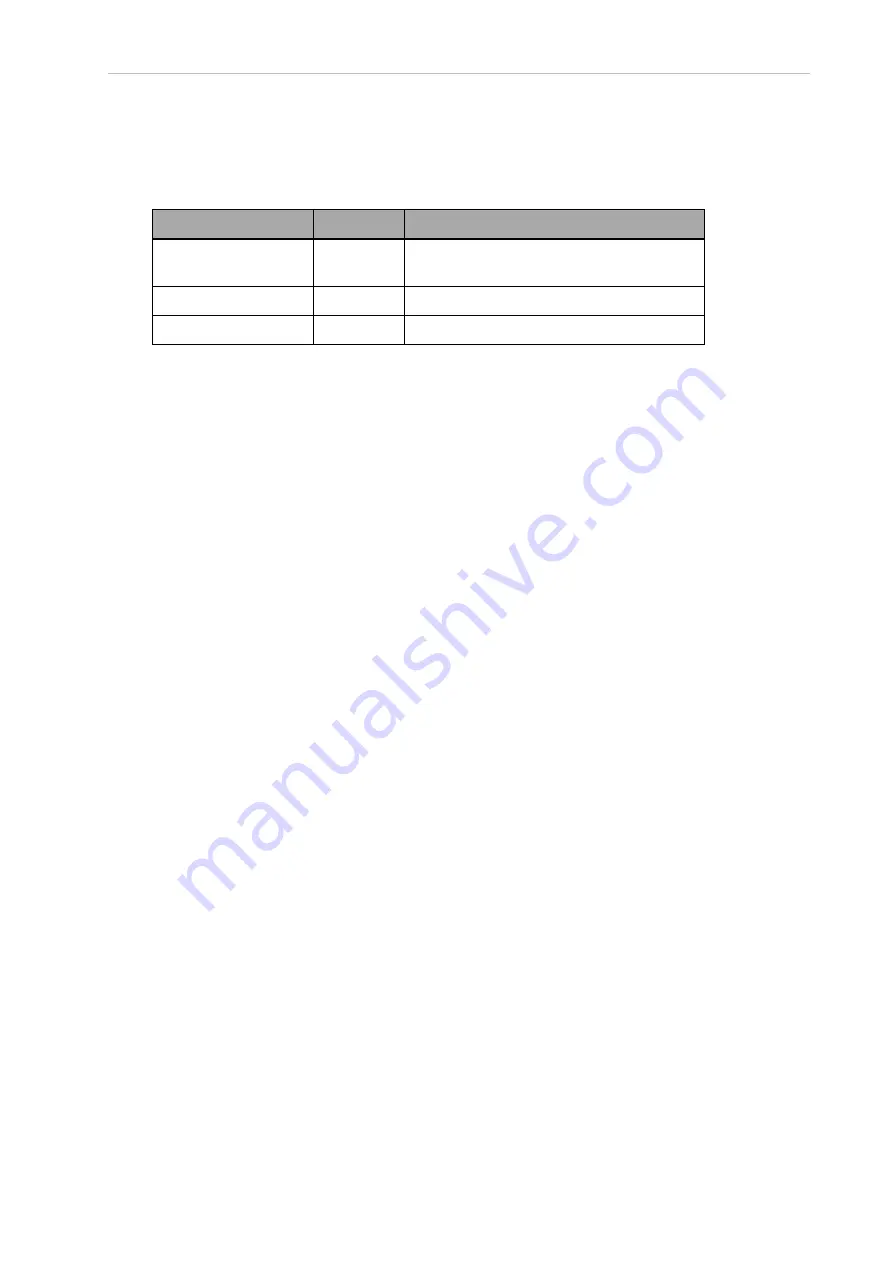
102
iX3 565 Robot with EtherCAT User’s Manual
22792-000 Rev. A
6.4 Checking Safety Systems
NOTE:
The following cleaning actions and intervals are suggestions only. Refer
to HACCP guidelines to determine what is required for your installation.
Table 6-3. Typical Cleaning Schedule
Item
Interval
Suggested Cleaning Action
Outer Arms and Ball
Studs
1 Week
Clean with wipes or water.
Platform
1 Week
Clean with wipes, air, or water.
Entire robot
1 Week
Clean In Place
Water Shedding
Surfaces of the robot have been designed to shed water. This increases the likelihood that con-
taminants or cleaning agents will drain with a wash-down procedure.
6.4 Checking Safety Systems
Use the following steps to check all robot safety devices that may be present in the system.
These tests should be performed at least every six months.
IMPORTANT:
Operating any of the following safety devices should disable
robot high power.
The High Power indicator must be operational to satisfy safety requirements.
l
E-stop button on the Front Panel or connected to the XSYSTEM cable.
l
E-stop button and enabling switch on the pendant (if present).
l
Any other user-supplied safety devices that have been installed in the robot system.
High Power Indicator Check
The robot monitors current used by the High Power indicator. This is to ensure that a High
Power indicator device is connected and functioning properly to satisfy safety requirements.
If the robot does not detect a current between 10 mA to 500 mA when High Power is requested,
an error condition (-924) *Front panel HIGH POWER lamp failure* will be present and High
Power will not be enabled.
The High Power indicator needs to be periodically checked for correct functionality. The fol-
lowing considerations should be made before beginning the High Power indicator check pro-
cedure.
l
Control power and High Power needs to be available.
l
All connected safety devices must be capable of providing signals for a safe state.
l
The robot High Power needs to be disabled and robot motions will not execute during
this procedure.
l
High Power safety timeout must be enabled to allow the indicator to flash after a High
Power request is made. The recommended setting is 10 seconds. Refer to the
Sysmac Stu-