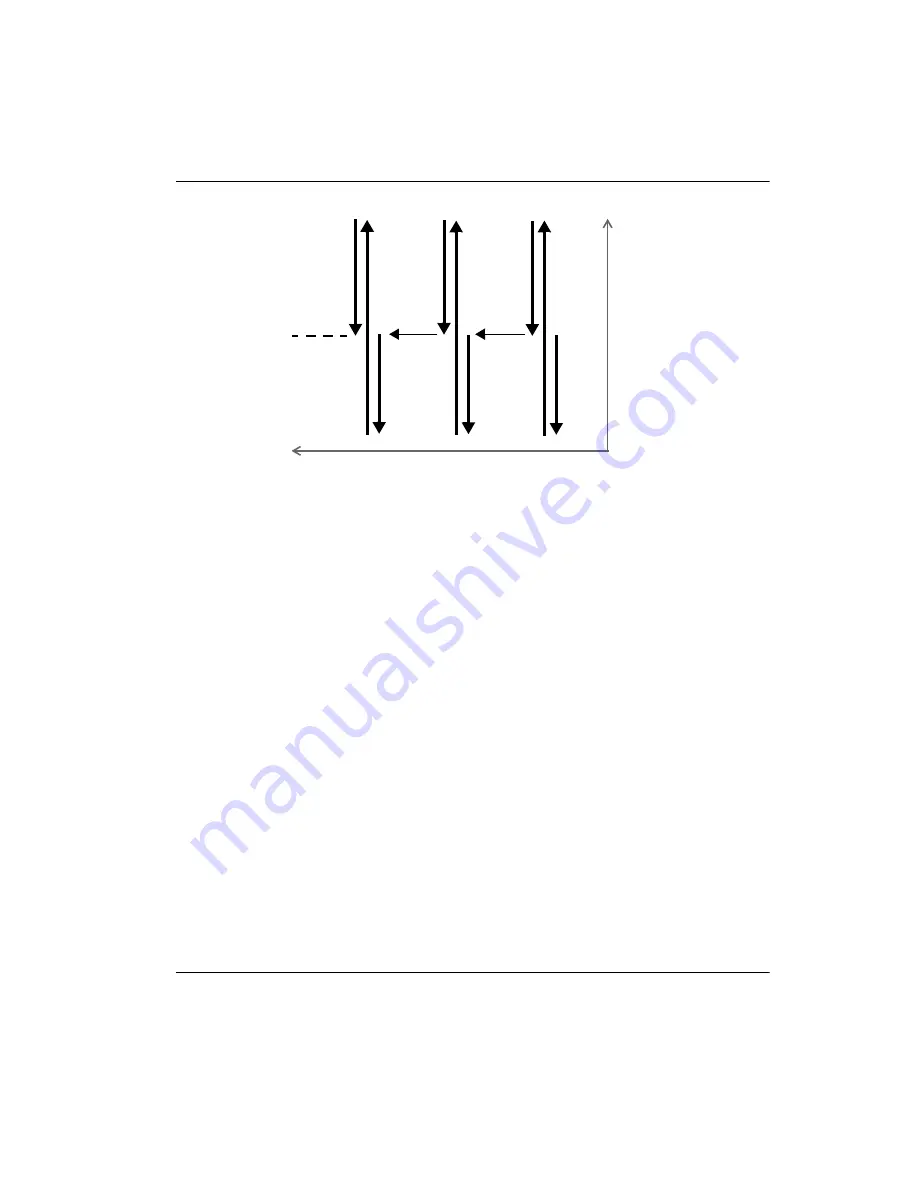
10-003591-01EN [Q7780031], Rev. 4, January 2020
Setup of Equipment
25
Figure 2-2 Symmetrical scan pattern for a pipe elbow inspection of 360°
In a symmetrical scan pattern, the indexing button is pressed once after completing a
scan, which stops the acquisition and activates the button’s red LED. Because of its
“smart indexing” function, the FlexoFORM scanner can then freely move along the
index axis to the next scan line without overwriting any acquisition data. When the
scanner is in position at the center of the next scan line (the zero position, or origin),
the indexing button is pressed once again, and the red LED turns off.
When the indexing button is released at the center of the next scan line, the position of
encoder 1 is reset to the
Origin
parameter value (equivalent to
Scan > Encoder >
Origin
). At the same time, the index value will be incremented by a predefined
distance set in the (encoder 2)
Resolution
parameter (see “Setting Up the Scan and
Index Parameters for an Elbow” on page 31).
To set the parameters for a symmetrical scan
1.
Set the appropriate scan type in the OmniScan MXU software by selecting
Scan >
Inspection > Type = Raster Scan
.
2.
In the OmniScan MXU software, set the scanner’s encoder number (1), type
(Quad), and resolution (12 steps/mm):
a)
Select
Scan > Encoder > Encoder = 1
.
b)
Select
Scan > Encoder > Type = Quad
.
c)
Select
Scan > Encoder > Resolution = 12
.
Scan axis
Index
axis
The initial position of the
scanner must be at the
center of each scan line.
Center line
(zero position)
on pipe
Summary of Contents for FlexoFORM
Page 6: ...Table of Contents vi 10 003591 01EN Q7780031 Rev 4 January 2020 ...
Page 8: ...10 003591 01EN Q7780031 Rev 4 January 2020 List of Abbreviations viii ...
Page 12: ...10 003591 01EN Q7780031 Rev 4 January 2020 Labels and Symbols 4 ...
Page 24: ...10 003591 01EN Q7780031 Rev 4 January 2020 Important Information Please Read Before Use 16 ...
Page 26: ...10 003591 01EN Q7780031 Rev 4 January 2020 Introduction 18 ...
Page 30: ...10 003591 01EN Q7780031 Rev 4 January 2020 Chapter 1 22 ...
Page 44: ...10 003591 01EN Q7780031 Rev 4 January 2020 Chapter 3 36 ...
Page 82: ...10 003591 01EN Q7780031 Rev 4 January 2020 Chapter 7 74 ...
Page 86: ...10 003591 01EN Q7780031 Rev 4 January 2020 Appendix B 78 ...
Page 90: ...10 003591 01EN Q7780031 Rev 4 January 2020 List of Tables 82 ...
Page 94: ...10 003591 01EN Q7780031 Rev 4 January 2020 Index 86 ...