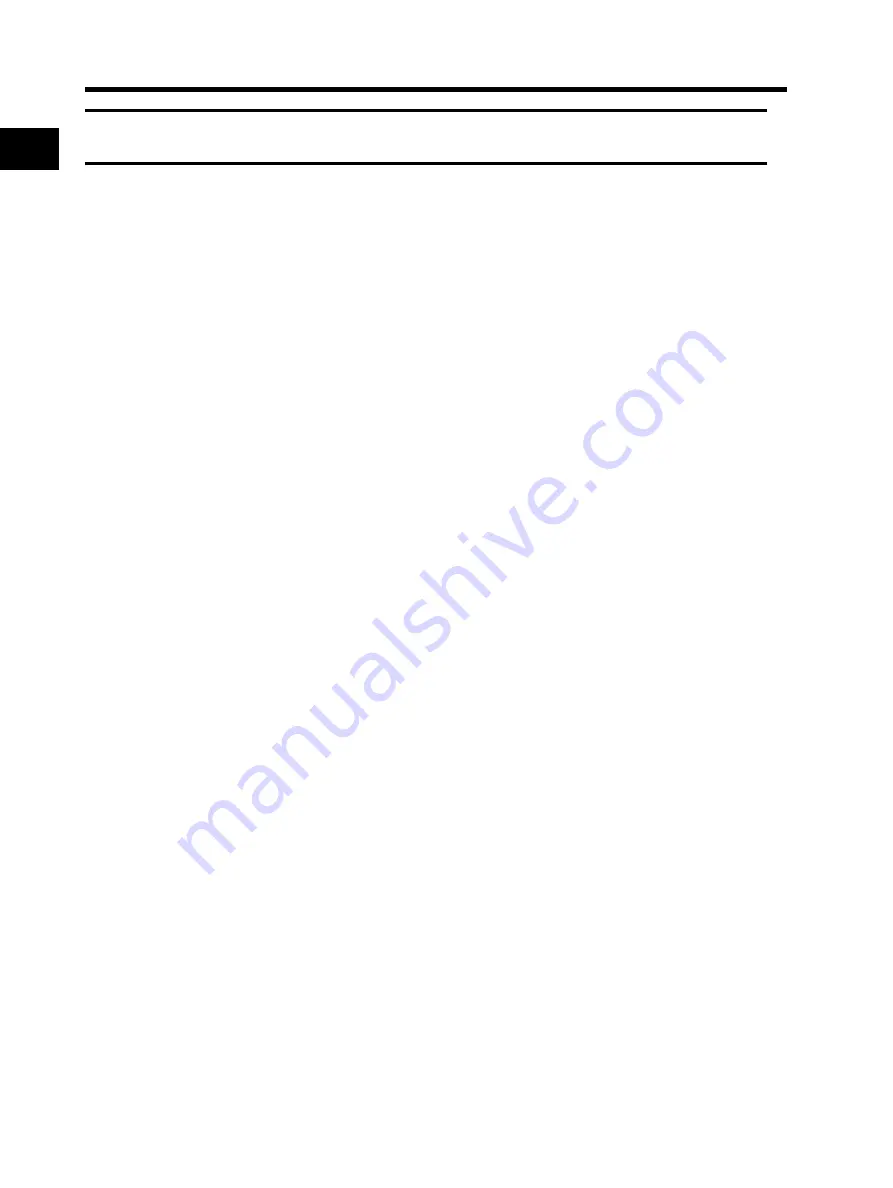
1-1
1-1 Overview
1
Overview
1Overview
1-1 Overview
The DI Board (3G3AX-DI) is an optional board for the 3G3RX Series Inverter.
With this board, you can digitally input the set frequency, acceleration time setting, deceleration time
setting, torque setting and position (orientation stop position) setting.
Note that the PG Board (3G3AX-PG) is required separately for position control through position set-
ting inputs.
Summary of Contents for 3G3AX-DI
Page 1: ...Cat No I565 E1 01 USER S MANUAL 3G3AX DI DI Board ...
Page 2: ......
Page 14: ...12 Contents ...
Page 15: ...Chapter 1 Overview 1 1 Overview 1 1 ...
Page 41: ......