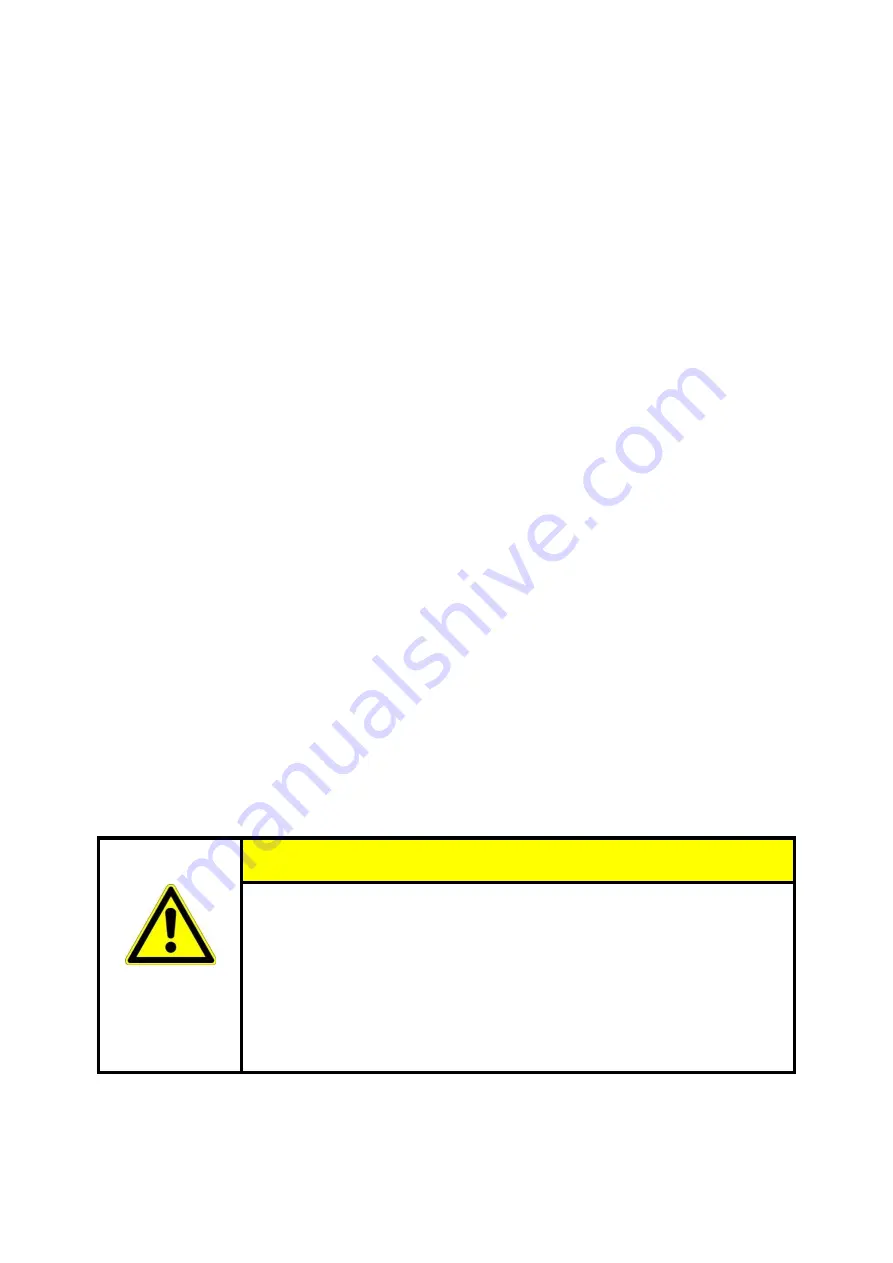
4.
Installation
4.0
General
The Booster unit must be installed and all electric connections must be performed in
accordance with local regulations.
4.1
Mounting
The Booster unit must be placed in a well ventilated room, in order to secure
adequate air supply for cooling of the pump engines. This also applies when the
motors are in operation.
The clearance in front of and on either side of the pumps must be at least 75cm.
4.2
Pipe Work
When installing the piping take care to avoid air traps.
CAUTION
Before the booster unit is connected to the water supply, the supply
line should be rinsed through carefully in order to remove coarse
impurities and metal shavings.
The pipes are connected to the manifolds of the Booster set. Either
end can be used.
The set must be tightened up before start-up.