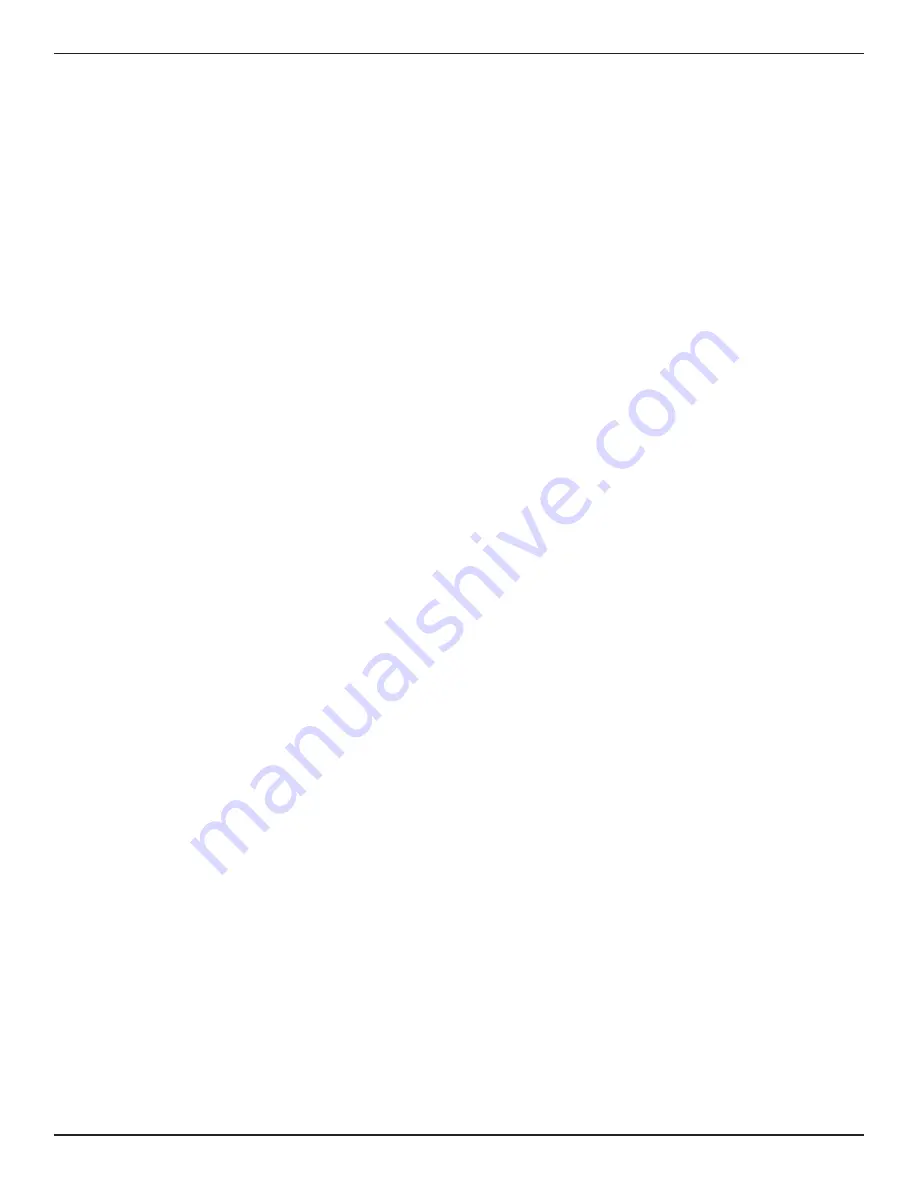
1-1
Safety
© 2022 Nordson Corporation
Section 1
Safety
Introduction
Read and follow these safety instructions. Task- and equipment-specific warnings,
cautions, and instructions are included in equipment documentation where appropriate.
Make sure all equipment documentation, including these instructions, is accessible to
persons operating or servicing equipment.
Qualified Personnel
Equipment owners are responsible for making sure that Nordson equipment is installed,
operated, and serviced by qualified personnel. Qualified personnel are those employees
or contractors who are trained to safely perform their assigned tasks. They are familiar
with all relevant safety rules and regulations and are physically capable of performing
their assigned tasks.
Intended Use
Use of Nordson equipment in ways other than those described in the documentation
supplied with the equipment may result in injury to persons or damage to property.
Some examples of unintended use of equipment include:
• using incompatible materials
•
making unauthorized modifications
• removing or bypassing safety guards or interlocks
• using incompatible or damaged parts
• using unapproved auxiliary equipment
• operating equipment in excess of maximum ratings
Regulations and Approvals
Make sure all equipment is rated and approved for the environment in which it is
used. Any approvals obtained for Nordson equipment will be voided if instructions for
installation, operation, and service are not followed.
All phases of equipment installation must comply with all federal, state, and local codes.
Summary of Contents for Encore HD iControl 2
Page 6: ...2022 Nordson Corporation 1609758 04 iv Table of Contents...
Page 8: ...2022 Nordson Corporation 1609758 04 ii Change Record...
Page 84: ...2022 Nordson Corporation 1609758 04 4 34 Troubleshooting...
Page 102: ...2022 Nordson Corporation 1609758 04 6 12 Parts...
Page 104: ...2022 Nordson Corporation 1609758 04 7 2 Drawings...
Page 105: ......
Page 106: ......
Page 107: ......
Page 108: ......
Page 109: ......
Page 110: ......
Page 113: ......
Page 114: ......