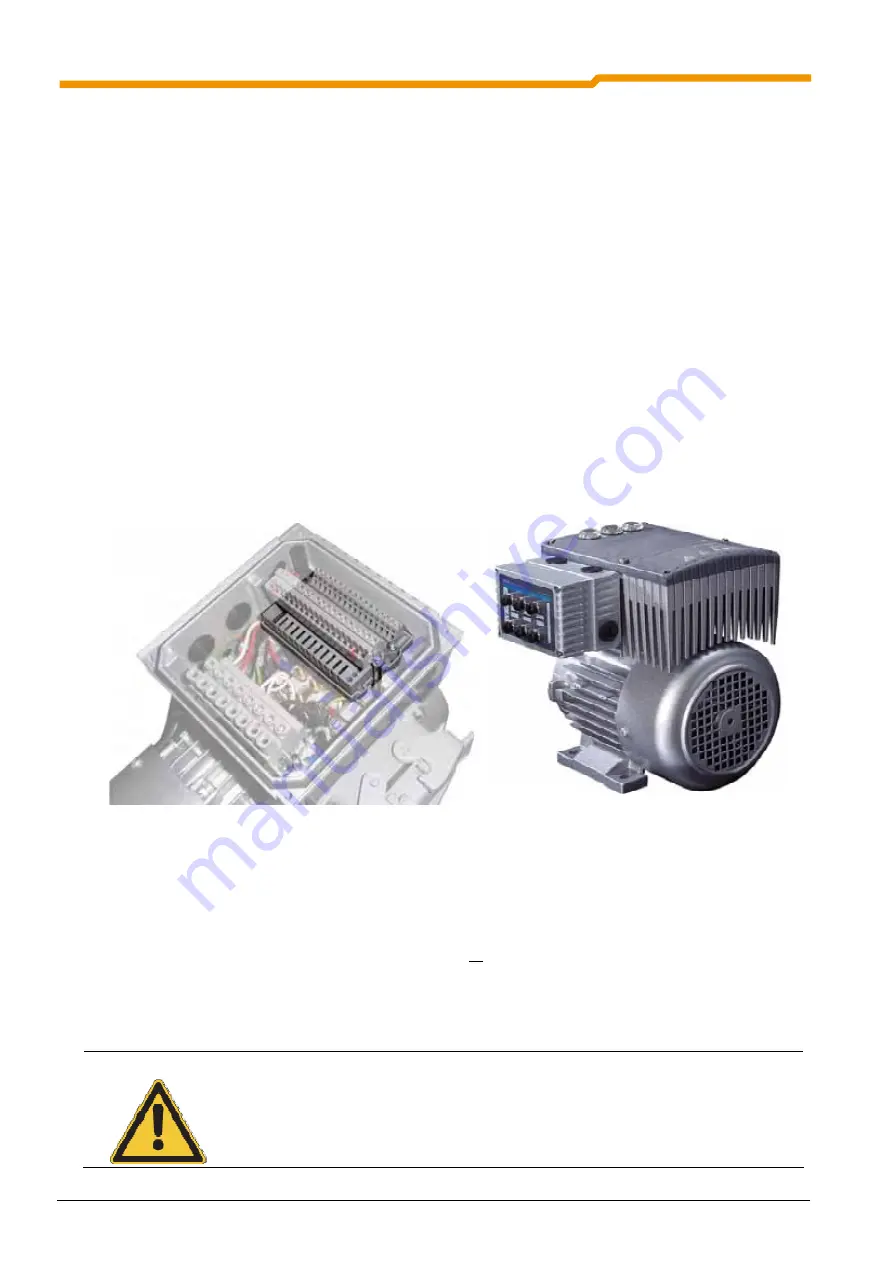
NORDAC SK 200E Manual
56
Subject to technical alterations BU
0200
GB
3 Options
A series of optional extension modules are available for the SK 200E. These modules are preferably used
for the production of the low voltage (24V control voltage) for the direct control or connection of the
frequency inverter to a host field bus.
The options are available both as an internal version for integration (into the FI), the so-called customer unit
SK CU4SK CU4-… or as an external version, the so-called technology unit SK TU4-… The differences
between the internal and external options are merely limited to the number of additional IOs and the
permissible current load of the connection terminals.
The
Customer Unit (SK CU4-…)
is integrated into the SK 200E. The electrical connection to the SK 200E
is made via the internal system bus. This is equipped with screw terminals for connection to external
peripherals. As an option, there is also the possibility of using 4/5-pin M12 plug connectors in the FI
housing.
A special case is the potentiometer adapter SK CU4-POT, which is mounted on the connection unit of the
frequency inverter and requires the use of an SK xU4-24V-…mains unit or an SK xU4-IOE IO module.
The
technology unit (Technology Unit, SK TU4-…)
is externally attached to the frequency inverter and is
therefore easy to access. The electrical connection to the SK 200E is made via the internal system bus.
External 4/5-pin plug connectors are available for use by the customer. A technology unit requires the use of
a suitable SK TI4-TU-… connection unit. The optional wall mounting kit SK TIE4-WMK-TU also allows the
technology units to be mounted close to the inverter.
SK TI4-... with integrated
SK CU4-...
SK 200E with external
SK TU4-...
An SK 200E frequency inverter is able to manage the following options via its system bus:
•
1 x CANopen absolute encoder and
•
1 x ParameterBox SK PAR-3H and (via an RJ12 connector)
•
1 x Field bus option (e.g. Profibus DP), internally or externally and
•
2 x I/O extensions (SK xU4-IOE-…), internally and / or externally
(FI firmware V1.2 R0 or higher, otherwise only 1x)
Up to 4 frequency inverters with their appropriate options can belong to a field bus.
WARNING
Modules must not be inserted or removed unless the device is free of voltage.
Summary of Contents for SK 200E Series
Page 1: ...GB BU 0200 NORDAC SK 200E Frequency inverter manual Quick commissioning page 123...
Page 2: ...NORDAC SK 200E Manual 2 BU 0200 GB...
Page 138: ...NORDAC SK 200E Manual 138 Subject to technical alterations BU 0200 GB 5 4 6 Certificate...
Page 262: ...NORDAC SK 200E Manual 262 BU 0200 GB...
Page 263: ...10 Keyword index BU 0200 GB 263...
Page 264: ...NORDAC SK 200E Manual 264 BU 0200 GB Part No 607 2002 1310...
Page 265: ...The Nordac SK 200E is available to order from www inverterdrive com...