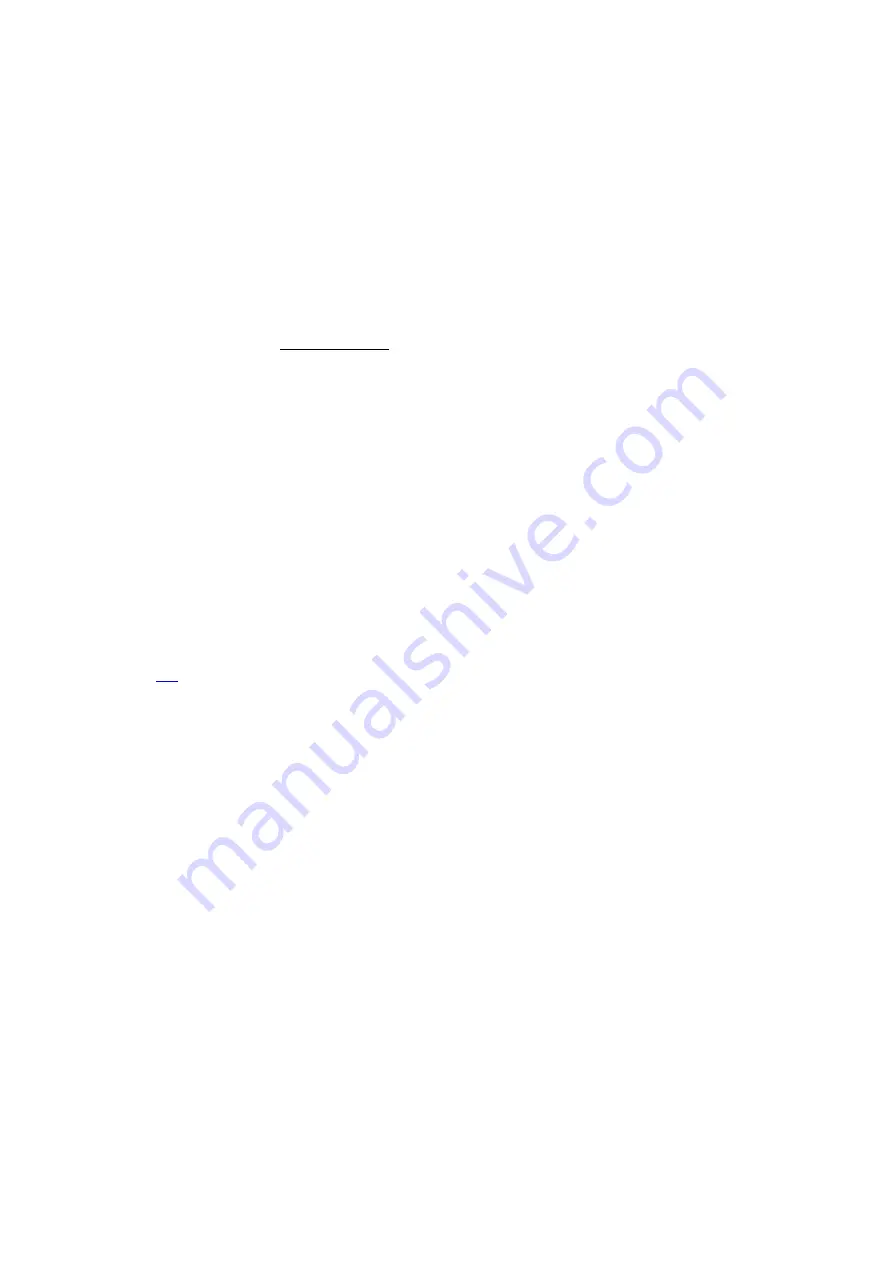
Ps34001b_oi_e.doc / 19.11.15
Page 37 / 43
9.2
Set Directions of Rotation
The direction of rotation must be defined now. Move the positioning drive into the forward
direction (this is the direction to which the drive moves with a positive set-point) either
manually or
with an external positive set-point or
by enabling the positioning drive. In this case the drive gets a speed set-point from
PS340/PS641 corresponding to the value of parameter F02.009 “Positioning Speed”.
Observe in the small monitor window right on the screen behind “Counter Slave” the displayed
count. This counter must count upwards (increase) and the displayed encoder frequency must be
positive.
If the counter counts downward and the frequency is negative, please click on the switch “Slave
Direction” to reverse the counting direction. The “Master Direction” item has no function in the
adjust menu of PS340/PS641 units. Moreover, if you are using the speed set-point by
PS340/PS641 you can use the displayed frequency value to check the settings of the parameter
F02.008 “Frequency Max. Speed”: The displayed encoder frequency must correspond to the speed
set by parameter F02.009 “Positioning Speed”.
9.3
Set Directions of Rotation without PC
If there is no PC or Laptop available the direction of rotation of the encoder of the positioning
drive can be adjusted alternatively:
First of all the position error (differential counter) must be shown on the display of the device (see
chapter
); with factory settings the default display value is the differential counter. Then you
must move the positioning drive to forward direction (this is the direction to which the drive
moves with a positive speed set-point). The differential counter thereby must count downwards,
i. e. the position error must decrement to negative values. If the differential counter counts
upwards, please reverse the counting direction by parameter F04.034 “Counting Direction”.
9.4
Setting of the Proportional Gain
The register “Gain Correction” determines how strong the controller responds to position and
speed errors of the drive. In principle, this setting therefore should be as high as possible.
However, depending on dynamics and inertia of the whole system, too high gain values will
produce stability problems.
Please try to increase the setting of Correction Gain from 1.000 to 1.500, 2.000, 2.500, 3.000 etc.
However, as soon as you find unsteady operation, noise or oscillation, you must reduce the
setting again accordingly.
At this point all important settings are done. Please stop the adjust program by button “Stop” and
leave it by button “Exit”. The system is ready for operation now and you can carry out the first
positioning.