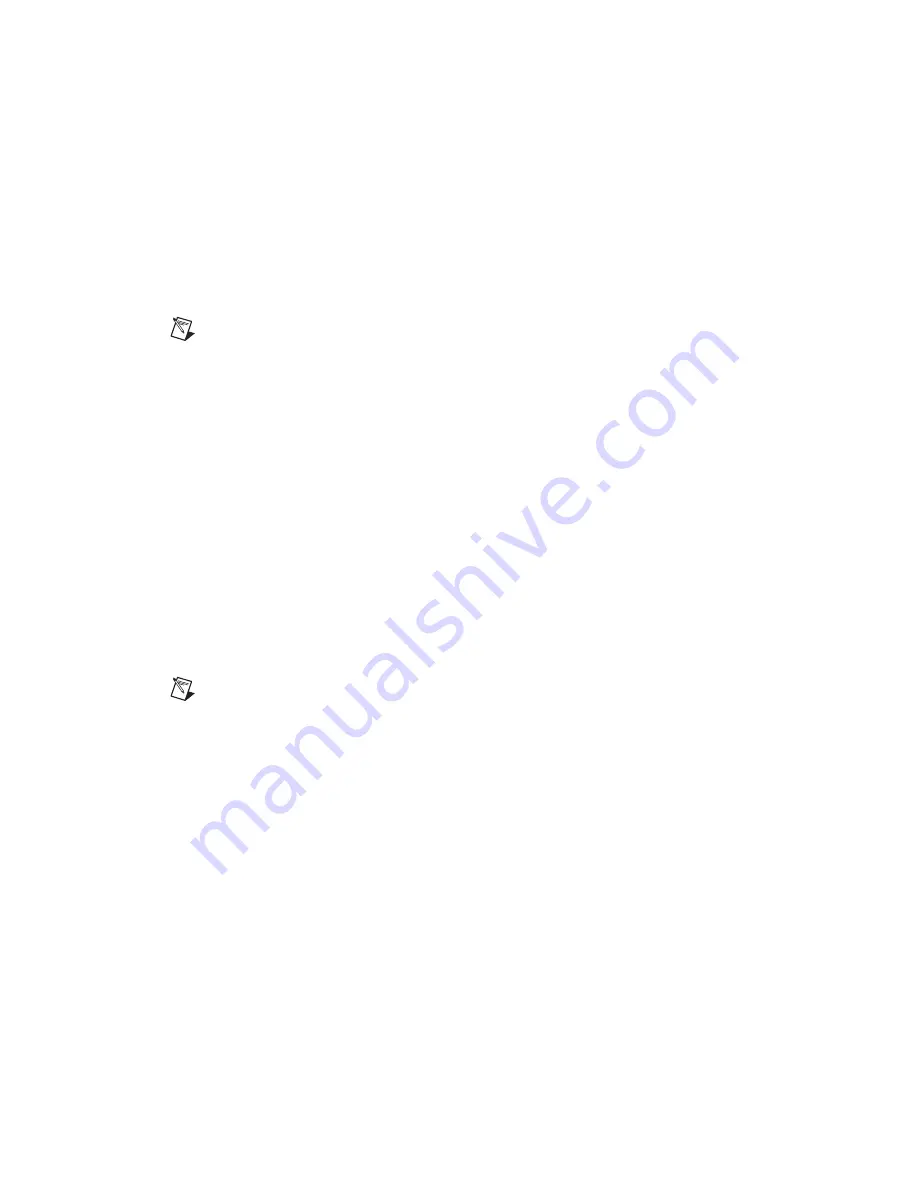
Chapter 4
Functional Overview
©
National Instruments Corporation
4-7
In its default configuration, the 7344 controller comes preconfigured as
four servo axes with Encoder 1 and DAC 1 mapped to Axis 1, Encoder 2
and DAC 2 mapped to Axis 2, and so on through Axis 4. However, it is
simple for advanced users to map any feedback and output resource to any
axis. This flexibility allows you to tailor each axis to accommodate your
specific motion system requirements.
Note
For many servo applications, the factory-default mapping of encoders and DACs to
axes will meet your system requirements.
Available feedback resources are Encoder <1..4> and ADC <1..4>.
Available output resources are DAC <1..4> and Stepper <1..4>.
Axes use the dedicated motion I/O signal lines assigned to them. A forward
and reverse limit input, a home input, and an inhibit output are dedicated to
each axis. Since there are four identical sets of these motion I/O signals,
mapping is not required. If the motion I/O is not needed by the axis, you
can reuse the signals as general-purpose I/O by disabling their indicated
function.
The 7344 controller supports axes with optional secondary feedback
resources (encoders or ADCs) and/or secondary output resources (DACs or
stepper outputs). Two feedback resources are used when implementing
dual-loop control. Defining two output resources is useful when controlling
axes with multiple motors, such as gantry systems where two DAC outputs
can be configured with different torque limits and/or offsets.
Note
Refer to the Axis and Resource Configuration section of the FlexMotion Software
Reference Manual for more information on configuring axes.
Motion Resources
Encoder, DAC, and ADC resources that are not used by an axis are
available for non-axis or nonmotion-specific applications. You can directly
control an unmapped DAC as a general-purpose analog output (±10 V).
Similarly, you can use any ADC channel to measure potentiometers or
other analog sensors.
If an encoder resource is not needed for axis control, you can use it for any
number of other functions, including position or velocity monitoring, as a
digital potentiometer encoder input, or as a master encoder input for
master/slave (electronic gearing) applications.