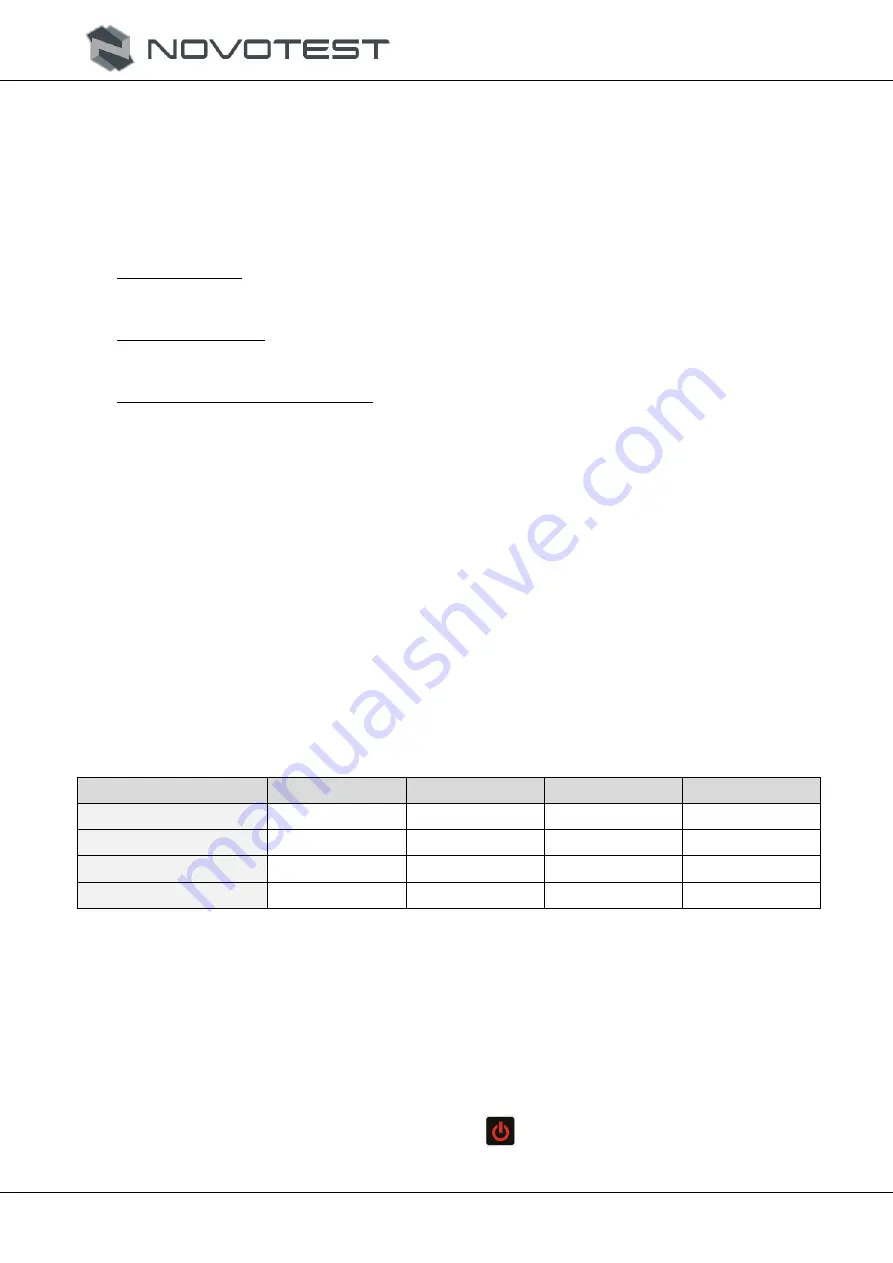
Operation Manual
Hardness Tester NOVOTEST T-UD3
Page. 16
deviation from these requirements. The additional error may be, either positive or negative, depending
on the specific conditions.
The reason for the additional error is the parasitic vibration at the indenter contact point with the
material at the moment of measurement. This is due to the vibration of the whole product, if its weight
is low, either because of product deflection if its thickness is small.
To determine the presence of additional error user should compare these measurement results with
the measurement results using a bench hardness tester.
There are three methods to delete the additional errors.
The first method – to make the one-point or two-point correction of the current user setting in
accordance with clause 2.3.7. It is used if an additional error is not more than 15%, and the results in a
series of measurements are constant.
The second method – deleting parasitic vibrations by gripping product in a vise (vise weight
should be over indicated in Table 1.3). To prevent damage of the product it is allowed to use the vise
with overhead jaws from a softer metal.
The third method (recommended) – deleting parasitic vibrations by grinding the object to a
massive polished plate. The plate should have roughness Ra not more than 0.4 microns, obviously
greater weight than indicated in Table 1.3, non-flatness not less than 0.005 mm, a Young's modulus of
the material from which the plate is made should be close to the Young's modulus of the product. The
underside of the product should be plane-polished with a roughness Ra not more than 0.4 microns and
flatness should be not more than 0,005 mm. For installation the product on the plate its support surface
(underside) should be covered with a thin layer of lubricant. Then the product is to be ground to the
plate surface in this way that between the surfaces and plates there are no even small air gaps.
Grinding must be tight enough so as the product and the plate are a single monolithic.
Also, imprints of different depths may be the reason of the additional error. Depths values may be
different, depending on the measured hardness (Table 2.1). It is recommended to measure the hardness
of the layer that is 20 times greater than the depth value. For the reasons mentioned above, the
measurement result is under the influence of the surface layer properties. The depth of indenter
penetration into the material is substantially smaller in comparison with the measurement by bench
machines: Brinell and Rockwell. This can cause the measurement result discrepancy in the case of
hardening, decarbonized layer, burn marks, and martensitic spots.
Table 2.1 - The depth of the imprints on the material surface in millimeters
Probe type
100НВ
187НВ
400НВ
60,7HRC
Leeb (D)
0,039
0,028
0,021
0,018
UCI (98 N)
0,098
0,081
0,052
0,036
UCI (50 N)
0,070
0,056
0,038
0,025
UCI (10 N)
0,031
0,025
0,017
0,011
Hardening can be formed in the surface layer after the turning, milling and rough polishing. The
softer is metal, the greater is difference between the hardness of the top layer and the inside layer.
Decarbonized layer with low hardness is formed by the high-temperature heat treatment. It may be
hardening, normalization, hot rolling, forging, etc. The thickness of this layer is typically less than 0.2
mm.
For heat treated steels with good hardenability when getting the average hardness due to surface
overheating martensitic spots with high hardness may occur.
2.3.2 Turning on
Turn on the device by long pressing the button
<
>
on the control panel until the short-time
splash screen on the display (Figure 2.3).