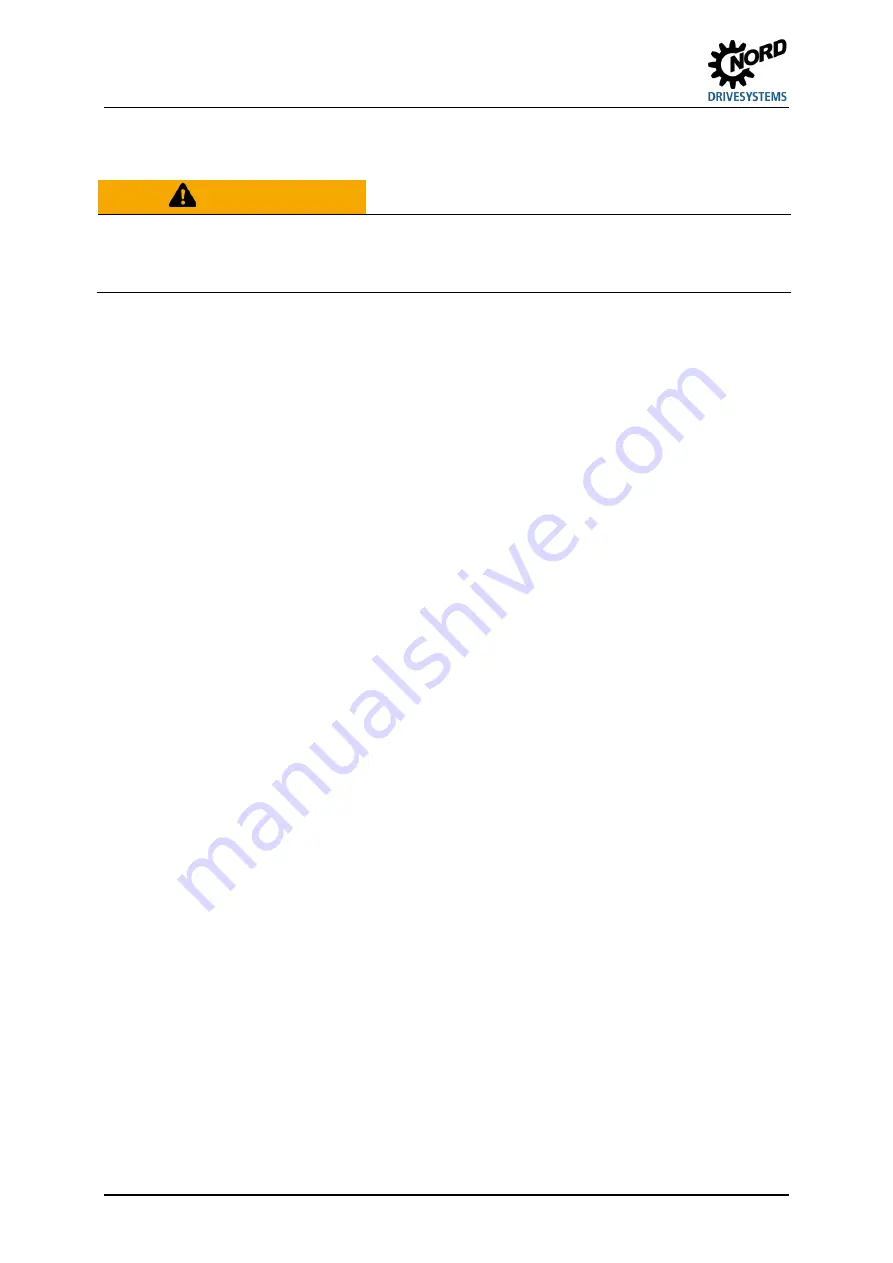
Industrial gear units – Operating and Assembly Instructions
74
B 1050 en-4419
5.2.8 Oil change
WARNING
Risk of burns and injuries
• Allow the gear unit to cool down.
• Wear protective gloves and goggles when changing the oil.
The position of the oil drain screw (optionally the drain tap), vents and devices for checking the oil
level can be obtained from the specific dimension sheet for the order.
Procedure:
1. Select a collection vessel according to the stated quantity of oil (please see chapter 7.3.3
"Lubricant quantities")and place it under the oil drain screw or the oil drain tap.
2. Unscrew the vent from the gear unit.
3. Unscrew the oil drain screw or the sealing plug from the oil drain tap and open it.
4. Completely drain the oil from the gear unit.
5. Clean the interior of the gear unit by flushing with oil so that oil sludge particles, due to wear and
old residues, are removed. The same type of oil as is used for operation must be used for this.
6. Clean the thread of the oil drain screw or the sealing cap of the oil drain tap and coat with a
threadlocker (e.g. Loctite 242 or Loxeal 54-03) before screwing in again. In both cases, tighten the
screws with the correct torque (please see chapter 7.4 "Screw tightening torques").
7. Fill the gear unit with the specified quantity of fresh oil according to the name plate through the vent
hole. If the gear unit is equipped with a dipstick, the oil may be filled through this hole.
8. After approx. 15 minutes (for oil level tanks 30 minutes), check the oil level as described in section
5.2.3 "Oil level"and correct as necessary.
9. Other attached components such as filters and piping should also be drained if necessary.
10. For gear units with oil circulation lubrication and oil supply systems, the oil bearing system must be
drained according to the manufacturer's specifications (maintenance instructions).
5.2.9 Internal cooling system (Option: CC)
To check the cooling coil, the coolant feed must be shut off and the pipes disconnected from the
cooling coil. If deposits are apparent on the inner wall of the cooling coil, the deposits and the coolant
must be analysed.
If a chemical cleaner is used, it must be ensured that the cleaning agent does not attack the material
of the cooling coil (copper pipe and brass fittings).
Check the cooling coil and the cover for leaks if strong corrosion is found on the connections.
Please contact the NORD Service department.
Summary of Contents for B 1050
Page 1: ...B 1050 en Industrial gear units Operating and Assembly Instructions...
Page 2: ...Industrial gear units Operating and Assembly Instructions 2 B 1050 en 4419...
Page 6: ...Industrial gear units Operating and Assembly Instructions 6 B 1050 en 4419...
Page 83: ...7 Appendix B 1050 en 4419 83 Gear units SK 5207 SK 10507 M1 oil screw holes...
Page 85: ...7 Appendix B 1050 en 4419 85 Gear units SK 5207 SK 10507 M3 oil screw holes...
Page 87: ...7 Appendix B 1050 en 4419 87 Gear units SK 5207 SK 10507 M5 oil screw holes...
Page 89: ...7 Appendix B 1050 en 4419 89 Gear units SK 11207 SK 15507 M1 oil screw holes...
Page 91: ...7 Appendix B 1050 en 4419 91 Gear units SK 11207 SK 15507 M3 oil screw holes...
Page 93: ...7 Appendix B 1050 en 4419 93 Gear units SK 11207 SK 15507 M5 oil screw holes...
Page 95: ...7 Appendix B 1050 en 4419 95 Gear units SK 5217 SK 11217 M1 oil screw holes...
Page 97: ...7 Appendix B 1050 en 4419 97 Gear units SK 5217 SK 11217 M5 oil screw holes...
Page 112: ...6052902 4419...