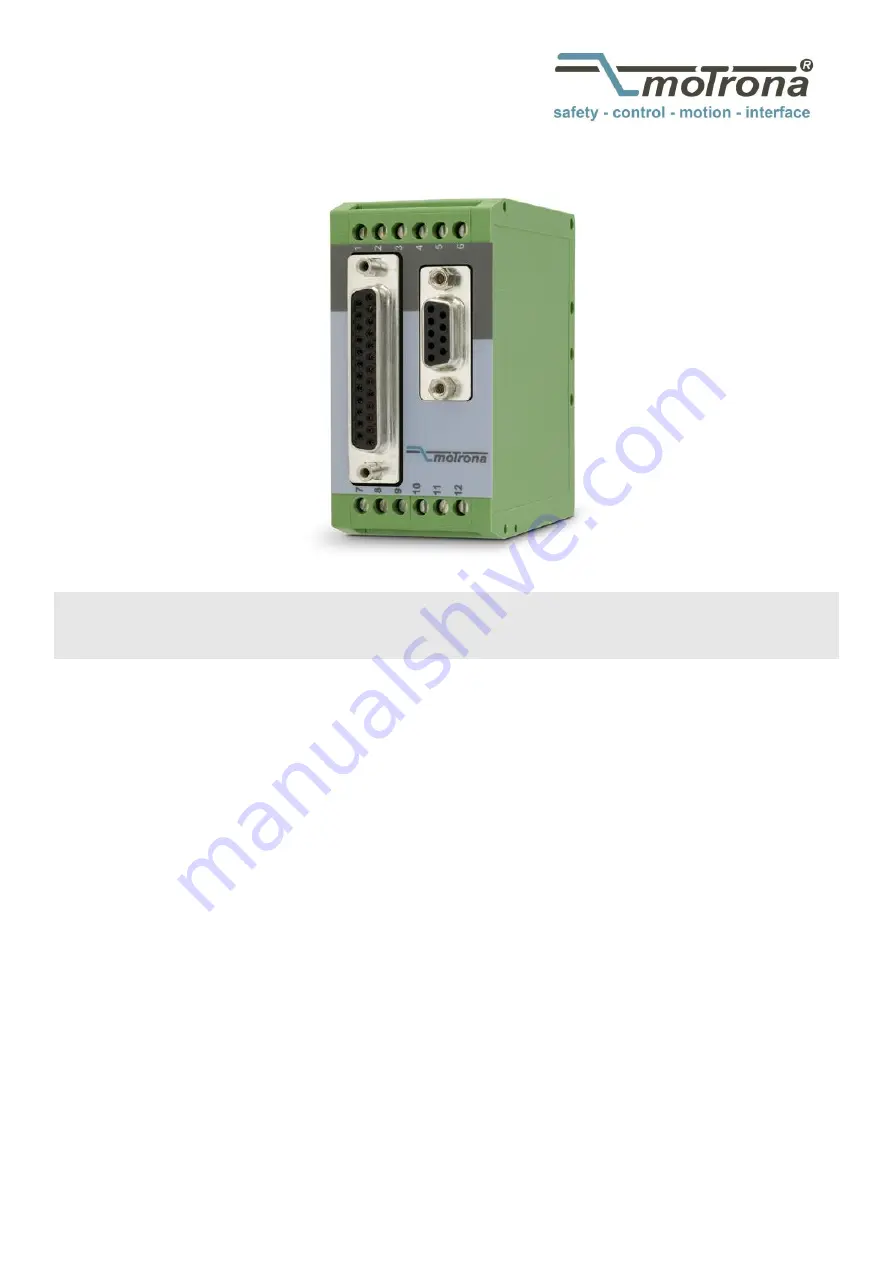
Operating Manual
motrona GmbH, Zeppelinstraße 16, DE - 78244 Gottmadingen, Tel. +49 (0) 7731 9332-0, Fax +49 (0) 7731 9332-30, [email protected], www.motrona.com
IP251
Universal SSI / RS232 signal converter for operation with absolute SSI sensors and encoders
Product Features:
Converts SSI data as well as serial data to parallel binary, Gray oder BCD data format
Linearization facilities by freely programmable in-/output curves
Additional facilities like bit-blanking, round-loop-operation etc.
Parallel output 25 bits (push-pull, short circuit proof)
RS232 interface for serial readout of the sensor data
SSI: Master or Slave operation
18 to 30 VDC power supply