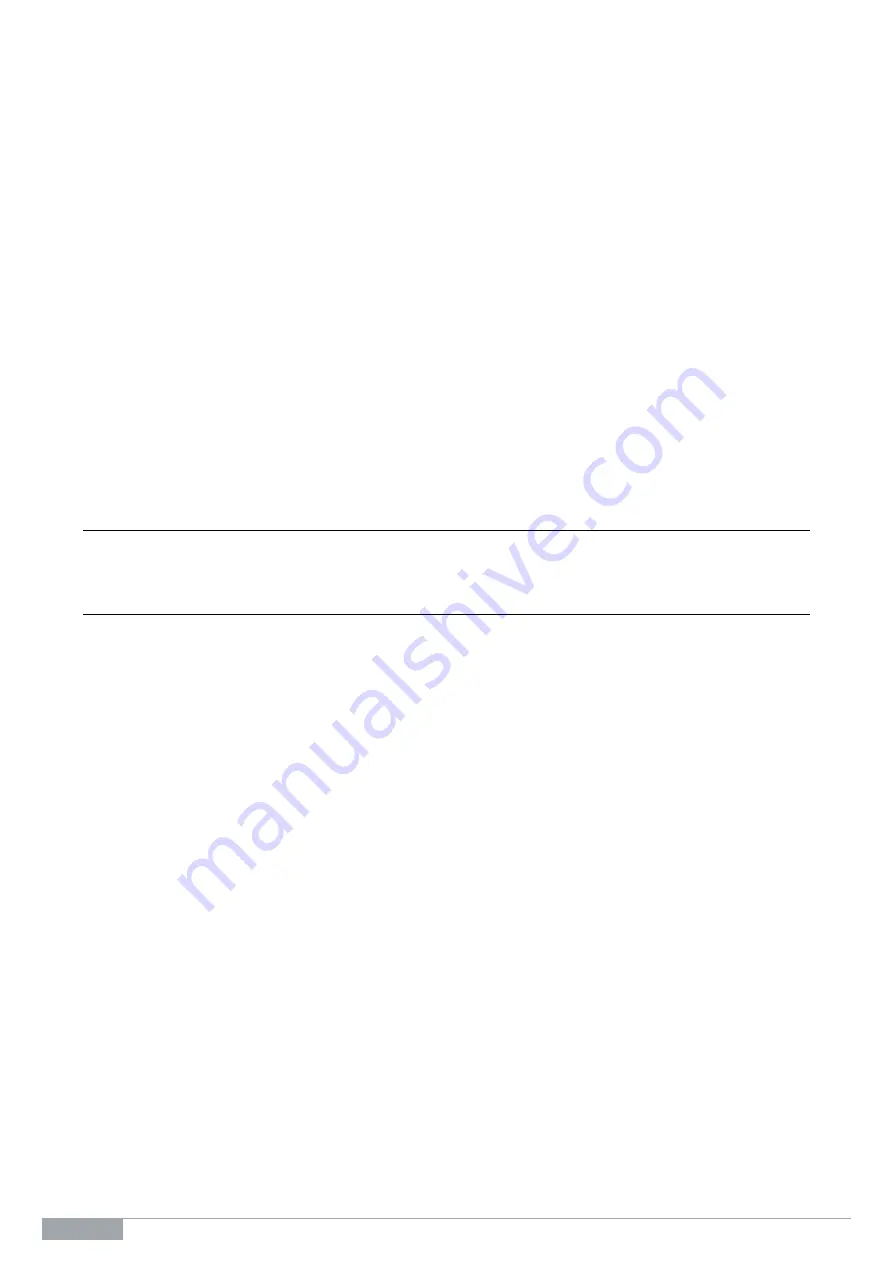
24 | 28
M0160.docx | Rev 1.3 | Modified on 19/05/2020 | © Remote Control Technologies Pty Ltd
Compliance and Standards
TBA
Troubleshooting
Troubleshooting the engine protection system requires more information from the manual that is supplied with
the Muirhead
®
EPS system. A typical engine protection schematic guide is provided in this manual.
During troubleshooting, inspect all components and connectors before any components are replaced. If
connectors are not tight and clean, they can cause intermittent or permanent electrical faults. Ensure the
connectors are tight and clean before any other tests are carried out.
Failure of an electrical component can cause or be caused by the failure of one or more other components.
Always try to find and correct the cause of the engine protection system failure before replacing a component.
Tools needed:
■
Part no. 2005 – Digital Multimeter x 1
■
Part no. 7599 – Circuit Tester x 1
Digital Multimeter
Use the part number 2005 digital multimeter or equivalent for making continuity checks and voltage
measurements. It is recommended that the circuit tester, part number 7599 or equivalent only, be used to test
the three outputs of the EPS control unit.
Note
If the EPS system is installed in conjunction with an idle timer and/or a fire status control unit, it is imperative
that the units are installed in the correct order. Failure to do so may result in the machine not shutting down
correctly.
Refer to the appendix at the end of this manual for the correct sequence.