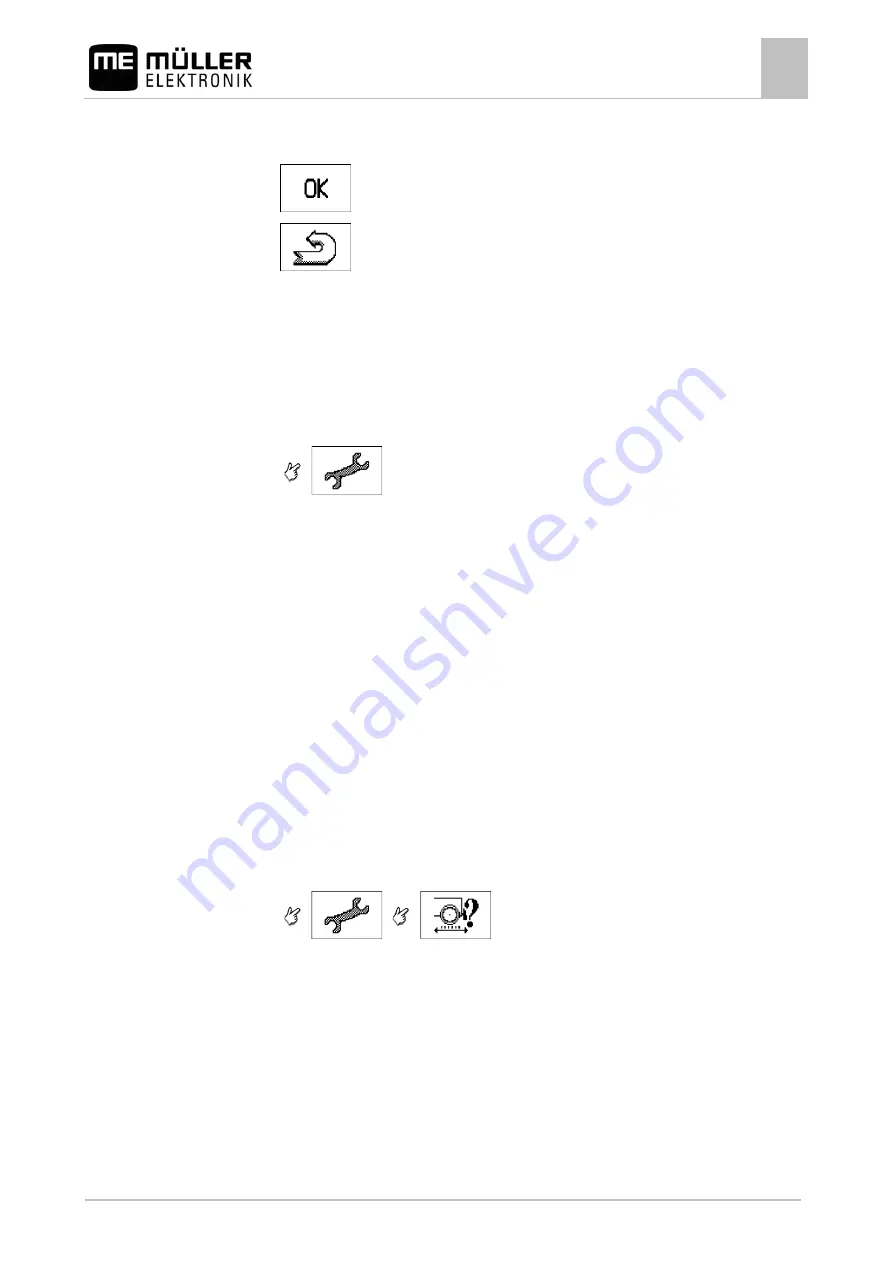
Configuring TRAIL-Control
Configuring the automatic centering
6
30322332-02-EN
V2.20160912
31
5.
Drive the previously measured 100m distance and stop at the end.
⇨
During the drive, the currently determined pulses are displayed.
6.
- Stop calibration.
7.
- Exit screen.
⇨
The number of pulses appears in the line "Wheel pulses".
Using other speed sensors
To configure the job computer for receiving the speed signal through the ISOBUS:
The speed signal can be received through the ISOBUS.
1.
Switch to the "PARAMETERS" screen:
2.
Set the "Wheel pulses" to "0".
Configuring the reverse driving sensor
If the trailed implement or the tractor sends a reverse driving signal through the ISOBUS, the job
computer can use this signal to adjust its regulating behaviour when driving in reverse.
You can find more information in this section: Configuring automatisms when driving in reverse [
The following signal sources are possible:
▪ "None" - The job computer should not expect a reverse driving signal. Even if a reverse driving
signal is transmitted through the ISOBUS, the job computer will ignore the signal.
▪ "ISOBUS" - The reverse driving signal is sent by the tractor or a different job computer through
the ISOBUS.
▪ "Sensor" - A reverse driving sensor is connected to the junction box or cable harness of the job
computer.
To select the reverse driving signal source:
1.
Switch to the "Calibration" screen:
2.
Select the field beside the "Reverse signal " parameter.
⇨
The available signal sources appear. See the description at the beginning of this section.
3.
Select the signal source.
4.
Restart the terminal.
Configuring the automatic centering
The system is capable of centering the position of the trailed implement in certain situations. With
drawbar steering, this means positioning the drawbar straight, and with stub axle steering, aligning
the wheels straight.
6.4.3
Procedure
6.4.4
Signal sources
Procedure
6.5