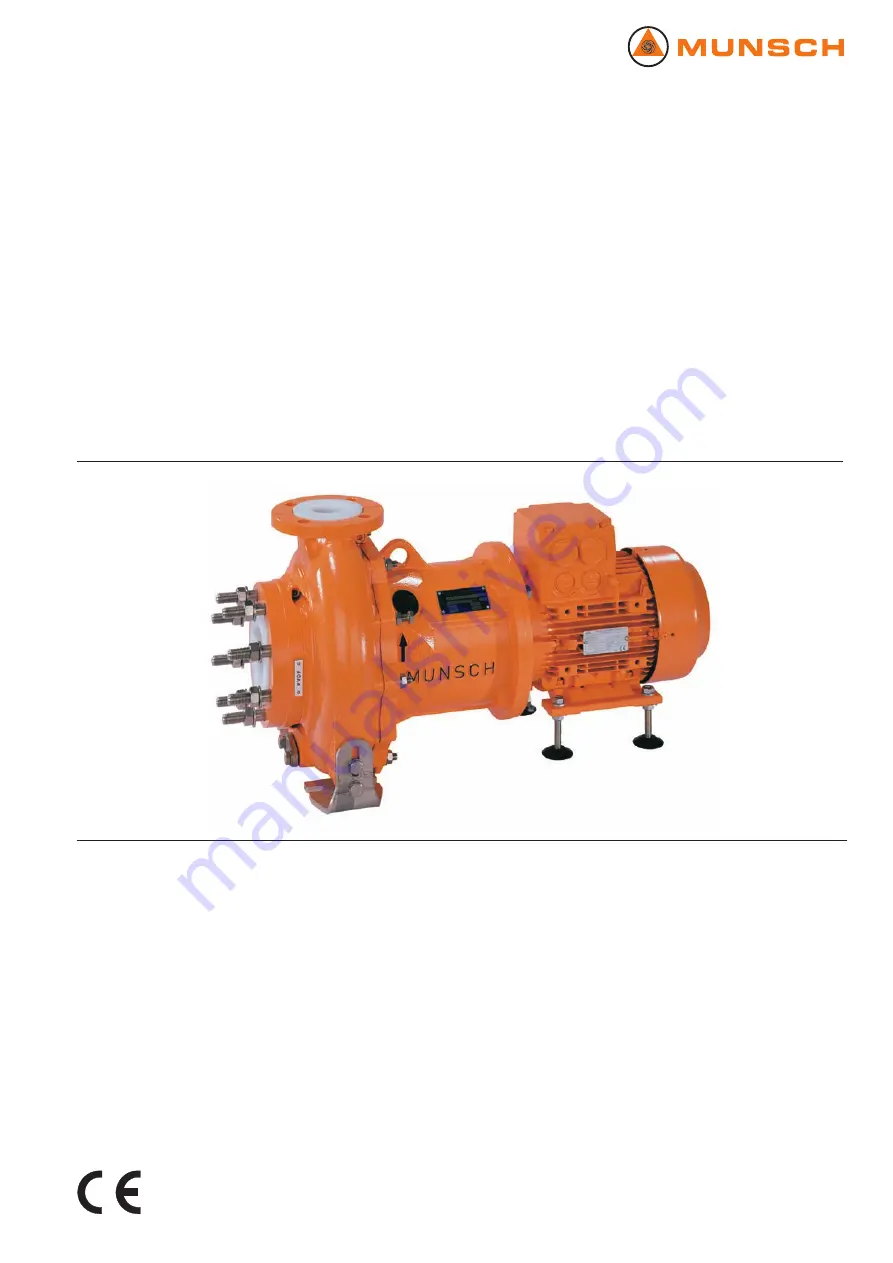
Standard Chemical Pump
Operating instructions
MPC-B series
Version
BA-2006.03
Print-No.
01
VM-No.
EN
Munsch Chemie-Pumpen GmbH
Im Staudchen
56235 Ransbach-Baumbach
Germany
Phone: +49 (0) 26 23-8 98-90
Fax: +49 (0) 26 23-8 98-95
E-mail: [email protected]
Internet: http://www.munsch.de
We reserve the right to make technical changes.