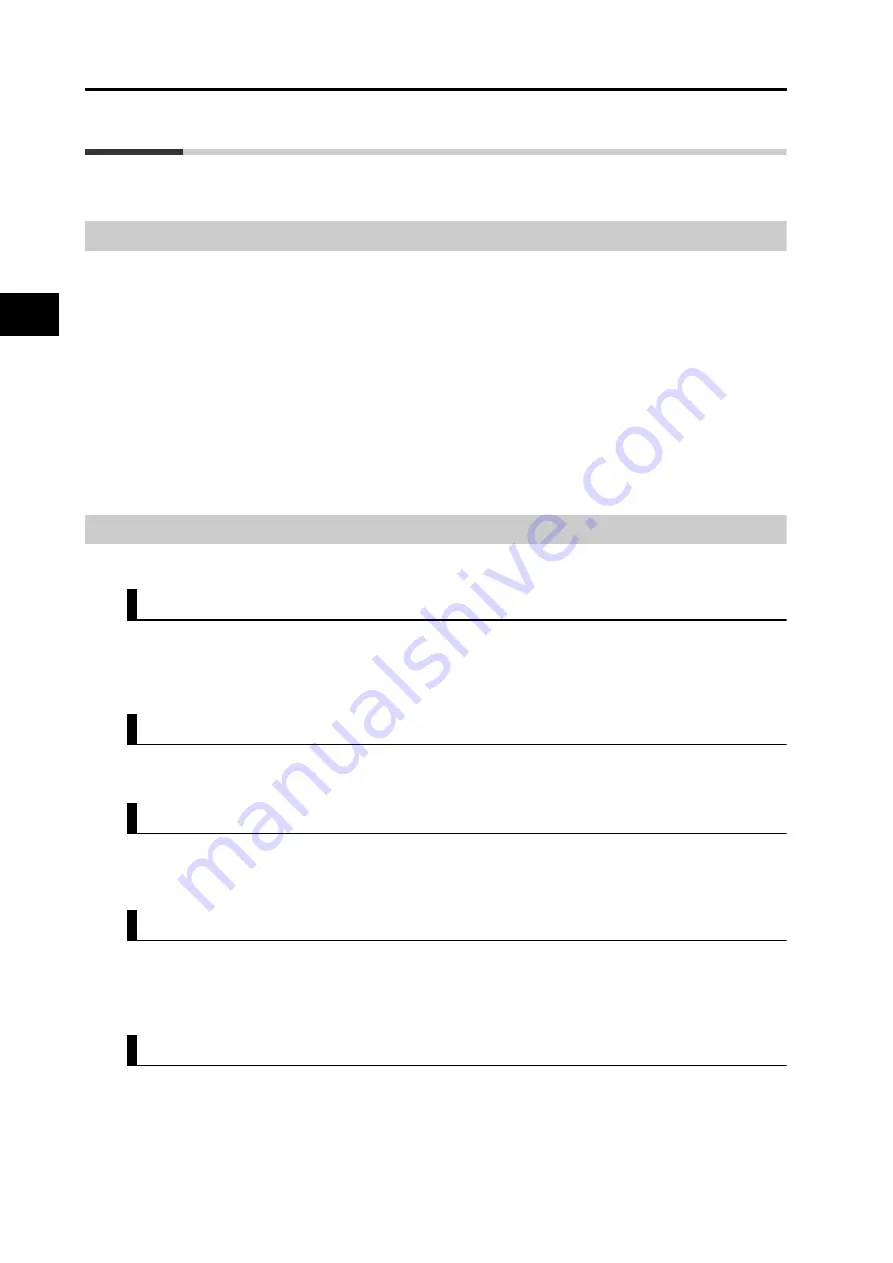
1-1
1-1 Outline
1
OMNUC G5-SERIES AC SERVOMOTOR AND SERVO DRIVE USER'S MANUAL
Features and System Configuration
1-1 Outline
Outline of the OMNUC G5 Series
With the OMNUC G5 Series, you can perform full closing control in addition to position control,
speed control and torque control.
Various models are available supporting wide-ranging motor capacities from 50 W to 5 kW and input
power supplies from 100 to 400 V. You will surely find a model that best suits your application.
Motors with high-resolution 20-bit incremental encoders and 17-bit absolute/incremental
encoders are available as standard models.
The OMNUC G5 Series features realtime autotuning function and adaptive filter function that
automatically perform complicated gain adjustments. A notch filter can also be automatically
set to suppress machine vibration by reducing machine resonance during operation.
The damping control function of the Servomotor and Servo Drive realizes stable stopping
performance in a mechanism which vibrates because of the low rigidity of the load.
Features of the OMNUC G5 Series
The OMNUC G5 Series has the following features.
7 Possible CONTROL modes Switching
You can switch among 7 CONTROL modes including the following: (1) position control, (2)
speed control, (3) torque control, (4) position and speed control, (5) position and torque control,
(6) speed and torque control, (7) full closing control. Desired modes can be selected with the
flexible driver according to your need. A single driver supports various applications.
Achievement of Accurate Positioning by Full Closing Control
Feedbacks from the external scale connected to the motor are used to accurately control positions.
Accordingly, position control is not affected by deviation caused by ball screws or temperature.
Wide Range of Power Supplies to Match Any Necessity
The OMNUC G5 Series now has models supporting 400 V for use with large equipment, at
overseas facilities and in wide-ranging applications and environment. Since the utilization ratio
of facility equipment also increases, the TCO (Total Cost of Ownership) will come down.
Safe Torque OFF (STO) Function to Ensure Safety
You can cut off the motor current to stop the motor based on a signal from an immediate stop
button or other safety equipment. In addition to the conventional stop method based on a
control signal, the STO function that permits direct stopping without a need to involve the
control circuit provides the immediate stop from 2 systems, thereby enhancing safety.
Suppressing Vibration of Low-rigidity Mechanisms during Acceleration/Deceleration
The damping control function suppresses vibration of low-rigidity mechanisms or devices
whose tips tend to vibrate.
2 vibration filters are provided to enable switching the vibration frequency automatically
according to the rotation direction and also via an external signal. In addition, the settings can
be made easily merely by just setting the vibration frequency and filter values, and you are
assured of stable operation even if the set values are inappropriate.