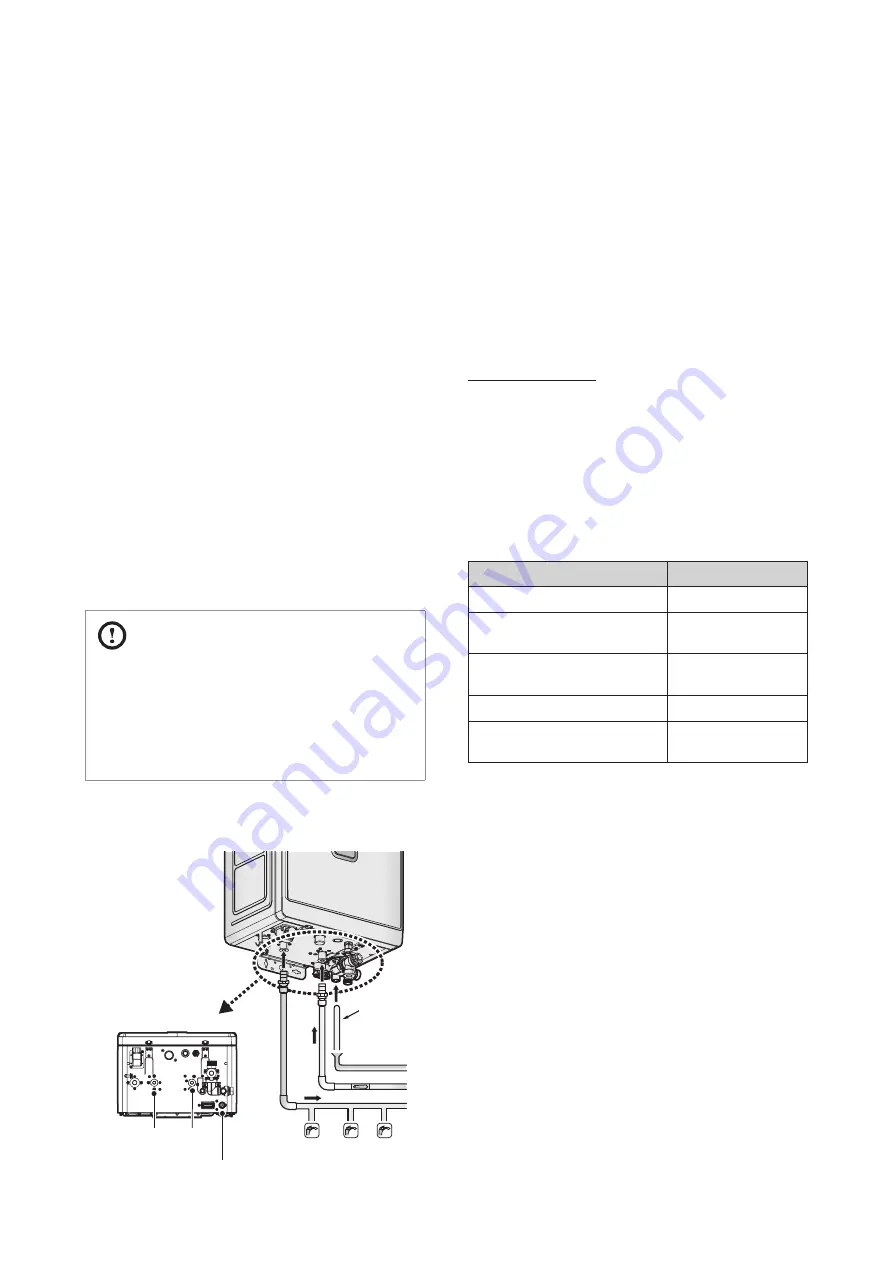
24 Installing the System Piping
4.2 Installing a Domestic Hot Water
(DHW) System
The water mains installation must comply with the Water Supply
(Water Fittings) Regulations and Scottish Water Byelaws.
The NCB300 is fitted with a stainless steel plate heat exchanger
for producing domestic hot water. The boiler does not have a
hot water store and in case of a demand for hot water the boiler
will heat the domestic water flowing through the plate heat
exchanger up to 65°C (adjustable) instantaneous.
In regions with a water hardness value higher than 200 ppm
(2.67 mmol/l), calcium deposits should be removed from the
plate heat exchanger on a regular basis. If problems occur
when using sanitary water with a chlorine content higher than
150 mg/l, no recourse can be made to the terms of the warranty.
In order to prevent calcification Navien recommends applying a
water softener.
The hardness of the water is variable in the United Kingdom
and other countries. The water company can provide exact
information about this. The domestic water installation can
be connected to the boiler by means of 15 mm compression
fittings.
If the mains supply is fitted with water meter, check valves or
loose jumper stop cock, then a DHW expansion device must be
fitted.
CAUTION
●
The installation must be made by sufficiently qualified
technicians, authorised to do so.
●
For correct installation, connect the central heating
system according to the current regulations together
with all other national and/or local regulations applicable
at the time of installation.
Refer to the following illustration for a typical DHW piping
example for the boiler.
Cold Water Supply
Condensate Pipe
Hot Water Supply
Bottom View
DHW Outlet
Adapter
Condensate
Outlet
Water Inlet
Adapter
Condensate
Drain Hose
When installing the DHW system, follow these guidelines:
●
Use only pipes, fittings, valves, and other components (such as
solder), that are approved for use in potable water systems.
●
Tighten the connection valves with care to avoid damage.
●
Keep the hot water piping system as short as possible, to
deliver hot water to the fixtures more quickly.
●
After installing the boiler, clean the cold water inlet filter. Then,
test the boiler for proper DHW supply and inspect for leaks.
●
If the mains supply is fitted with water meter, check valves or
loose jumper stop cock, then a DHW expansion device must
be fitted.
About the DHW Quality
Proper maintenance of the boiler is required when water quality
does not meet European standards. Damage caused by poor
water quality is not covered under warranty. The following table
shows the maximum contaminant levels allowed, based on the
European drinking water guideline: 98/83/EG dated 3 November
1998. If you suspect that your water is contaminated in any
way, discontinue use of the DHW and contact an authorised
technician or licensed professional.
DHW Quality
Parameter
Value
Water type
Potable water
pH
Conductivity (at 20°C in μS/cm)
7.0-9.5
Max. 2500
Chloride (ppm)
Iron (ppm)
Max. 150
Max. 0.2
Hardness (°dH / ppm)
1-12 °dH / 17-224 ppm
Number of bacterial colonies at
22°C (number/ml). pr EN ISO 6222
Max. 100
Navien is not responsible for performance issues of the domestic
system by scaling or accumulation of dirt; suitable steps shall be
taken by the installer and user to avoid water quality related issues.
Connection of the drinking water installation should be done
according to the Water Supply (Water Fittings) Regulations and
Scottish Water Byelaws.
Summary of Contents for NCB300-28K
Page 81: ...Memo...
Page 82: ...Memo...