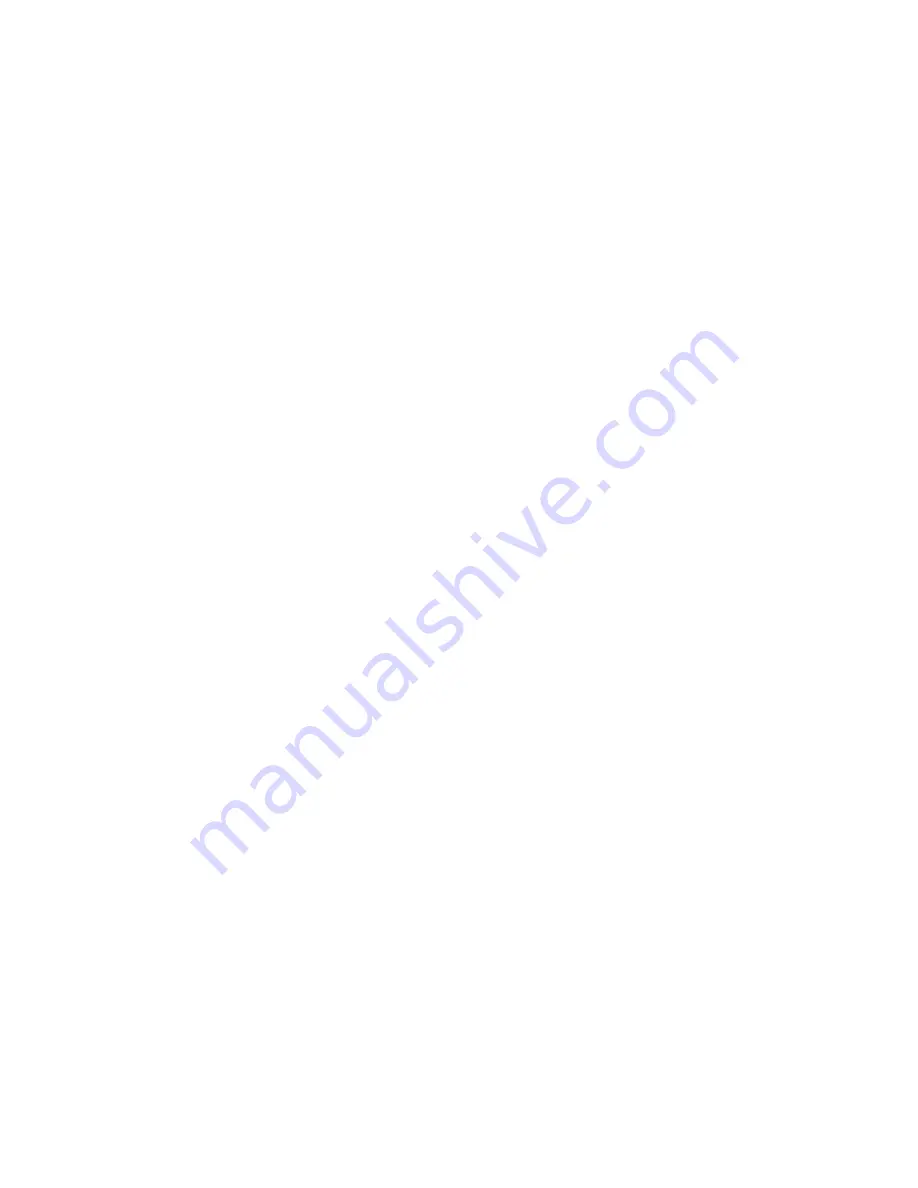
Chapter 4
Functional Overview
4-2
ni.com
Embedded Real-Time Operating System (RTOS)
The embedded firmware is based on an embedded RTOS kernel and
provides optimum system performance in varying motion applications.
Motion tasks are prioritized. Task execution order depends on the priority
of each task, the state of the entire motion system, I/O or other system
events, and the real-time clock.
The DSP chip is a separate processor that operates independently from
the CPU but is closely synchronized. The 7340 is a true multiprocessing
and multitasking embedded controller.
The advanced architecture of the 7340 enables advanced motion features,
such as enhanced PID functions. Refer to the
NI-Motion User Manual
for
more information about the features available on the 7340.
Trajectory Generators
The 7340 trajectory generators calculate the instantaneous position
command that controls acceleration and velocity while it moves the axis to
its target position. Depending on how you configure the axis, this command
is then sent to the PID servo loop or stepper pulse generator.
To implement infinite trajectory control, the 7340 has eight trajectory
generators implemented in the DSP chip (two per axis). Each generator
calculates an instantaneous position for each PID update period. While
simple point-to-point moves require only one trajectory generator,
two simultaneous generators are required for blended moves and infinite
trajectory control processing.
Analog Feedback
The 7340 has an 8-channel multiplexed, 12-bit ADC. The converted analog
values are broadcast to both the DSP and CPU through a dedicated internal
high-speed serial bus. The multiplexer provides the high sampling rates
required for feedback loop closure, joystick inputs, or monitoring analog
sensors. Refer to Appendix A,
, for the multiplexer scan rate.
Four of these channels are intended for calibration, leaving the other four
available for analog feedback.