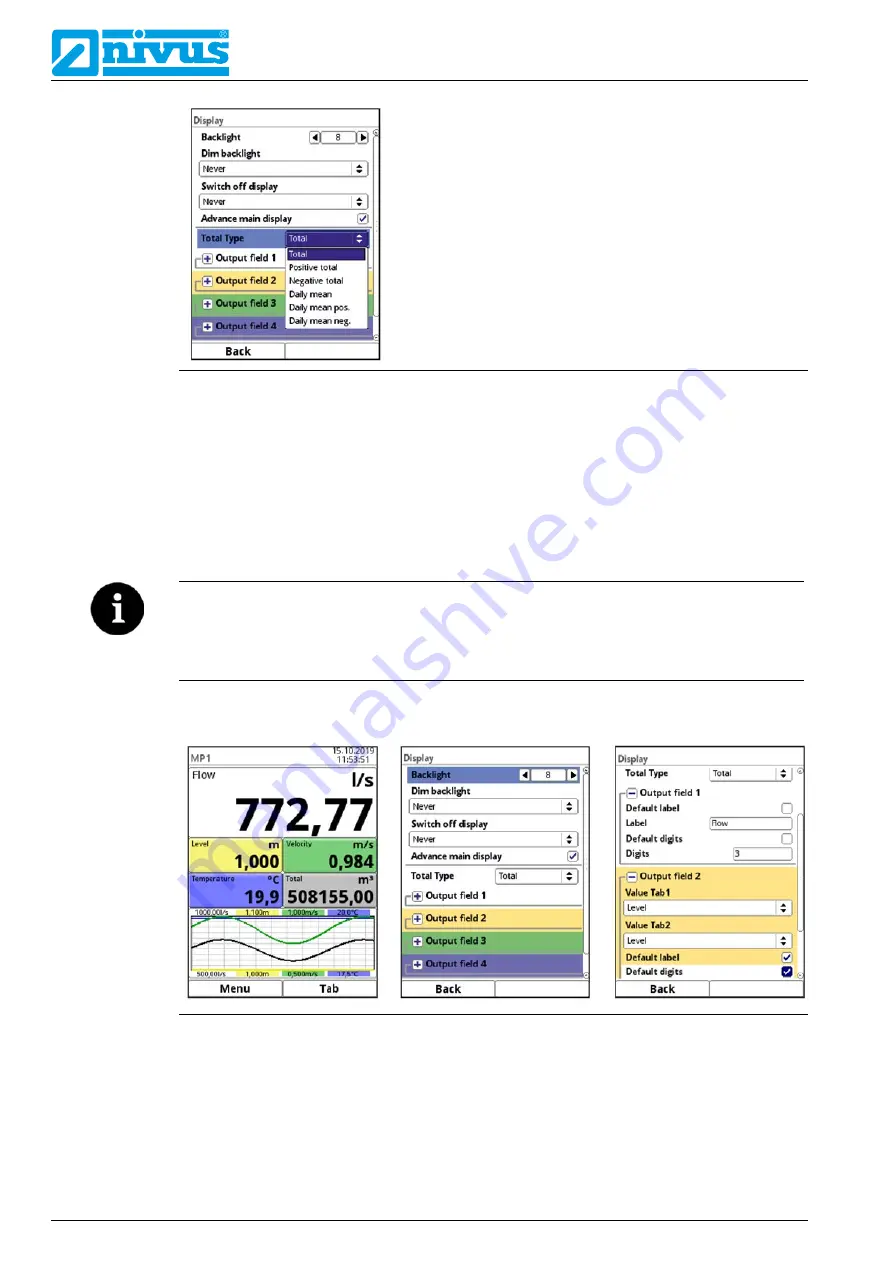
Instruction Manual
NivuFlow 650
page 130
NF 650 - rev. 01 / 29.06.2020
Fig. 36-2
Total Type
Total Type
The totals types to be displayed are defined here. The following options are available: >Total<,
>Positive total<, >Negative total<, >Daily mean<, >Daily mean pos.< and >Daily mean neg.<.
Output fields
The five main screen output fields (>Flow<, >Level<, >Velocity<, >Temperature< and >Total<
and/or flow for >Measurement place 1< and >Measurement place 2< and >Total< for measure-
ment place Combi) can be defined by the user in terms of names and decimal places.
Note
The values
assigned
to fields
cannot
be changed.
Example: the “Flow” field will
always
issue the flow value even if it has been renamed to
“Temperature”.
The underlying colours of the output fields correspond to the colours of the values in the main
display.
Fig. 36-3
Output fields, colours and settings
Â
Ü
Renaming
procedure:
1. Unfold the output field.
2. Untick >Standard Name<.
3. Enter a new name. Any name can be entered. The length of the name is limited to
16 characters.
The name entered
does not
change the values on the main screen.