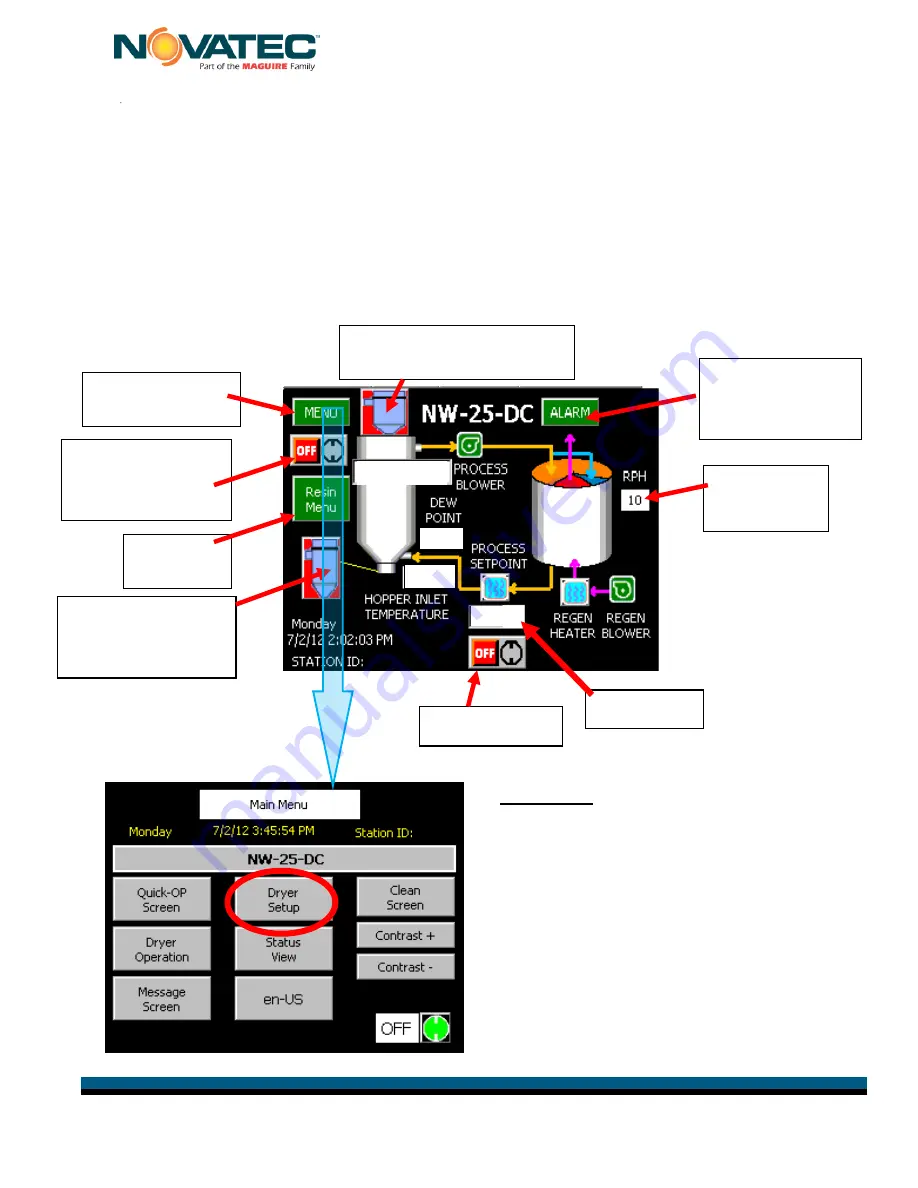
NWDC
IM 26 MAR 2014 © 2014 Novatec, Inc. All Rights Reserved
Page 25
[Type text]
[Type text]
NWDC IM 26 MAR 2014
Main Menu
:
From here you can access:
Quick-Op Screen
Dryer Setup
Dryer Operation
Status View
Message Screen (Alarms)
Clean Screen
Contrast Adjustments
En-US = English US
10 PROGRAMMING OTHER DRYING AND CONVEYING FUNCTIONS
10.1 Commonly Used Screens
STEP#1
– Depress MENU button to program the Drying and Conveying Functions.
The
Quick-Op
is the starting page for the dryer. Once the control is programmed it will
display an overview of drying and conveying operations.
Depress this button to
start the dryer.
This shows the
wheel speed
– it
should be between
6 and 12 rph.
Depress this button to go
to the alarm list
– there is
a tutorial there that
explains the alarms in
more detail.
Depress this button to go to
Machine Mount Receiver
page and start this receiver
–
the icon will turn green when
operating.
Depress this button to go
to the Main Menu for
Dryer Set Up & more.
Depress this
button to go to
the resin menu.
Depress this button to go to Hopper
Receiver page and start this receiver
–
the icon will turn green when operating.
Depress this button to
enable and disable the
process heater
– the icon
will turn green when
energized.
Polycarbonate
250 F°
249 F°
-40
Press to Change
Process Setpoint