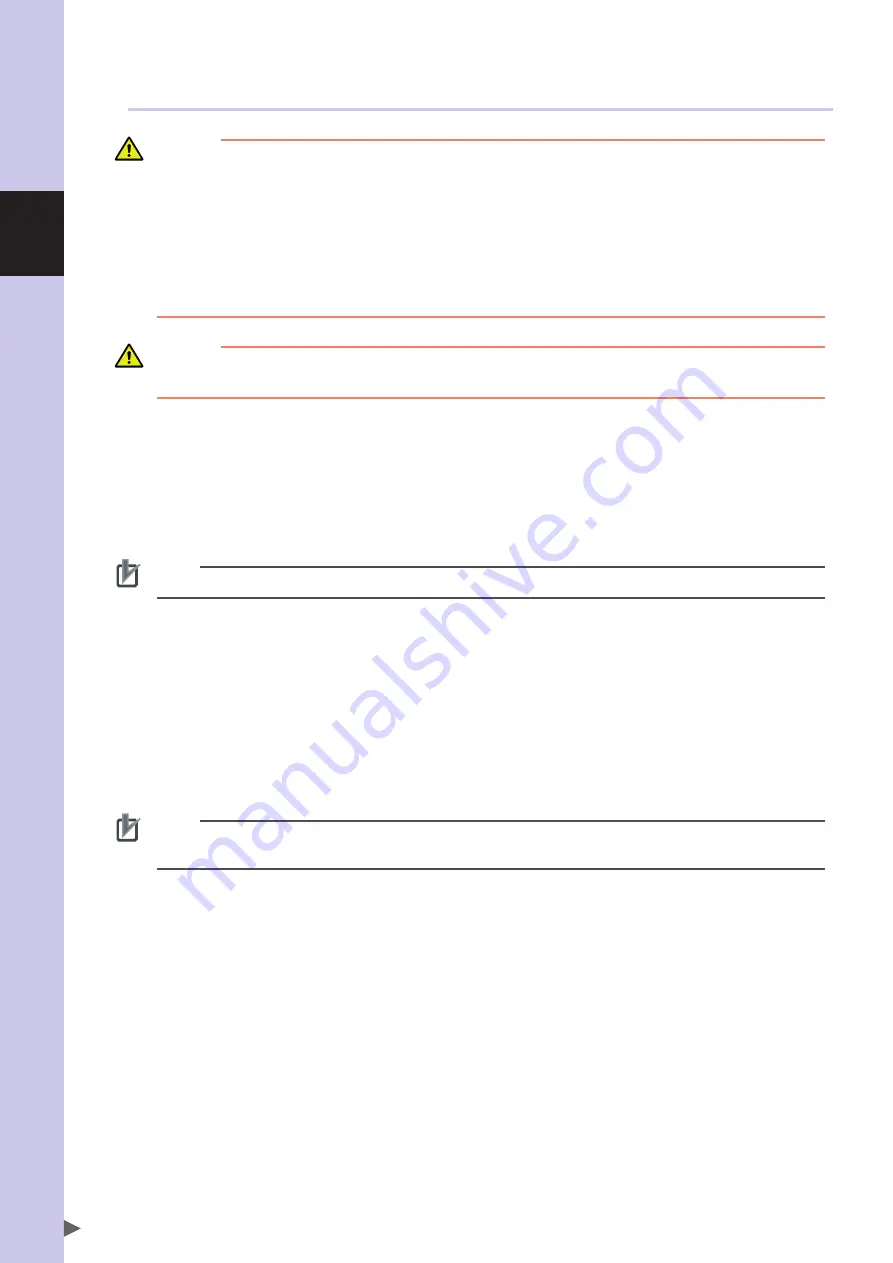
2
Installa
tion
2-16
2.3.2 Moving the R6YXG500, R6YXG600, R6YXGH600, R6YXG700, R6YXG800,
R6YXG900 and R6YXG1000
WARNING
SERIoUS InJURY mAY oCCUR IF THE RoboT FALLS And pInS SomEonE UndER IT.
• CHECK THAT THERE ARE no CRACKS And CoRRoSIon on THE EYEboLT InSTALLATIon. IF FoUnd, do noT USE
EYEboLTS To movE THE RoboT.
• SCREW THE EYEboLTS SECURELY InTo THE TAppEd HoLES UnTIL THE bEARInG SURFACE oF EYEboLT mAKES
TIGHT ConTACT WITH THE bEARInG SURFACE on THE ARm.
• USE A HoIST And RopE WITH CARRYInG CApACITY STRonG EnoUGH To SUppoRT THE RoboT WEIGHT.
• mAKE SURE THE RopE STAYS SECURELY on THE HoIST HooK.
• REmovE ALL LoAdS ATTACHEd To THE RoboT mAnIpULAToR End. IF AnY LoAd IS STILL ATTACHEd, THE
RoboT mAY LoSE bALAnCE WHILE bEInG CARRIEd, And ToppLE ovER CAUSInG ACCIdEnTS.
CAUTION
• When moving the robot by equipment such as cranes that require a license, only properly qualified personnel may operate it.
• The equipment and tools used for moving the robot should be serviced daily.
The following describes how to correctly and safely move the robot using the R6YXG500 as an example. Move also
the R6YXG600, R6YXGH600, R6YXG700, R6YXG800, R6YXG900 and R6YXG1000 in the same manner.
1
Lower the Z-axis from the origin position.
For the R6YXG500 and R6YXG600, lower the Z-axis approximately 24mm from its origin position.
For the R6YXGH600, R6YXG700, R6YXG800, R6YXG900 and R6YXG1000, lower the Z-axis approximately 33mm from
its origin position.
NOTE
The Z-axis is secured to the base with the arm clamp stay at shipment from the factory.
2
Turn off the controller.
3
Disconnect the robot cable from the controller.
4
Remove the bolts from the upper portion of the X-axis arm.
5
Clamp the arm.
Clamp the arm with the arm clamp stay, bolts, and washers (2 washers for R6YXG500 and R6YXG600, 1 washer for
R6YXGH600, R6YXG700, R6YXG800, R6YXG900 and R6YXG1000) that come with the robot.
If the arm position shown in the Fig. below cannot be obtained due to the X-axis and Y-axis additional mechanical stoppers,
remove the X-axis and Y-axis additional mechanical stoppers.
NOTE
Since the mechanical stoppers are installed to provide the maximum working envelope at shipment from the factory, the arm position
shown in the Fig. below can be obtained.
6
Tighten two eyebolts.
Tighten two eyebolts through washers into the upper portion of the X-axis arm. (The washers are also used when changing
the Y-axis mechanical stopper positions. So, if they are used, remove the washers and place them underneath the eyebolts.)
7
Secure the robot cable.
Wind the robot cable around the upper portion of the robot base so that it does not hinder the base mount, and then fasten the
cable end with adhesive tapes.
Summary of Contents for R6YXG500
Page 1: ...ZX T Series Cat No I155E EN 03A R6Y XG series INSTALLATION MANUAL SCARA Robots XG Series...
Page 2: ......
Page 10: ......
Page 36: ......
Page 38: ......
Page 40: ......
Page 46: ......
Page 48: ......
Page 56: ......
Page 174: ......
Page 176: ......
Page 220: ......
Page 221: ...Chapter 4 Periodic inspection Contents 1 Overview 4 1 2 List of inspection items 4 2...
Page 222: ......
Page 226: ......
Page 227: ...Chapter 5 Harmonic drive replacement period Contents 1 Overview 5 1 2 Replacement period 5 2...
Page 228: ......
Page 232: ......
Page 238: ......
Page 240: ......
Page 244: ......
Page 246: ......
Page 323: ...8 Specifications 8 77 1 3 Robot inner wiring diagram Robot inner wiring diagram R6YXG500...