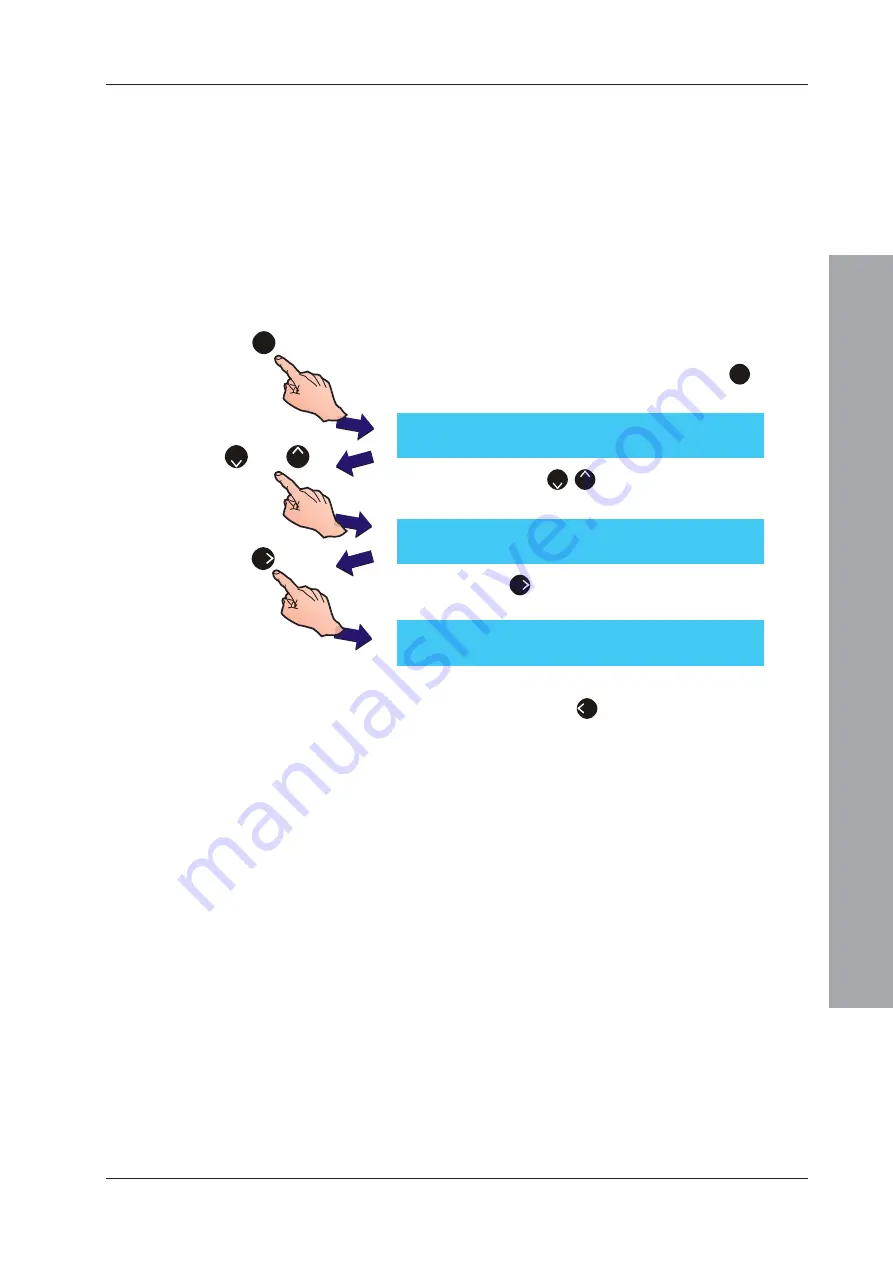
ID50 Series Panel - Installation, Commissioning & Configuration Manual
Configuration
Mode
47
997-263, Issue 4
September 2002
5.5.18 Digital Input 1
Digital Input 1 can be configured as either Day Mode Start
or Class Change function.
When configured as Day Mode Start, activation from the
input during the Day Mode period starts/ends Day Mode
delays, depending on their current state.
When Class Change is selected outputs assigned to CBE
Rules that have Class Change configured will activate
when Digital Input 1 is operated.
To configure Digital Input 1:
1
Using the numeric keypad, press
1
at the
Commissioning menu to enter the Setup menu.
2
Press either
2
/
8
to step through the options until
the Digital Input 1 menu is displayed.
3
Press
6
to toggle between Day Mode Start and
Class Change.
4
With the required configuration of Digital Input 1
displayed, press
4
to return to the Commissioning
menu.
[Setup] Language =
English
> : Change
×
: More
< : Exit
[Setup]
Digital Input 1 =
Day Mode Start
> : Change
×
: More
< : Exit
[Setup]
Digital Input 1 =
Class Change
> : Change
×
: More
< : Exit
1
or
8
2
6