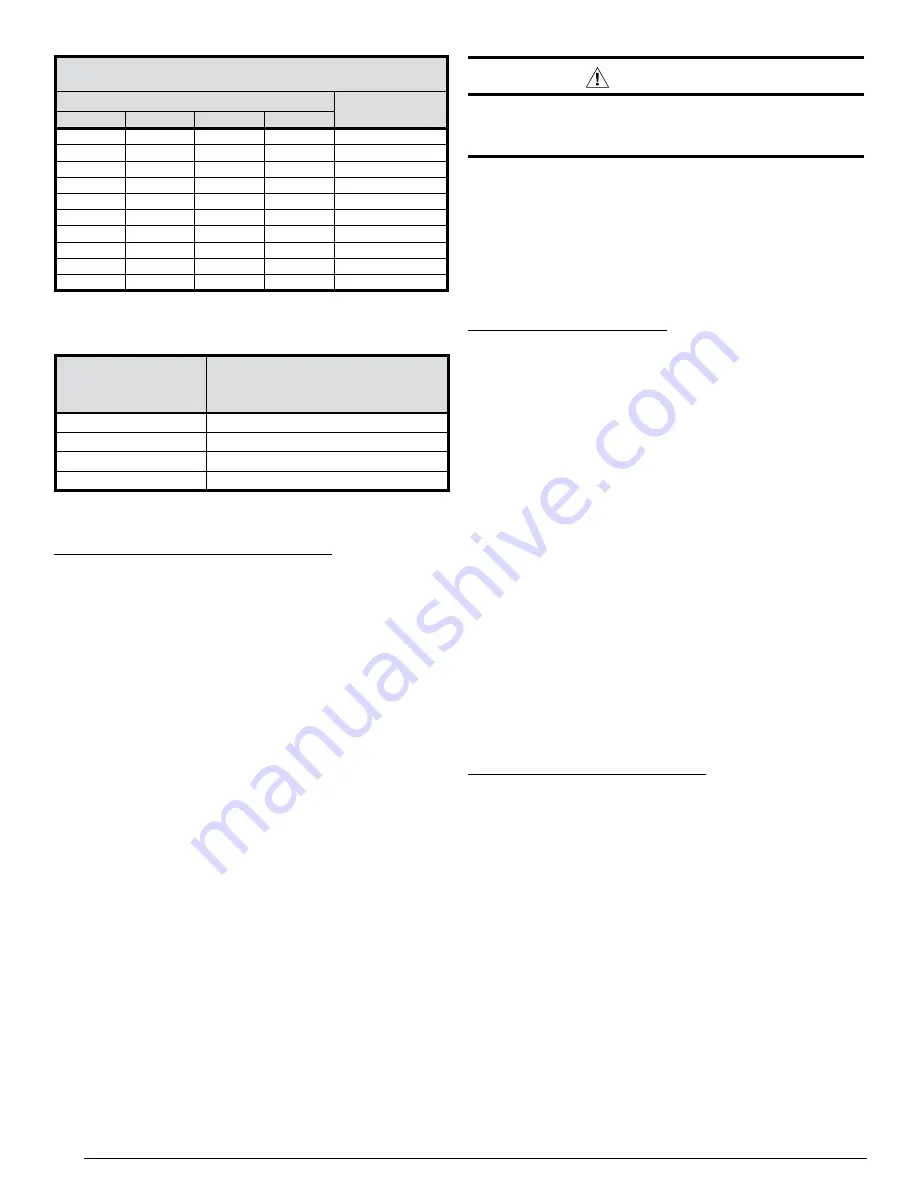
12
Table 3. Copper Wire Size
COPPER WIRE SIZE — AWG
(1% VOLTAGE DROP)
SUPPLY WIRE LENGTH-FEET
SUPPLY CIRCUIT
AMPACITY
200
150
100
50
6
8
10
14
15
4
6
8
12
20
4
6
8
10
25
4
4
6
10
30
3
4
6
8
35
3
4
6
8
40
2
3
4
6
45
2
3
4
6
50
2
3
4
6
55
1
2
3
4
60
NOTE:
Wire Size based on N.E.C. for 60° type copper conductors.
Table 4. Thermostat Wire Gauge
WIRE GAUGE
RECOMMENDED MAXIMUM
WIRE LENGTH (FT) FROM UNIT
TO THERMOSTAT
22
45
20
70
18
115
16
180
Checking Heat Anticipator Settings
• Add the current draw of the system components.
OR
• Measure the current flow on the thermostat
R
-
W
circuit
after the circulating blower motor has started. Set the heat
anticipator according to the thermostat manufacturer’s
instructions for heat anticipator settings.
Heating Configurations
This furnace is factory configured for two stage gas heating
operation with a two stage heating thermostat. Connect the low
voltage thermostat
White
&
Brown
wires to
W1
&
W2
, between
the unit low voltage terminal board and thermostat sub-base.
To operate with a single stage heat thermostat, only connect
the low voltage thermostat
White
wire between
W1
on the unit
low voltage terminal board and thermostat sub-base. Reposition
the automatic heat staging jumper located on the ignition control
module from NONE to 5 or 10 for the desired delay in minutes
before the gas furnace will automatically move to high heat
operation. See
NOTE:
When low fire on the gas valve is energized, the furnace
operates in low fire mode at a lower blower speed and the timer
begins its delay function. If the room thermostat is not satisfied
before the timer activates, the furnace will stage to high fire.
The inducer motor and blower will ramp to a higher speed until
the thermostat is satisfied.
Configuring the Variable Speed Blower
The variable speed blower has been designed to give the
installer maximum flexibility for optimizing system performance,
efficiency, and comfort. It is equipped with a microprocessor-
controlled variable speed motor that is pre-programmed to
deliver optimum airflow in a variety of conditions and system
configurations. Because the blower can be configured in many
ways, it is important to read and follow all instructions carefully.
CAUTION:
To avoid personal injury or property damage, make
certain that the motor leads cannot come into contact
with any uninsulated metal components of the unit.
Before operation, the variable speed blower must be configured
to match the unit with the system, climatic conditions, and
other system options. With the blower installed and configured
properly, the furnace will gradually change speed in response
to changes in system variables such as thermostat settings,
duct static, filters, etc. The variable speed blower is configured
by setting the heat, cool, and adjust jumpers located on the
ignition control board as described below. See
.
Selecting Cooling Airflow
The cooling airflow is selected by setting the Cool and Adjust
jumpers on the ignition control board.
lists the recommended airflow values (CFM) and selector
tap settings for each nominal system capacity. All airflows
for other modes of operation (except secondary gas heat)
are determined by this basic setting. For maximum capacity,
generally, a selection at or near the top of the CFM range for
that nominal capacity is best.
NOTES:
• The CFM values listed in
are not dependent on
duct static pressure. The motor automatically compensates
(within the limits of the motor) for changes in duct static
pressure.
• If coil icing occurs, the basic cooling airflow selected may
be too low. Verify the selected setting is within the range
shown in
and the system is properly charged. If
icing continues, raise the selected airflow to the next higher
tap.
• For maximum dehumidification and energy efficiency, select
an airflow near the middle or bottom of the CFM range for
that nominal capacity.
• The 2-stage cooling feature of the unit requires modulating
the airflow. The unit will automatically adjust the airflow to
the appropriate rate when the unit capacity changes.
Selecting Gas Heating Airflow
The heating airflow is selected by setting the heat jumper to
the desired tap (A,B,C, or D) located on the ignition control
board. Refer to
rise based on the furnace’s nominal efficiency and firing input.
Follow across the table row to find the tap setting and nominal
air-flow. Verify the selected rise is within the specification shown
on the furnace rating label.
Optional Humidistat
An optional humidistat may be installed in the return air duct
for humidity control (when needed), maximum system capacity
and energy efficiency. The humidistat senses when humidity in
the return air stream is above a preset level and sends a signal
to the motor to reduce airflow. This allows more moisture to be
removed until the humidity level drops.
NOTE:
The indoor blower
motor of this packaged unit is pre-programmed for humidistat
operation. Remove the
Red
jumper wire between the
R
and
DEHUM
terminals on the ignition control board.
If installing a humidistat, install it in the return air duct as
directed in the installation instructions included with the kit.