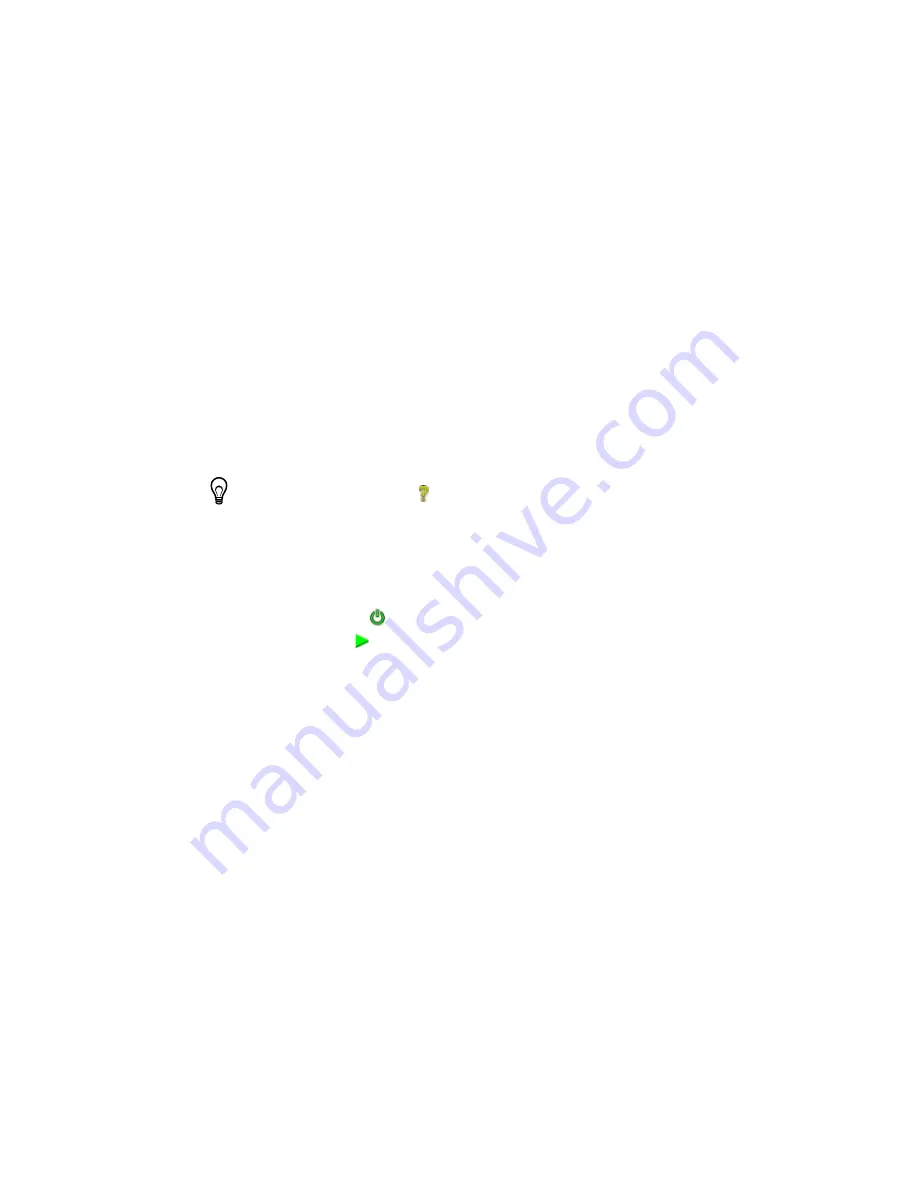
34
|
ni.com
|
Getting Started with NI 9512 and P7000 Drives
Step 7: Ena
b
le and Test the Drive using La
b
VIEW
Use the Interactive Test Panel to test and debug your motion system and configuration settings
on the selected axis. With the Interactive Test Panel you can perform a simple straight-line move
and monitor move and I/O status information, change move constraints, get information about
errors and faults in the system, and view position or velocity plots of the move. If you have a
feedback device connected to your system, you can also obtain feedback position and position
error information.
Complete the following steps to test your setup after configuring your axes using the
Axis
Configuration
dialog box. This test will move the motor 5 revolutions at 60 rpm.
1.
Use the DIP switches on the P7000 drive to set the desired drive step resolution. This
example uses 5000 steps/rev microstepping resolution. Table 6 shows the step resolution
switch settings.
2.
Right-click the axis in the
Project Explorer
window and select
Interactive Test Panel
from the shortcut menu. Opening this dialog box sends the axis settings to the hardware and
activates the I/O on the module.
Tip
Click the
Help
button (
) on the bottom of the dialog box for detailed
information about the items available in this dialog box.
3.
On the
Move
tab set
Target Position
to 25,000 Unit (5000 step resolution
×
5 revolutions).
4.
Click the
Move Constraints
tab. Set
Velocity
to 5000 Unit/sec (velocity = step resolution),
Acceleration/Deceleration
to 50,000 Unit/sec
2
, and
Acceleration Jerk/Deceleration
Jerk
to 500,000 Unit/sec
3
.
5.
Click the
Enable
button (
) on the bottom of the dialog box to enable the drive.
6.
Click the
Start
button (
) on the bottom of the dialog box to start the move with the
configured options.
7.
Use the
Status
and
Plots
tabs to monitor the move while it is in progress.
8.
Finalize your motion system setup by connecting and configuring additional I/O such as
limits as required by your system.