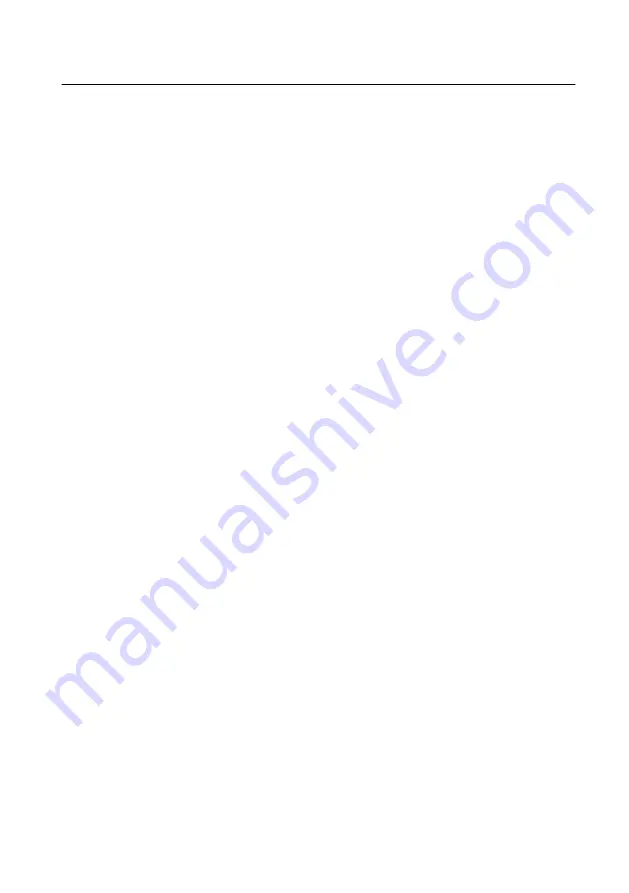
Test Conditions
Follow the setup and environmental information below to ensure the PXIe-4135 meets the
published specifications. Test limits in this document are based on the July 2016 edition of the
PXIe-4135 Specifications
.
•
Ensure that the safety interlock terminal is open during verification procedures unless
specifically required. Ensure proper operator safety procedures when using the
PXIe-4135 with the interlock closed.
•
Keep cabling as short as possible. Long cables act as antennas, picking up extra noise that
can affect measurements.
•
Verify that all connections to the PXIe-4135, including front panel connections and
screws, are secure.
•
Ensure that the PXI chassis fan speed is set to HIGH, that the fan filters, if present, are
clean, and that the empty slots contain filler panels. For more information about cooling,
refer to the
Maintain Forced-Air Cooling Note to Users
document available at
.
•
Allow a warm-up time of at least 30 minutes after the chassis is powered on and
NI-DCPower is loaded and recognizes the PXIe-4135. The warm-up time ensures that the
PXIe-4135 and test instrumentation are at a stable operating temperature.
•
Use low noise triax cabling for all HI and HI Sense connections. For LO and LO Sense
connections, use shielded twisted pair copper wire for all cable connections to the device.
•
To ensure the system has had adequate time to settle, wait one second after requesting a
new current or voltage or after changing a load before taking a measurement.
•
When making measurements, configure the following aperture time-related settings:
–
Set the
niDCPower Aperture Time
property or
NIDCPOWER_ATTR_APERTURE_TIME
attribute to 2 power-line cycles (PLCs) on
the module.
–
Set the
niDCPower Aperture Time Units
property or
NIDCPOWER_ATTR_APERTURE_TIME_UNITS
to power line cycles.
–
Set the
niDCPower Configure Power Line Frequency
property or the
NIDCPOWER_ATTR_POWER_LINE_FREQUENCY
attribute to either 50 or 60
depending on the frequency of the AC power line in your location.
•
Do not use the NI-DCPower Soft Front Panel (SFP) to request test points for any
adjustment functions because you cannot set aperture time using the SFP.
•
Ensure that properties or attributes for the module that are not specified in calibration
procedures are set to their default values.
•
When making measurements, configure any specified digital multimeters (DMMs) with
the best available ranges and measurement settings for each specified test point.
•
Keep relative humidity between 10% and 70%, noncondensing.
4
|
ni.com
|
PXIe-4135 Calibration Procedure