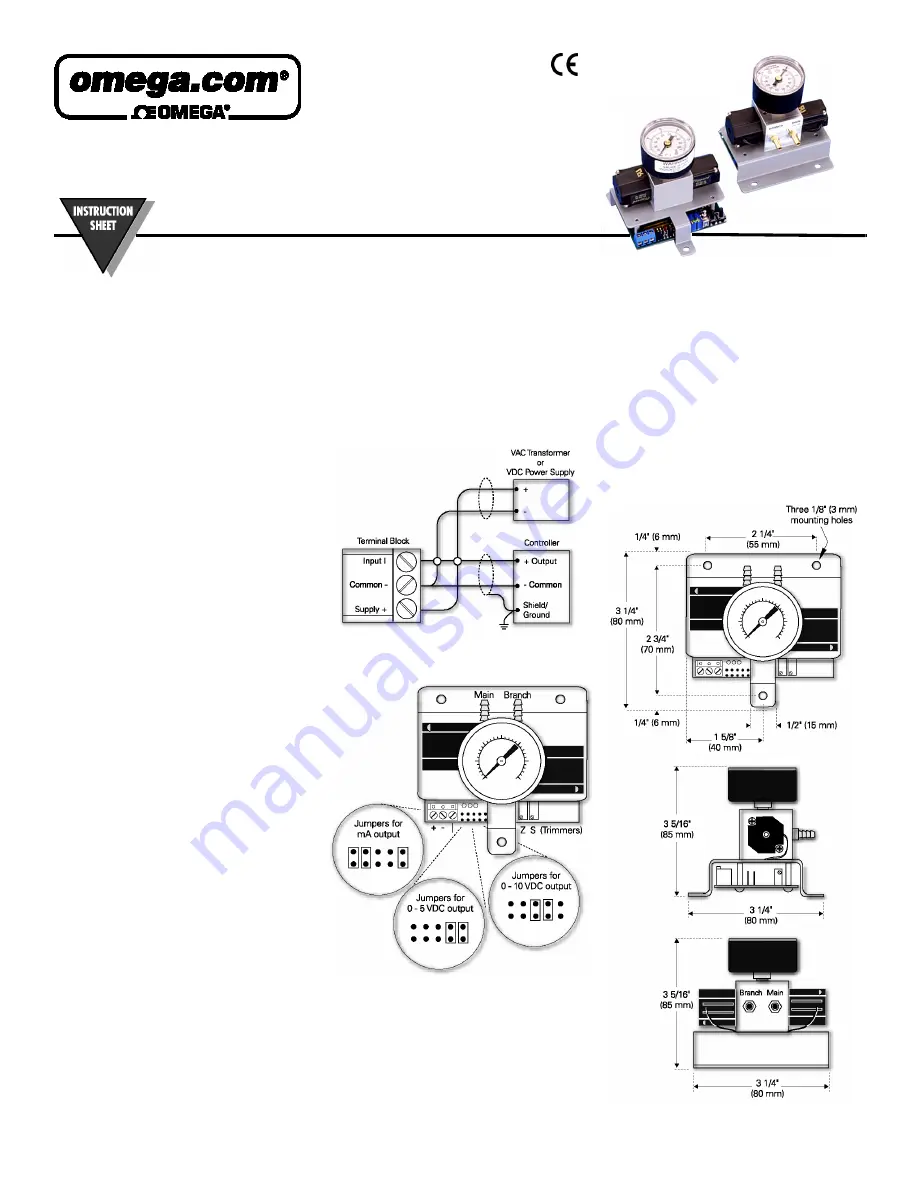
Electropneumatic Transducer
IP-411 and IP-413
M2073/0303
SPECIFICATIONS
Accuracy
*
:
±
1%
FS
Maximum Supply Pressure
: 40
PSIG
Pressure Differential
: 0.1
PSIG
(supply to branch)
Supply Voltage
: 18 to 28
VAC
or
VDC
Supply Current
:
150
M
A
Enclosure
: 18 Ga. C.R. steel chassis
Finish
:
Baked on enamel PMS2GR88B
Conformance
: EMC standards EN50082-1(1992),
EN55014(1993)/EN60730-1(1992)
Compensated Temperature Range
: 25°
F
to 150°
F
(4°
C
to
65°
C
)
T. C. Error
:
±
0.025%/°
F
(.03%/°
C
)
Media Compatibility
: Clean dry air or any inert gas
Port Connection
: ¼-inch O.D. poly tubing
Environmental
: 10 to 90%
RH
non-condensing
Termination
: Screw terminal block
Wire Size
: 12 Ga. maximum
Input Impedance
: 301 ohms (4 - 20
M
A
); 10K ohms
(0 - 5 or 0 - 10
VDC
)
Weight
: 1.0 lb. (.45 kg)
*
Includes nonlinearity, hysteresis, and non-repeatability.
INSTALLATION PRECAUTIONS
Do not use on an oxygen service, in an explosive or
hazardous environment, or with flammable or combustible
material.
Disconnect the power supply before installing the transducer.
Failure to do so can result in electrical shock and equipment
damage.
Make all connections in accordance with the job wiring
diagram and national and local electrical codes. Use only
copper conductors.
Use electrostatic discharge precautions such as wrist straps
when installing and wiring the transducer.
Do not exceed ratings for the transducer.
This transducer contains a half-wave rectifier power supply
and must not be powered from transformers powering other
devices with non-isolated full-wave rectifier power supplies.
Verify that the main supply pressure does not exceed 40
PSIG
.
Ensure a minimum of 6 to 10 feet (1.8 to 3.0 m) of tubing
between the transducer and the actuator.
For a 24
VAC
supply voltage, make sure that the hot and
neutral are not reversed. If more than one transducer is being
powered from the same transformer, the hot and neutral
should be the same for each transducer.
MOUNTING
The electropneumatic transducer must be mounted in an
upright position so that the main and branch ports face
upwards and the gauge can be read easily.
1.
Select the mounting location.
2.
Mount the transducer on a vertical surface with three
#8 self-tapping screws (not provided).
3.
Pull wires through the bottom of the transducer and
make the necessary connections.
4.
Make the pneumatic connections.
WIRING
Use maximum 12
AWG
wire for wiring terminals and flexible
¼-inch O.D. poly tubing for main and branch pneumatic
connections. The electropneumatic transducer can be
powered with a 18 to 28
VAC
or
VDC
supply.
1.
Connect the power supply voltage wire to the supply
[+] terminal and the power supply common to the
common [-] terminal.
2.
Connect the controller output wire to the input [I]
terminal and the controller common wire to the
common [-] terminal.
JUMPER CONFIGURATIONS
Jumper configuration varies by output type:
M
A
or
VDC
.
CHECKOUT
To verify proper operation of the transducer, adjust the input
signal to obtain a maximum output pressure for the
appropriate range. The output should be 15 or 20
PSIG
. Next,
adjust the input signal to obtain a minimum output pressure.
The output should be 0 or 3
PSIG
.
CALIBRATION
All electropneumatic transducers are factory calibrated to
meet or exceed published specifications. If field adjustment is
necessary, follow these instructions:
1.
Connect air to the Main port.
2.
Connect an accurate gauge to the Branch port using a
minimum of 6 to 10 feet (1.8 to 3.0 m) of tubing.
3.
Connect an 18 to 28 VAC or VDC power source to the
[+] and [-] terminals. The maximum supply voltage
should not exceed 30
VAC
/
VDC
.
4.
Apply a low input signal to the [-] and [I] terminals
(0
VDC
or 4
M
A
).
5.
Adjust [Z] to obtain the desired low output pressure.
6.
Apply a high input signal to the [-] and [I]
terminals (5/
10
VDC
or 20
M
A
).
7.
Adjust [S] to obtain the desired high output pressure.
8.
Repeat steps 4 through 7 until the transducer is fully
calibrated.
DIMENSIONS
Summary of Contents for IP-411
Page 2: ...Manual REVISION ...