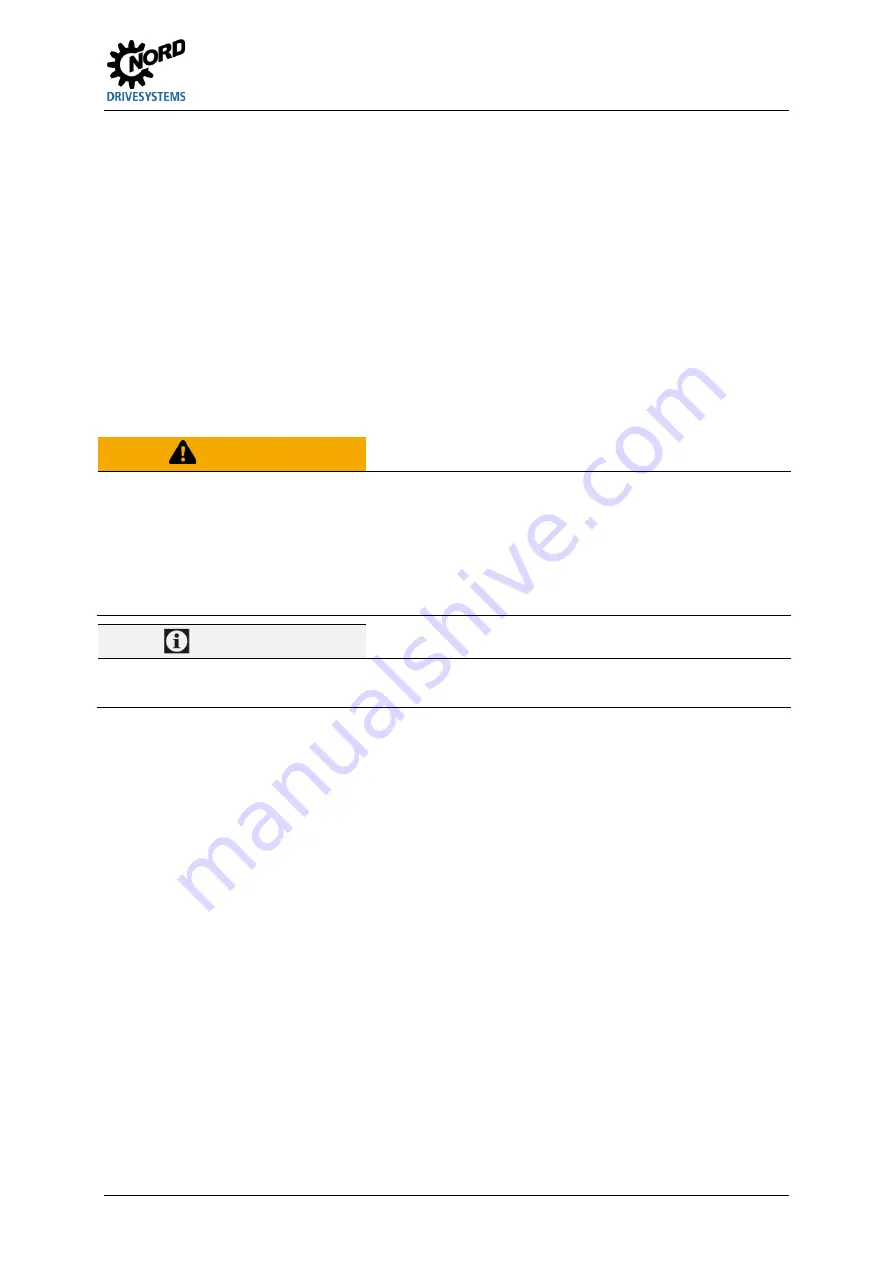
3 Transport, storage, assembly
B 1050 en-3921
47
NORD recommends a g6 fit for the bolt supporting the elastic element.
To facilitate installation and to protect against corrosion, a suitable lubricant may be applied to the
inner diameter of the elastic element.
The elastic element is made of an elastomer that can be used up to a temperature of +40°C.
Depending on the component, the elastic element is capable of compensating for a small assembly-
related offset. For specifications, refer to the manufacturer's documentation.
3.12 Motor mount (Option: MT)
Gear units with motor mounts and belt drives are pre-adjusted prior to delivery. Check the alignment of
the motor and the belt tension prior to commissioning the gear unit.
3.13 Installing the belt drive
WARNING
Risk of belt damage from incorrect installation
A damaged belt may break during operation. This can result in severe injuries.
• Reduce the axle spacing before installation so that the belt can be inserted into the grooves
without the use of force.
• Forcible mounting belts by means of tyre levers, screwdrivers etc. is completely impermissible, as
this often causes invisible damage to the stretch-resistant tension cord or the surrounding fabric.
Information
In the standard version, V-belt drives cannot be combined with a mounting flange or fan, as these
options would conflict with each other.
To ensure the correct function, the pre-tension of the belt must be checked and corrected as
necessary. Excessive, or too little contact pressure increases losses due to friction and may result in
an interruption of torque transfer.
The belt tension can be checked with the aid of various measuring devices. NORD recommends that
the check is made with the aid of a non-contact frequency measuring device, which enables quick,
simple and reliable testing even in inaccessible areas.
Initial installation and the general inspection procedure with a frequency measuring device are
described below:
1. Ensure the axis-parallel and horizontal alignment of the shaft and the V-belt pulleys. Maximum
angular deviation and displacement values can be provided on request.
2. Clean and de-grease all bare metal surfaces such as holes and the surface of the tapered bushing
of the pulley.
3. Insert the tapered bushing into the hub. Bring all connecting holes into alignment. Half-threaded
holes must be opposite half-smooth holes.
4. Lightly grease the studs or cap screws and screw them in. Do not tighten the screws yet.
5. Clean and de-grease the shaft.
6. Push the pulley with the taper bushing to the required position on the shaft.
7. If a key is used, place it in the groove on the shaft. There must be play between the key and the
groove in the hole.
Summary of Contents for 6052902/0213
Page 1: ...B 1050 en Industrial gear units Manual with installation instructions...
Page 2: ...Industrial gear units Manual with installation instructions 2 B 1050 en 3921...
Page 7: ...Publisher B 1050 en 3921 7...
Page 97: ...7 Appendix B 1050 en 3921 97 Gear units SK 5207 SK 10507 M1 oil screw holes...
Page 99: ...7 Appendix B 1050 en 3921 99 Gear units SK 5207 SK 10507 M3 oil screw holes...
Page 101: ...7 Appendix B 1050 en 3921 101 Gear units SK 5207 SK 10507 M5 oil screw holes...
Page 103: ...7 Appendix B 1050 en 3921 103 Gear units SK 11207 SK 15507 M1 oil screw holes...
Page 105: ...7 Appendix B 1050 en 3921 105 Gear units SK 11207 SK 15507 M3 oil screw holes...
Page 107: ...7 Appendix B 1050 en 3921 107 Gear units SK 11207 SK 15507 M5 oil screw holes...
Page 109: ...7 Appendix B 1050 en 3921 109 Gear units SK 5217 SK 11217 M1 oil screw holes...
Page 111: ...7 Appendix B 1050 en 3921 111 Gear units SK 5217 SK 11217 M5 oil screw holes...
Page 126: ...Industrial gear units Manual with installation instructions 126 B 1050 en 3921...
Page 127: ...Key word index B 1050 en 3921 127...
Page 128: ...6052902 3921...