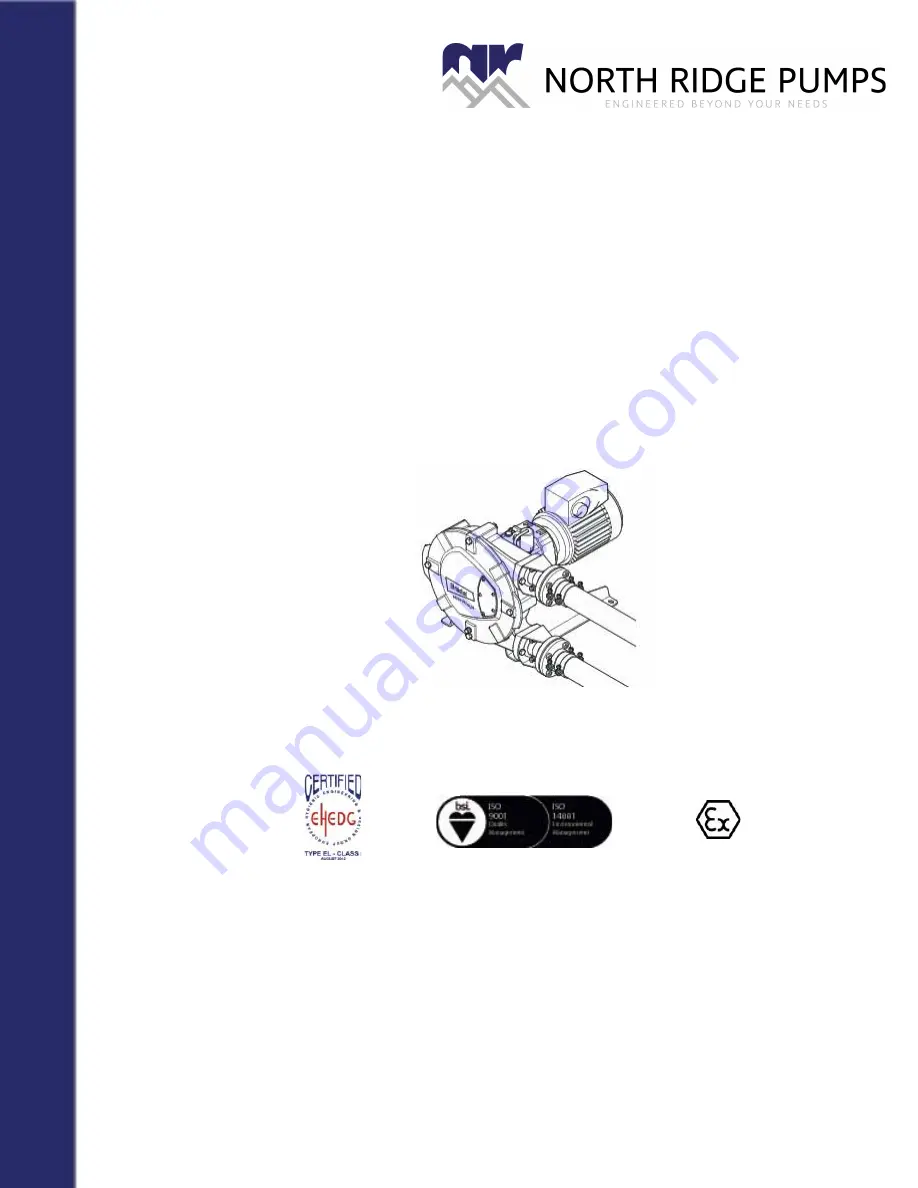
Product Specification Sheet
X-Cel House, Chrysalis Way, Langley Bridge, Eastwood, Nottinghamshire NG16 3RY
Tel: +44 (0) 1773 302 660 | Email: [email protected] | Website: www.northridgepumps.com
Hose pump series
Bredel 25 and Bredel 32
Manual
Product Specification Sheet
X-Cel House, Chrysalis Way, Langley Bridge, Eastwood, Nottinghamshire NG16 3RY
Tel: +44 (0) 1773 302 660 | Email: [email protected] | Website: www.northridgepumps.com
Hose pump series
Bredel 25 and Bredel 32
Manual