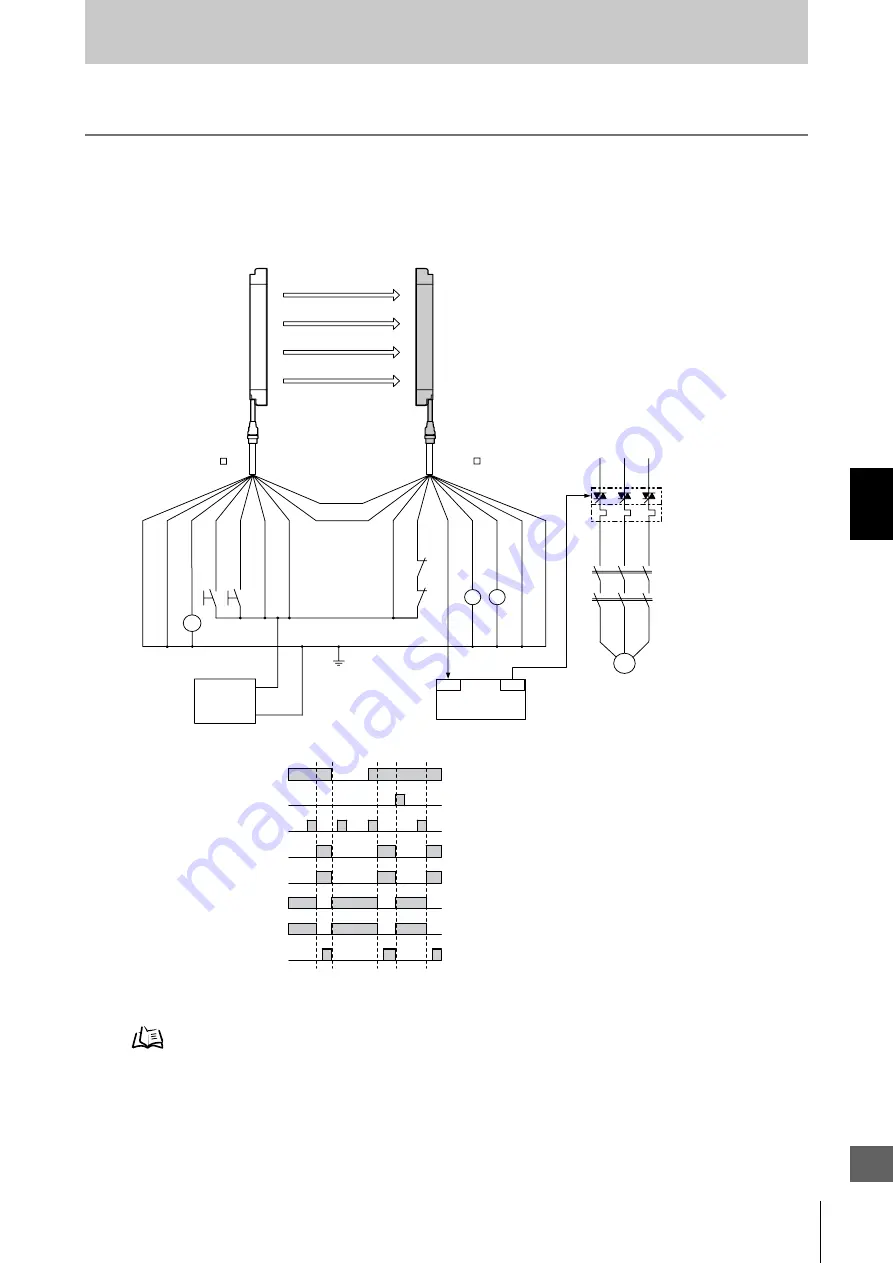
169
F3SJ-A
User’s Manual
Ch
apt
e
r
5
Wir
ing
Ex
amples
Input/Output Circuit and Applications
E
Wiring Examples
Some examples of a motor control system using F3SJ are shown. The category of these systems defined by
EN954-1 is 4.
Using only F3SJ
•Use of relay contact welding detection and interlock is possible without a controller or relay unit
- Wiring for Auto Reset Mode p.28
- Wiring When External Device Monitoring Function Is Not Used p.28
PLC input *
OUT
PLC
IN
S1
S2
KM1
KM2
KM1
KM2
E1
+DC24V
0V
M
KM2
KM1
KM4
F39-JC A-L
F39-JC A-D
Emitter
Receiver
Communication
line (+) (Grey)
Communication
line (-) (Pink)
Shield
0V (Blue)
Test input (Green)
Reset input (Yellow)
Interlock selection input (White)
+24V (Brown)
+24V (Brown)
External device monitoring input (Red)
Auxiliary output 1 (Yelllow)
Safety
output 1 (Green)
Safety
output 2 (White)
0V (Blue)
Shield
- Manual reset mode
S1
:External test switch (connect to 0V if a switch is not required)
S2
:Interlock/lockout reset switch
KM1, KM2 :Safety relay with forcibly-guided contact (G7SA) or
magnetic contactor
KM3
: Load or PLC (for monitoring)
KM4
:Solid state contactor (G3J)
M :3-phase
motor
E1
:24VDC power supply (S82K)
PLC :Programmable
controller
(Used for monitoring -- not related to safety system)
- Using external device monitoring function
Unblocked
Blocked
External test switch (S1)
Reset switch (S2)
Safety output
KM1,KM2 N.O. contact
KM1,KM2 N.C. contact
PLC output
KM3
Auxiliary output 2 (Red)
* Output operation mode of auxiliary output 1 is "safety output information/reverse enabled" (initial setting)
Courtesy
of
CMA/Flodyne/Hydradyne
▪
Motion
Control
▪
Hydraulic
▪
Pneumatic
▪
Electrical
▪
Mechanical
▪
(800)
426-5480
▪
www.cmafh.com