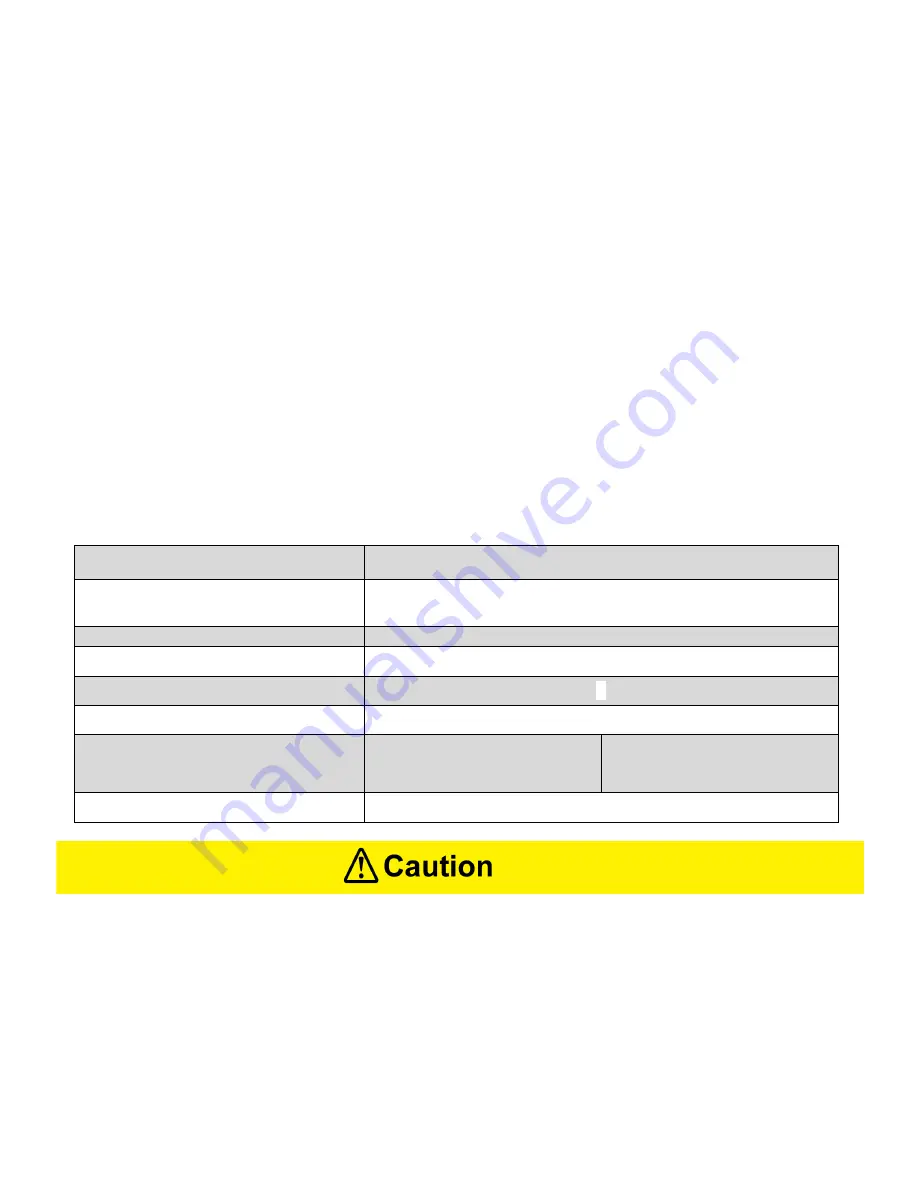
MCH60
Nuvair
Page 20
www.Nuvair.com
•
Oil Level Sight Gauge and Oil Pressure Gauge
•
Automatic Condensate Drains
•
Loadless Start
•
Low Oil Shutdown Switch
•
Final Stage Head
•
High Temp Switch set at 350°F
•
(4) CAN-35 Filtration Towers
o
(3) Dyer Filter Elements
o
(1) Triplex Filter Element
o
130,000 cu ft
•
Aluminum frame with isolation vibration mounts
Lubricant:
•
Nuvair 455
TM
Food Grade Lubricant (standard)
•
Nuvair 751
TM
Diester Based Lubricant (optional)
6.0 Compressor Specifications
Ambient room temperature should never exceed 113
°
F (45
°
C) during operation of the Compressor
System. Operation at higher temperatures may lead to system damage and malfunction.
6.1 Unpacking and Installation
•
Please read all information supplied before physically installing the Compressor System.
•
Unpack the system and remove from the pallet. Visually inspect the system to make sure there has
been no damage during shipping. If damaged, please call Nuvair to file a damage report. Please take
photos and supply detailed information about the damage.
Compressor Models
Two (2) Coltri MCH30
Charging Rate
Filling an 80 cu ft tank from 500 psi
20.4 SCFM (577 L/min)
×
2
Total Charging Rate: 40.8 SCFM (1154 L/min)
Maximum Operating Pressure
6000 psi (414 bar)
Pumping Unit RPM
1100
Number of Stages
4
×
2
Lubrication
Pressure Lubrication, capacity 1.2 gal (4.5 L)
×
2
Oil Pressure
cold
routine use
minimum pressure
58 psi (4 bar)
21.75 psi (1.5 bar)
14.5 psi (1 bar)
Air Quality
Grade E
Summary of Contents for MCH60
Page 1: ...Operation Manual MCH60...
Page 2: ...MCH60 Nuvair Page 1 www Nuvair com Notes...
Page 3: ...MCH60 Nuvair Page 2 www Nuvair com Notes...
Page 37: ...MCH60 Nuvair Page 36 www Nuvair com 19 0 Service Log Date Technician Name Service Performed...
Page 41: ...MCH60 Nuvair Page 40 www Nuvair com Notes...