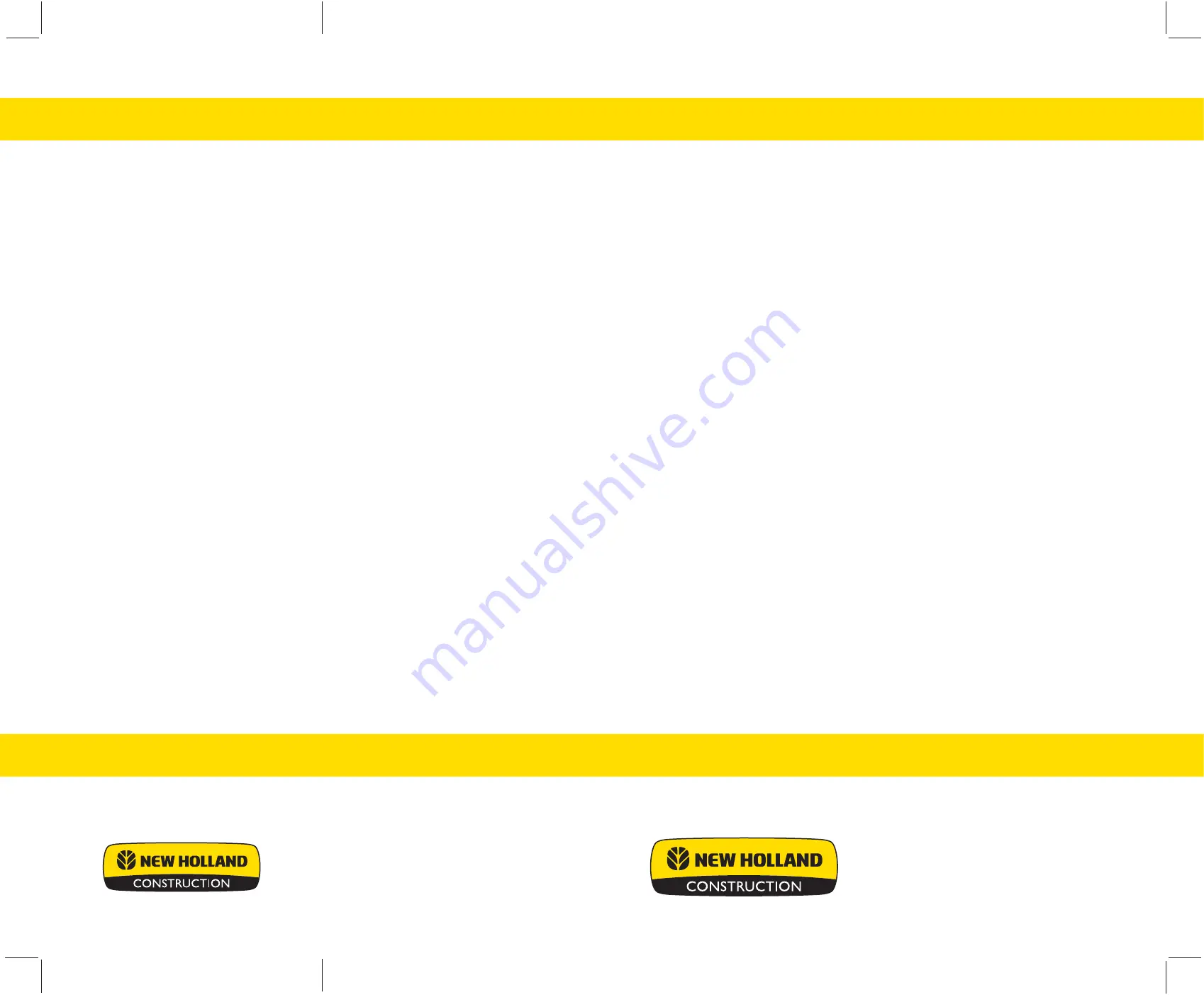
© 2015 CNH Industrial America LLC. All Rights Reserved.
SERVICE MANUAL
D180C
Tier 2
Crawler Dozer
PIN NDDC18000 and above; PIN NEDC18000 and above; PIN NFDC18000 and above
Part number 47907879
2
nd
edition English
October 2015
Replaces part number 47645622
SERVICE
MANUAL
D180C
Tier 2
Crawler Dozer
PIN NDDC18000 and above;
PIN NEDC18000 and above;
PIN NFDC18000 and above
1/2
Part number 47907879