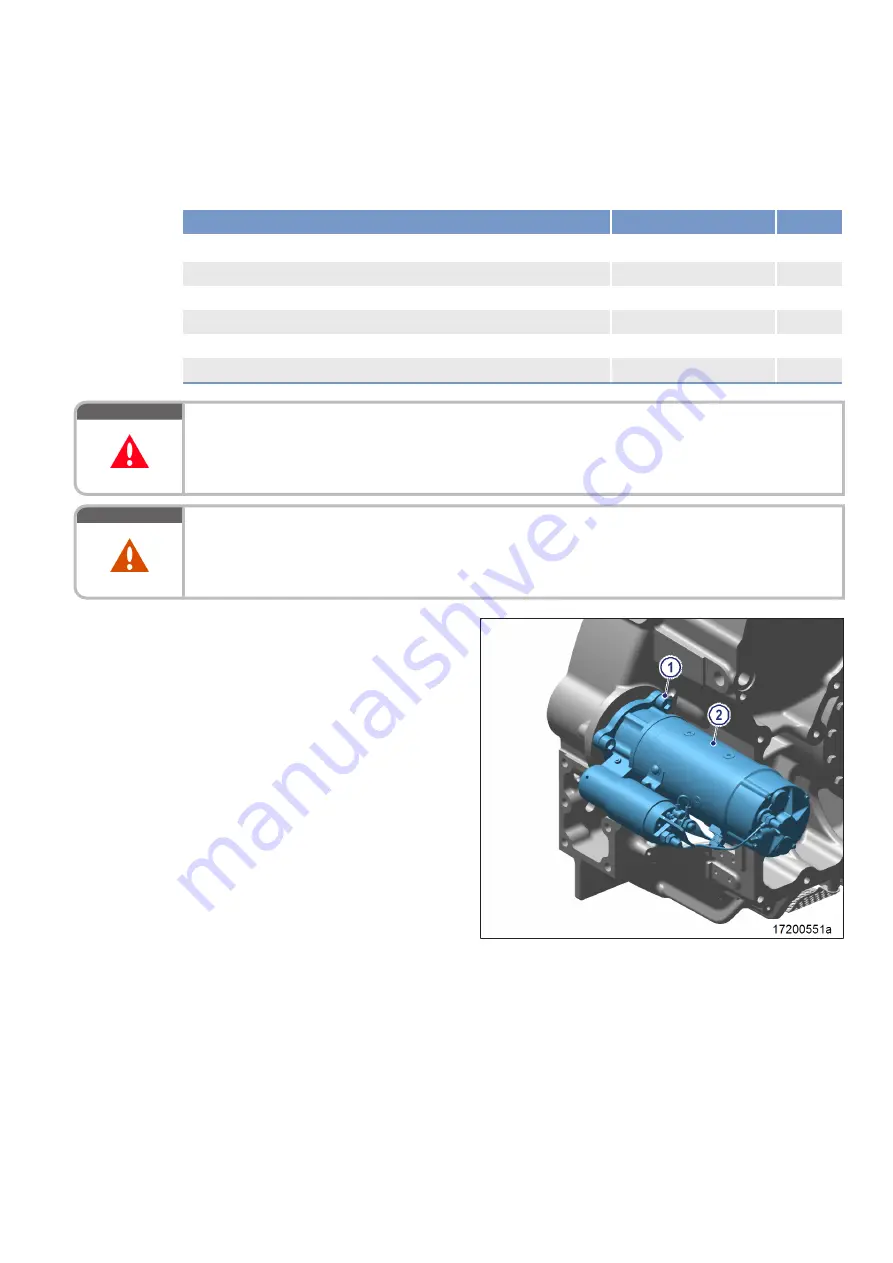
8.8.3 Starter – Installation
Special tools, Material, Spare parts
Designation / Use
Part No.
Qty.
Screwdriver bit
F30378921
1
Socket screwdriver, 14 mm
F30378499
1
Torque wrench 1.0–5.0 Nm
F30452774
1
Torque wrench, 10–60 Nm
F30452769
1
Ratchet adapter
F30027340
1
Lubricating grease (Molykote Longtherm 2 Plus NLGI 2)
X00057299
1
DANGER
Electric voltage supply for operation.
Danger of burns and fatal electric shock!
• Make certain that the power supply to the product is switched off before starting work. Secure
against unintentional switching on!
WARNING
Heavy part, risk of falling or overturning due to lack of stability.
Risk of crushing body or limbs!
• Use appropriate lifting gear and appliances.
• Wear safety shoes.
Starter – Installation
1.
Coat the starter pinion with grease and turn it
back into its initial position as necessary.
Note:
Do not secure crane to engagement magnet.
2.
Attach starter (2) to crane.
3.
Insert starter in opening in flywheel housing.
4.
Align bores for securing screws on starter
with those on flange.
5.
Attach starter (2) to flange with screws (1).
MS150116/04E 2018-04
| Starting System | 211
TIM-ID: 0000014016 - 011