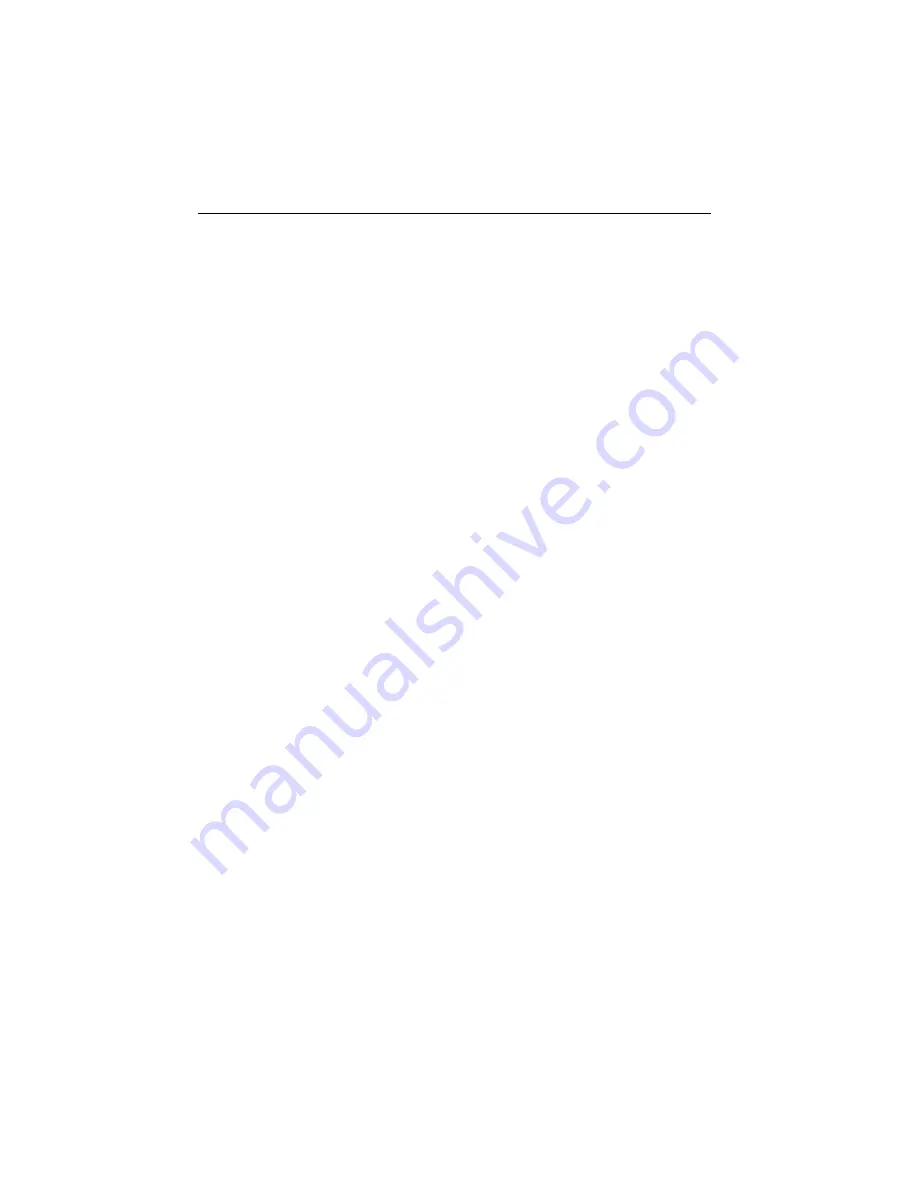
2
|
ni.com
|
NI SMD-7611/7612 User Manual
Safety Information
Only qualified personnel are permitted to transport, assemble, commission, and maintain this
equipment. Properly qualified personnel are persons who are familiar with the transport,
assembly, installation, commissioning and operation of motors, and who have the appropriate
qualifications for their jobs. The qualified personnel must know and observe the following
standards and regulations:
•
IEC 364 resp. CENELEC HD 384 or DIN VDE 0100
•
IEC report 664 or DIN VDE 0110
•
National regulations for safety and accident prevention or VBG 4
To minimize the risk of potential safety problems, you should follow all applicable local and
national codes that regulate the installation and operation of your equipment. These codes vary
from area to area and it is your responsibility to determine which codes should be followed, and
to verify that the equipment, installation, and operation are in compliance with the latest revision
of these codes.
Equipment damage or serious injury to personnel can result from the failure to follow all
applicable codes and standards. We do not guarantee the products described in this publication
are suitable for your particular application, nor do we assume any responsibility for your product
design, installation, or operation.
•
Read all available documentation before assembly and commissioning. Incorrect handling
of products in this manual can result in injury and damage to persons and machinery.
Strictly adhere to the technical information on the installation requirements.
•
It is vital to ensure that all system components are connected to earth ground. Electrical
safety is impossible without a low-resistance earth connection.
•
The STR2 contains electrostatically sensitive components that can be damaged by incorrect
handling. Discharge yourself before touching the product. Avoid contact with high
insulating materials (artificial fabrics, plastic film, etc.). Place the product on a conductive
surface.
•
During operation keep all covers and cabinet doors shut. Otherwise, there are deadly
hazards that could possibility cause severe damage to health or the product.
•
In operation, depending on the degree of enclosure protection, the product can have bare
components that are live or have hot surfaces. Control and power cables can carry a high
voltage even when the motor is not rotating.
•
Never pull out or plug in the product while the system is live. There is a danger of electric
arcing and danger to persons and contacts.
•
After powering down the product, wait at least ten minutes before touching live sections of
the equipment or undoing connections (e.g., contacts, screwed connections). Capacitors
can store dangerous voltages for long periods of time after power has been switched off. To
be safe, measure the contact points with a meter before touching.
Be alert to the potential for personal injury. Follow the recommended precautions and safe
operating practices. Safety notices in this manual provide important information. Read and be
familiar with these instructions before attempting installation, operation, or maintenance. The