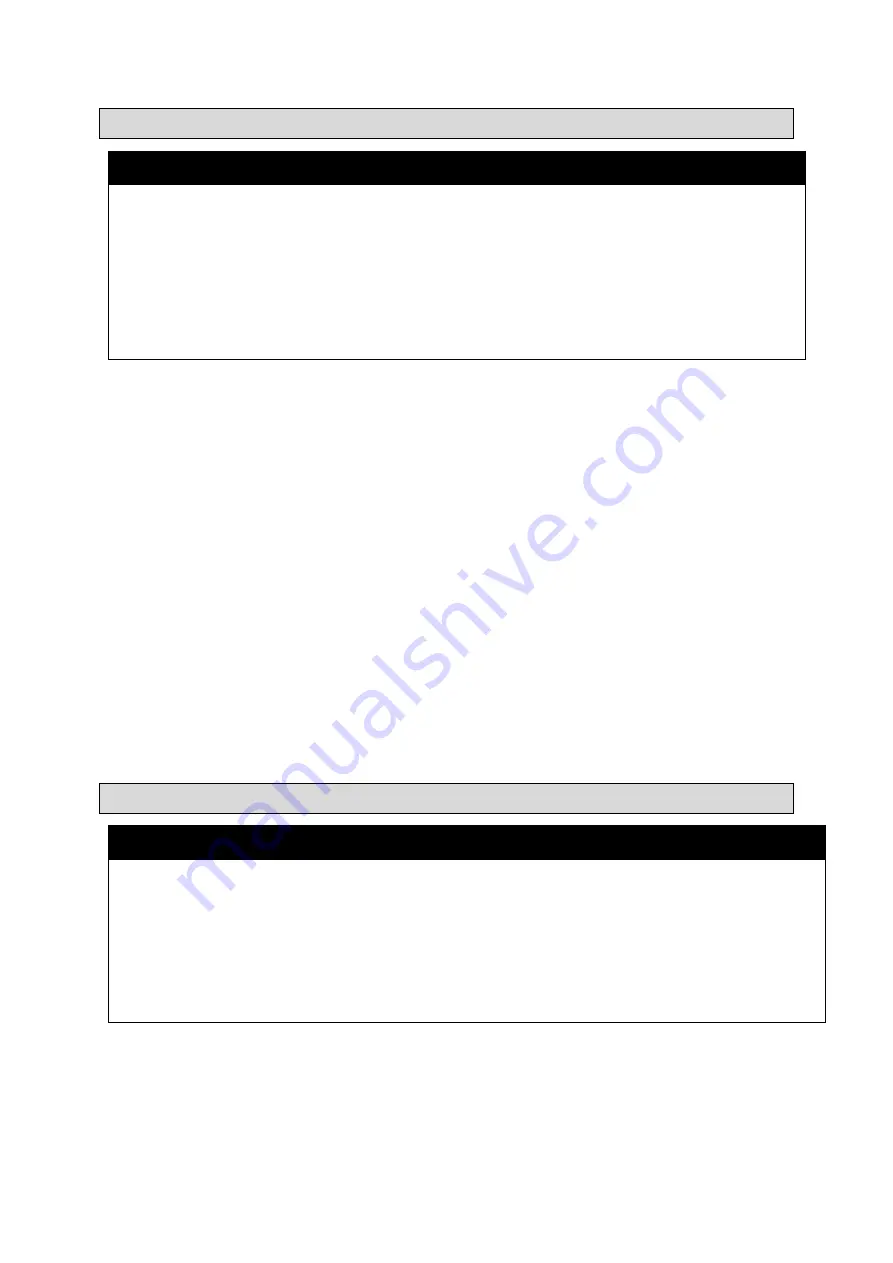
Page 11 of 23
Assembly Instructions
⚠
WARNING
•
The air compressor should be turned off, unplugged from the power source, the air bled from the
tank and the unit allowed time to cool before any maintenance is performed. Personal injuries
could occur from moving parts, electrical sources, compressed air or hot surfaces. The quick
connect assembly must be attached before use. Failure to assemble correctly could result in
leaks and possible injury.
•
If unsure of assembly instructions or you experience difficulty in the assembly please call your
local service department for further information.
1. Unpack the air compressor. Inspect the unit for damage. If the unit has been damaged in
transit, contact the carrier and complete a damage claim. Do this immediately because there
are time limitations to damage claims.
2.
Check the compressor’s serial label to ensure that you have received the model ordered, and
that it has the required pressure rating for its intended use.
3. Locate the compressor according to the following guidelines:
a. Position the compressor near a grounded electrical outlet.
b. The compressor must be at least 12 inches (31 cm) from any wall or obstruction, in a
clean, well-ventilated area, to ensure sufficient air flow and cooling.
c. In cold climates, store portable compressors in a heated building when not in use.
This will reduce problems with the motor starting and freezing from water
condensation.
d. Remove the compressor from the carton and place it on the floor or a hard, level
surface. The compressor must be level to ensure proper drainage of the moisture in
the tank.
Before Each Use
⚠
WARNING
•
Risk of unsafe operation.
Firmly grasp air hose in hand when installing or disconnecting to prevent
hose whip.
•
Risk of unsafe operation.
Do not use damaged or worn accessories.
•
Risk of bursting.
Too much air pressure causes a hazardous risk of bursting. Check the
manufacturer’s maximum pressure rating for air tools and accessories. The regulator outlet pressure
must never exceed the maximum pressure rating.
LOCATION OF THE AIR COMPRESSOR: The air compressor should always be located in a clean,
dry, and well-ventilated environment. The unit should have at minimum 12 inches of space on each
side. The air filter intake should be free of any debris or obstructions. Check the air filter on a daily
basis to make sure it is clean and in working order.