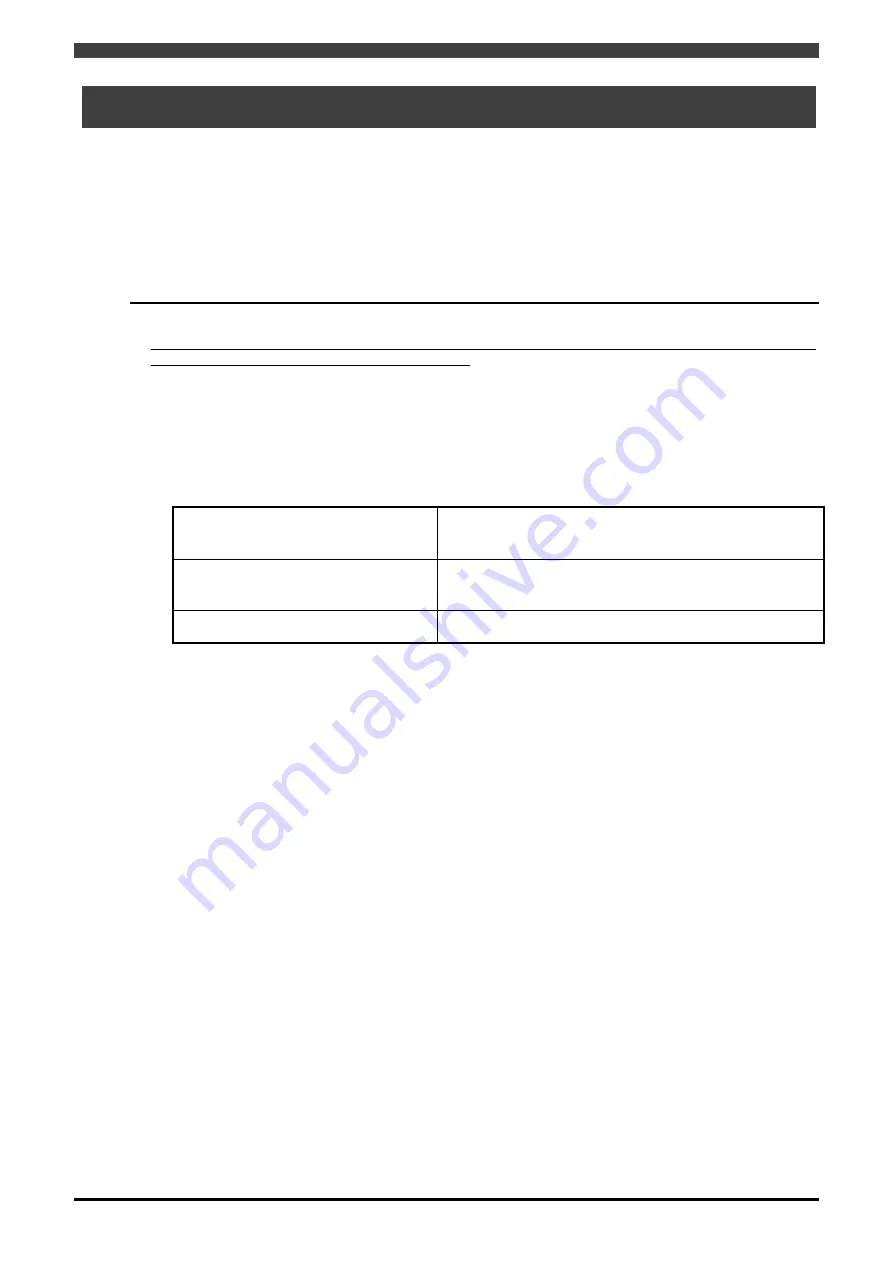
2.5 Operating Range, Angle and Speed Monitoring Function
2-25
2.5 Operating Range, Angle and Speed Monitoring Function
During operating range or speed monitoring operations, the motor position is received from the servo motor
and the current value data of the robot is received from the encoders, and the area and speed set are monitored
by the monitoring routine inside the RMU.
The operating range monitoring function monitors that the robot axis angles and its TCP (Tool Center Point)
do not exceed the operating ranges which have been set, and if one of the angles or the TCP does exceed the
ranges, robot is stopped by shutting off the safety outputs.
The speed monitoring function monitors that the TCP speed does not exceed the operating speed which have
been set, and if it does exceed the speed, robot is stopped by shutting off the safety outputs.
2.5.1 Collaborative operation with human
Compliance to ISO 10218-1 and -2 : 2011 by utilizing partial area limitation and speed monitoring, in case
of performing collaborative operation with human
Robot is just one of constructive part in manufacturing system, so robot is not designed enough safely for the
collaborative operation with human. Collaborative operation is dynamic, so monitoring distance and monitoring
speed should be determined by the risk assessment according to the system. Displaying of speed and
separating distance should be included in the information of usage.
Relative speed between human and robot should be considered when the minimum safety separating
distance is calculated. Please refer to ISO 13855 and or so to calculate this distance.
Please perform the verification and/or validation kin accordance with following item.
Usage of collaborative operation is
determined by the risk assessment
・
Review of the schedule, circuit diagram and design
document that is unique for the system
・
Risk assessment review in accordance with the task
Displaying of speed and separating
distance is included in the information of
usage
・
Review of the schedule, circuit diagram and design
document that is unique for the system
・
Risk assessment review in accordance with the task
ISO 10218-2 is referred in order to design
collaborative operation
・
Test for real usage
Summary of Contents for RMU20-20
Page 2: ......
Page 6: ...Contents 4 ...
Page 8: ......
Page 26: ...1 4 EC DECLARATION OF CONFORMITY FOR MACHINERY 1 18 NOTE ...
Page 68: ...2 9 Enabling RMU 2 40 NOTE ...
Page 70: ......
Page 100: ...3 4 Setting when a slider unit is used 3 30 NOTE ...
Page 102: ......
Page 138: ...4 4Approval 4 36 8 Approval is completed The following screen will be displayed ...
Page 144: ......
Page 154: ...5 4Trouble shooting 5 10 NOTE ...
Page 156: ......
Page 166: ...6 4Trouble shooting 6 10 NOTE ...
Page 168: ......
Page 189: ......