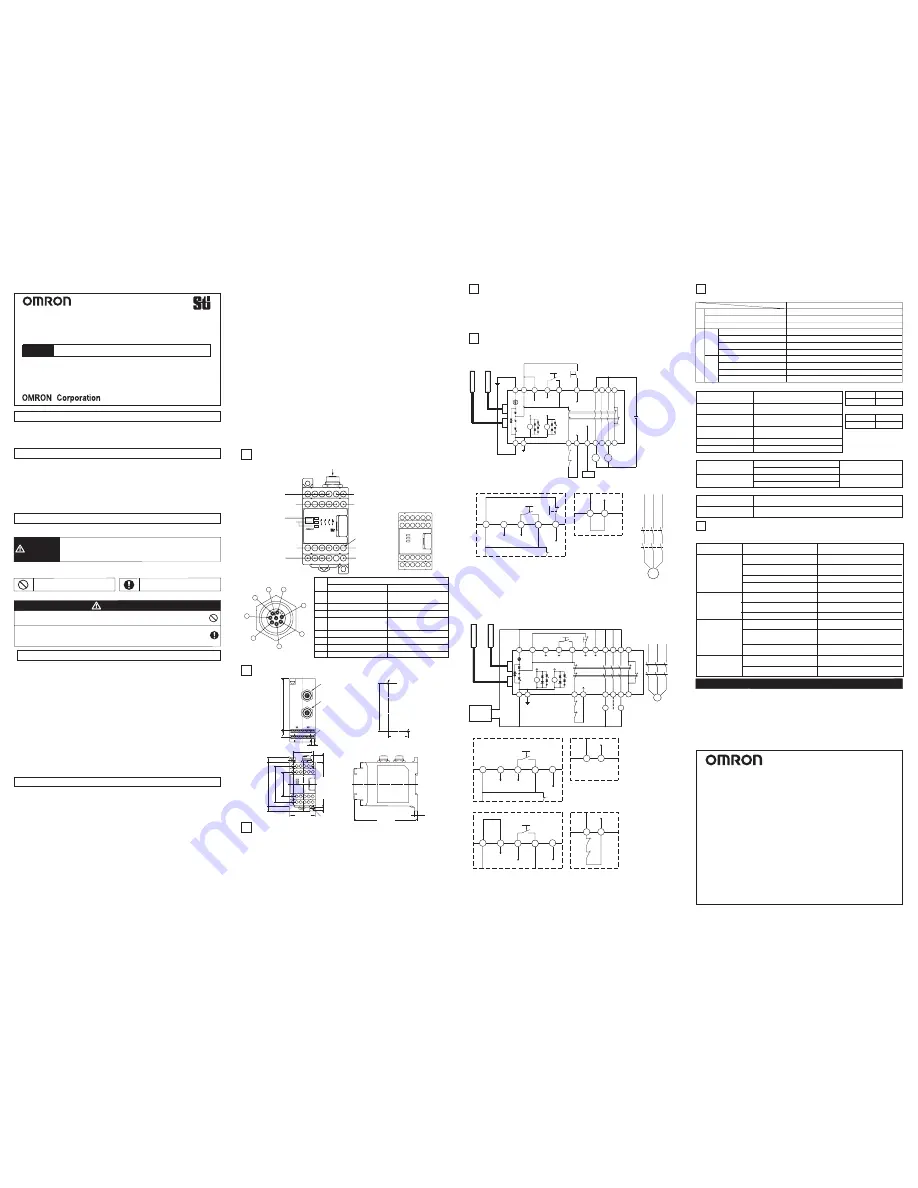
*S1 Open: Normal light emission.
Close: Stop light emission.
●
Wiring for Auto-reset mode.
●
Wiring for Manual reset mode and the EDM function enabled
●
Wiring when the EDM is not used.
●
Wiring when the EDM is not used.
*S3 If the switch is not necessary,
connect between X1 and H1.
4
Functions
Designation
The F3SP-B1P can construct the condition conforming to cat. 4 / PLe or cat.2 / PLc requested by EN
ISO13849-1 with combination as follows:
- Category 4 / PLe:
Type F3SN-A
□□□□
P
□□
or F3SH-A09P03 or F3SR-430B
□□□□
or
F3SJ-A
□□□□
P
□□
or F3SJ-B
□□□□
P25
- Category 2 / PLc:
Type F3SN-B
□□□□
P
□□
Note: Category is not judeged only by the condition above, but is judged by the
condition of the whole control system.
- In order to be cat. 4/ PLe, or cat. 2/ PLc
1. The NC contact from a contactor is required to feed back signal.
(Refer to the application examples. For category 2, it is not mandatory.)
2. PE terminal should be connected to protective earth.
3. In application with long term operation of devices, the F3SP-B1P must have cyclic
operation every 24 hours at least in order to detect failures and a failure
accumulation.
Application examples
5
●
Wiring for the Manual reset mode and the EDM function.
5-1 When in combination with the F3SN/F3SH/F3SJ
5-2 When in combination with the F3SR
Specifications
●
Characteristics
(1) When ready for wiring, the power source should be disconnected first. Further, at operating
this unit, the terminal cover should be closed correctly in orde to prevent an electrical shock.
(2) Do not wire in case threat of Lightning. otherwise an electric shock may occur.
(3) Do not apply any excessive voltage or current to the input or output circuit the F3SP-B1P.
Doing so may result in damage to the F3SP-B1P or cause afire.
(4) Do not apply any variable voltage, otherwise F3SP-B1P may malfunction.
(5) Do not connect any overload to the output circuit, otherwise the F3SP-B1P in operation will
generate excessive heat and the output elements of the F3SP-B1P may short-circuit or fire
may result.
(6) The lifetime of F3SP-B1P depends on the conditions of switching of its outputs. Be sure to
conduct its test operation under actual operating conditions in advance and use it within
appropriate switching cycles. Change the F3SP-B1P before expected operation. Over
operation may cause may short-circuit or may malfunction.
(7) Do not operate the F3SP-B1P with flammable or explosive gass. An arc with operation and
the heat of relay will cause a fire or an explosion.
(8) Do not disassemble, repair, or modify the F3SP-B1P, otherwise an electric shock may occur or
the F3SP-B1P may malfunction.
(9) Use protective device (Fuse etc) for short-circuit protection and ground fault protection,
otherwise a fire may occur or the F3SP-B1P may malfunction.
(10) Be sure to wire correctly. The sensor connector is the same both the emitter and the
receiver.
(11) Do not dismantle, repair, or modify F3SP-B1P. it may lead to loss of its safety functions.
(1) For malfunctions in case that the power supply picks up gradually.
Malfunctions in case that the power supply picks up gradually. In case that the input circuits
close before the power supplies, internal logic may malfunction.
(2) Handling
Do not drop the F3SP-B1P or shock or vibrate the F3SP-B1P excessively. Doing so may result
in damage to the F3SP-B1P or cause F3SP-B1P to malfunction.
(3) For adhesion of solvent
Adhesion of solvent, likely Alcohol, Thinner, Trichloroethane, Gasoline, on the product should
be prohibited. Such solvent cause erasing the marking and being inferior of the parts.
(4) Take appropriate and sufficient countermeasures when installing systems in the following
locations. Inappropriate and insufficient measures may result in malfunction.
1. Locations subject to static electricity or other forms of noise.
2. Locations subject to possible exposure to radioactivity.
3. Locations close to power supplies.
(5) Wiring
1. Use the following to wire the F3SP-B1P.
- Stranded wire (Flexible wire): 0.75 to 1.5mm
2
- Solid wire: 1.0 to 1.5mm
2
2. The F3SP-B1P may malfunction or generate heat.
- Tighten each screw to a torque of 0.78 to 1.18N
・
m
3. PE is a ground terminal. When machine is grounded at the positive, the PE terminal
should not be grounded.
4. NC terminals do not have any function. Do not wire them.
The following functions of the sensor can be used. Refer to the instruction manual of
the sensor for detailed information.
・
Auto reset
/
Manual reset (Interlock function)
・
External device monitoring (EDM)
・
External test (Light emission stop function by test input)
・
Auxiliary output (PNP transistor output)
(
*)
*
When in combination with the F3SR, "auxiliary output" can not be used.
The F3SP-B1P received the following approvals in combination with the
F3SN/F3SH/F3SR/F3SJ:
・
From EU accredited body TUV-SUD Product Service GmbH:
- EC Type-examination in accordance with the EU Machinery Directive
Approved standards: EN61496-1, CLC/TS 61496-2 (IEC61496-2)
・
From the Third Party Assessment Body UL:
- UL Listed to U.S. and Canadian safety standards
Approved standards: IEC61496-1, IEC61496-2,
UL508, CAN/CSA C22.2 No.14, CAN/CSA C22.2 No.8
●
Ratings
6
Thank you for purchasing F3SP-B1P Control Unit.
Please read and understand this manual before using the products.
Keep this manual ready to use whenever needed.
Only qualified person trained in professional electrical technique should handle F3SP-B1P.
Since this instruction sheet only provides general infomation, refer to the instruction
manual of the sensor.
Please consult your OMRON representative if you have any questions or comments.
USER'S MANUAL
Type F3SP-B1P
Jul. 2011
English
WARNING
Precaution for Safe Use
Indicates a potentially hazardous situation which, if not avoided,
will result in minor or moderate injury, or may
result in serious injury or death.
Additionally there may be significant property damage.
Meanings of Signal Words
The following signal words are used in this manual.
Meaning of Alert Symbols
The following alert symbols are used in this manual.
Serious injury may possibly occur due to breakdown of safety outputs.
Do not connect loads beyond the rated value tothe safety outputs.
Serious injury may possibly occur due to loss of required safety functions.
Wire F3SP-B1P properly so that supply voltages or voltages for loads do
NOT touch the safety inputs accidentally or unintentionally.
WARNING
Alert Statements
Control Unit
For F3SN-A
□□□□
P
□□
, F3SN-B
□□
P
□□
, F3SH-A09P03,
F3SR-430B
□□□□
, F3SJ-A
□□□□
P
□□
, F3SJ-B
□□□□
P25
Indicates prohibited actions
Indicates mandatory actions
Precautions for Safe Use
Precautions for Correct Use
●
Life expectancy
Electrical endurance
Mechanical endurance
100,000 operations MIN. Rated load
Switching frequency 1,800 operations/h
5,000,000 operations MIN.
Switching frequency 18,000 operations/h
●
Isolation specification
Insulation resistance
Dielectric strength
Between different poles of output
Between different poles of output
Between inputs and outputs
Between inputs and outputs
100Mohm MIN.
(by 500VDC Megger)
2,500VAC 1min.
7
Failure detection
Type F3SP-B1P can detect the failure for the safety of internal circuit, parts condition and
external wiring.
K1 and K2 LED
do not turn on.
Failures of the parts
of the internal circuits.
Replace with a new product.
Failures involving the wiring
of External input. (input line)
Failure indication
by LED
Failure condition
K1 or K2 LED
does not turn on.
Power LED
does not turn on.
Checking points and measures
to take
Failures involving the wiring
of External input. (input line)
Failures of the parts of the
External devices. (Contactor etc)
Failures of the parts
of the internal circuits.
Replace with a new External devices.
(Contactor etc)
Failures of the parts
of the internal circuits.
Replace with a new product.
Supply voltage outside
the rated value.
Check the supply voltage to
Expansion.
Failures involving the wiring
of External input. (output line)
Replace with a new product.
Check the wiring to External input.
(input line)
Check the wiring to External input.
(output line)
Check the wiring to External input.
(input line)
Failures of the parts of the
Protective device. (Fuse etc)
Replace with a new Protective device.
(Fuse etc)
All LED turn on.
but the safety
output doesn't on.
Failures involving the wiring
of External input.
(input line / power line)
Check the wiring to External input.
(input line/power line)
Failures of the Sensor.
Failures of the Sensor.
Check the Sensor.
Check the Sensor.
S1: External test switch
S2: Interlock / Lockout reset switch
S3: Lockout reset switch
KM1,KM2: Magnet contactor
M: 3-phase motor
S1: External test/Lockout reset switch
S2: Interlock reset switch
KM1,KM2: Magnet contactor
M: 3-phase motor
E1: 24 VDC power supply (S82K)
1.7W MAX.
(
Exclude sensor power)
24VDC
25VAC
60VDC
5A
AC: 1250VA
DC: 150W
AC: 125VA
DC: 150W
TYPE F3SP-B1P
Rated power consumption
Rated supply voltage
Operating voltage range
Input
Rated load
Rated carry current
Max. switching voltage
Max. switching capacity
Output
For Nor
th
America
Rated load
Rated carry current
Max. switching voltage
Max. switching capacity
For E
ur
ope
5A
250VAC 5A cos
φ
=1 30VDC 5A L/R=0ms
250VAC 125VDC
-15% to +10% of rated supply voltage
25VAC 5A cos
φ
=1 30VDC 5A L/R=0ms
OMRON shall not be responsible for conformity with any standards, codes, or
regulations that apply to the combination of the products in the customer's
application or use of the product.
Take all necessary steps to determine the suitability of the product for the
systems, machines, and equipment with which it will be used. Know and
observe all prohibitions of use applicable to this product.
NEVER USE THE PRODUCTS FOR AN APPLICATION INVOLVING SERIOUS RISK
TO LIFE OR PROPERTY WITHOUT ENSURING THAT THE SYSTEM AS A WHOLE
HAS BEEN DESIGNED TO ADDRESS THE RISKS, AND THAT THE OMRON
PRODUCT IS PROPERLY RATED AND INSTALLED FOR THE INTENDED USE
WITHIN THE OVERALL EQUIPMENT OR SYSTEM.
Suitability for Use
OMRON EUROPE B.V. (Representative in EU)
Wegalaan 67-69, NL-2132 JD Hoofddorp
THE NETHERLANDS
PHONE 31-2356-81-300 FAX 31-2356-81-388
OMRON SCIENTIFIC TECHNOLOGIES INC.
6550 Dumbarton Circle, Fremont CA 94555-3605
U.S.A
PHONE 1-510-608-3400 FAX 1-510-744-1442
OMRON ASIA PACIFIC PTE. LTD.
438A Alexandra Road # 05-05/08,
Alexandra Technopark Singapore 119967
SINGAPORE
PHONE 65-6-835-3011 FAX 65-6-835-2711
Note: Specifications subject to change without notice.
OMRON Corporation
Shiokoji Horikawa, Shimogyo-ku, Kyoto, 600-8530
JAPAN
Original instructions
EC Declaration of Conformity
Standards
OMRON declares that Type F3SP-B1P is in conformity with the requirements of
the following EC Directives:
- EMC Directive: 2004/108/EC
- Machinery Directive: 2006/42/EC
OMRON (CHINA) CO., LTD.
Room 2211, Bank of China Tower, 200 Yin Cheng Zhong Road,
PuDong New Area, Shanghai, 200120, China
PHONE 86-21-5037-2222 / FAX 86-21-5037-2200
●
Protection class
Operation time
100ms MAX.
(exclude sensor response time)
Destruction: 300 m/s
2
Malfunction: 100 m/s
2
Ambient humidity
Ambient temperature
Shock resistance
Vibration resistance
Response time
-10 to 55
℃
10ms MAX.
(exclude sensor response time)
35 to 85%RH
10 to 55Hz 0.35mm single amplitude
(0.7mm double amplitude)
IP20
IP40
3
2
Enclosure
Terminals
●
Pollution degree
External
Internal
(6) Mounting multiple units
When mounting multiple units close to each other, the rated current will be 3A.
Do not apply a current higher than 3A.
(7) Operating and Storage Environment
Do not operate or store the F3SP-B1P under the following conditions.
Doing so may result in damage to the F3SP-B1P or cause the F3SP-B1P to malfunction.
1. The places with direct sunlight.
2. The places with ambient temperature ranges not within -25 to 55
℃
.
3. The places with rapid temperature changes resulting in condensation or relative humidity
ranges not within 35 to 85%RH.
4. The places with atmospheric pressure out of the range 86 to 106kpa.
5. The places with corrosive or inflammable gas.
6. The places with water, oil, or chemical sprayed on the F3SP-B1P.
7. The places with vibration or shock affecting the F3SP-B1P.
8. The places with atmosphere containing dusts, saline or metal powder.
(8) DC power supply units
In order to conform to IEC61496-1 and UL508, DC power supply unit must satisfy all the
conditions mentioned in the instruction manual the sensor.
(9) Installation
1. Cabinet of F3SP-B1P should meet IP54 protection.
2. The F3SP-B1P is exclusively for F3SN-A
□□□□
P
□□
, F3SN-B
□□□□
P
□□
,
F3SH-A09P03,
F3SR-430B
□□□□
, F3SJ-A
□□□□
P
□□
, F3SJ-B
□□□□
P25 series.
3. The following functions are set with two short pieces when delivered. Change wirings
depending on necessary functions.
- H1-X1 short: Auto reset mode.
- T31-T32 short: EDM function is inactive.
*
These combinations of wiring and function are for the use with the F3SN/F3SH or F3SJ.
When in combination with the F3SR, refer to Section 5.
(10) For feedback purpose use devices with contacts capable of switching micro loads of
24VDC, 5mA.
(11) This is a class A product. In residential areas it may cause radio interference, in which case
the user may be required to take adequate measures to reduce interference.
KM1
24VDC
KM1
KM2
KM2
S2
S1
PLC
EMITTER
RECEIVER
K1
K2
K1
K2
A1
H1
L1
J1
H1
X1
A2
PE
T31
T32
P1
41
33
23
13
42
34
24
14
INTERLOCK
TEST
RESET
AUXILIARY
EDM
OSSD2
OSSD1
S3
S1
H1
L1
J1
H1
X1
T31
T32
INTERLOCK
TEST
RESET
KM1
M
KM2
●
Wiring when the EDM is used.
●
Wiring for Auto-reset mode.
●
Wiring for Auto-reset mode.
S1
S2
A1
H1
L1
J1
H1
X1
P1
13
23
33
41
KM1
KM2
Function
select input
TEST
RESET Operating
range
select input
OSSD 1
OSSD 2
K1
K2
K1
K2
A2
PE
T31
T32
EDM
14
24
34
42
KM1
KM2
KM1
KM2
F3SP-B1P
E1
24VDC
0V
M
Emitter
Receiver
Function
select input
TEST
RESET
S1
H1
L1
J1
H1
X1
T31
T32
EDM
H1
Function
select input
TEST
RESET
S1
L1
J1
H1
X1
T31
T32
EDM
H1
1
External Physical Dimensions
2
●
Unit
For safety category and PL
3
43
63
76 M
A
X.
9
7×5=35
13 M
A
X.
45 MAX.
R2.3
111 MAX.
5
5.6
9
4.6 dia.
35±0.3
5.9
24-M3
Emitter
Receiver
10.5
91
84
±0.3
Two,4.2 dia. or M4
Mounting holes
Sensor connectors For Receiver(Black)
For Emitter(Gray)
Output terminals
Power input
terminal
Output terminals
Power input
terminal
Earth terminal
I/O terminals
Input power
indicator
Relay operation
indicators
I/O terminal
I/O terminals
I/O terminals
Type F3SP-B1P
13
23
33
41
H1
J1
NC
NC
L1
H1
X1
A1
14
13
24
23
34
33
42
41
P1
34
42
24
14
A2
PE
T32
T31
NC
NC
NC
PWR
K
1
K
2
No.
13 23 33 41
14 24 34 42
T31 T32
A1
X1
H1
H1 J1
L1
NC NC
PE
NC NC
A2
P1
NC
24 VDC
SAFETY LIGHT CURTAIN
CONTROL UNIT
F3SP-B1P
●
Connector
Pin
No.
Signal Name
Receiver
1
2
4
5
6
7
3
RS-485 (A)
Auxiliary output
(* Operating range
select input)
OSSD 1
+24V
OSSD 2
EDM input
*Names used when connecting with the F3SR
0V
RS-485 ( B )
NC
RS-485 ( B )
RS-485 ( A)
Reset input
Test input
+24V
Interlock selection input
(* Function select input)
Emitter
0V
8
1
2
7
6
5
4
3
8
KM1
KM2