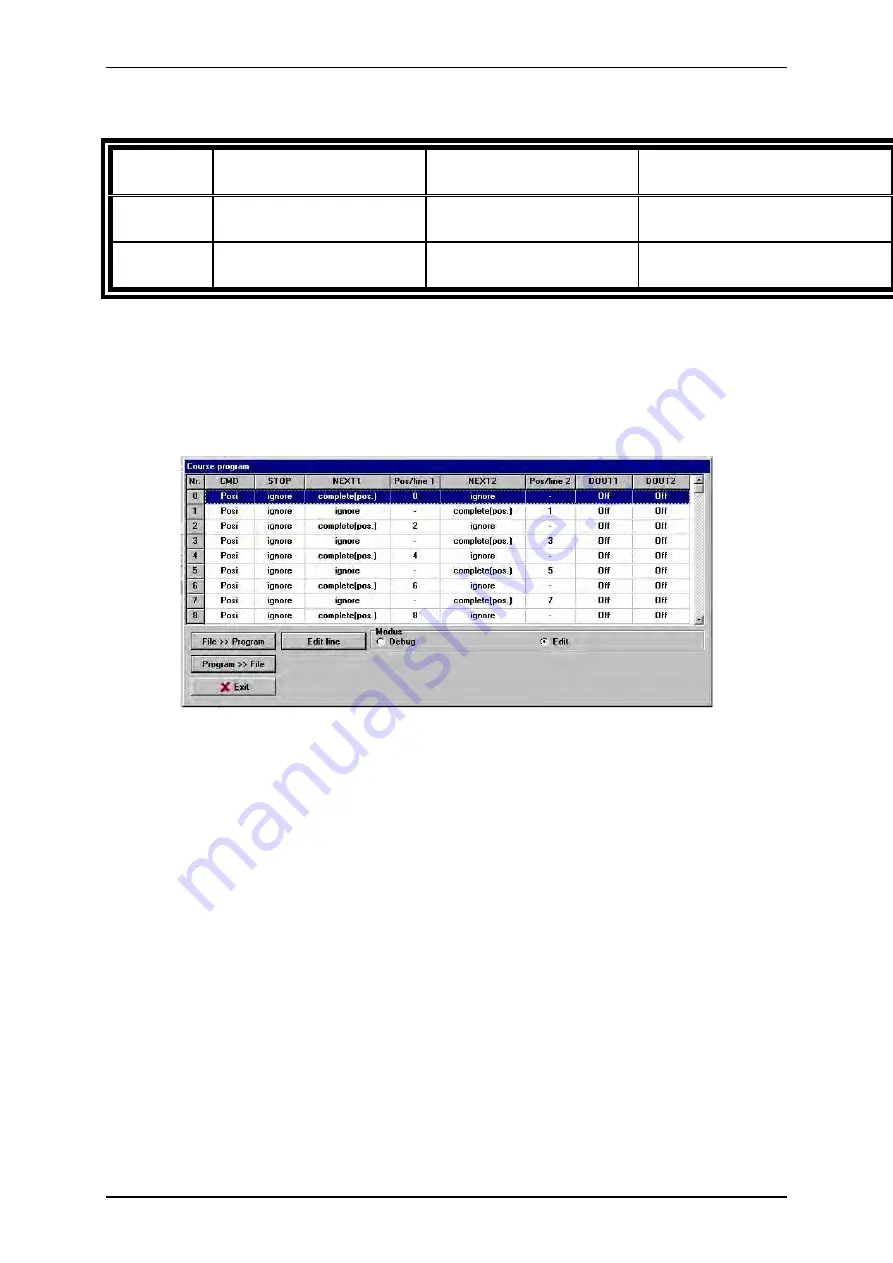
Page 79
Table 10: Available position sets if the course program is active and the
Course/Posi
input = 0
Configuration
:
64 positions:
16 positions:
Explanation:
Table 8
4 groups with 8 positions each
Pos. 0..7, 16..23, 32..39, 48..65
8 complete positions
Pos. 0..7
Standard configuration
Control signal
Course/Posi
at DIN 3
Table 9
4 groups with 8 positions each
Pos. 0, 2, 4, 6, … 60, 62
8 complete positions
Pos. 0, 2, 4, 6, 8, 10, 12, 14, 16
New configuration
Control signal
Course/Posi
at DIN 0
Creating a course program
The menu for managing and creating course programs with up to 32 program lines can be opened
under
Parameters/Positioning/Course program
.
The
File >> Program
can be used to load an already existing course program into the servo
positioning controller while the
Program >> File
button can be used to save a program just created.
In the
Modus
field, you can select either the input mode
Edit
or the monitoring mode
Debug
. The
monitoring mode is described in detail in
chapter Debugging a course program
If you click the
Edit line
button or a line in the table, another window opens in which you can define
commands for the selected course program line.
The program offers the following basic course program commands
Position branch (and linear position sequence)
Branch (Line)
Level test (and unconditional program jump)
End of program
Chapter Course program: Examples
includes three small example applications for a course program.
The various course programs are explained in detail in
chapter End of program
to
User Manual DUET_FL „DUET_FL 48/10“
Version 1.1 Motor Power Company
Summary of Contents for DUET_FL 48/10
Page 3: ...ber dieses Handbuch Page 3...
Page 4: ...Page 4 User Manual DUET_FL DUET_FL 48 10 Version 1 1 Motor Power Company...
Page 12: ...Page 12 List of Figures User Manual DUET_FL DUET_FL 48 10 Version 1 1 Motor Power Company...
Page 15: ...Page 15 List of Tables User Manual DUET_FL DUET_FL 48 10 Version 1 1 Motor Power Company...
Page 76: ...Page 76 User Manual DUET_FL DUET_FL 48 10 Version 1 1 Motor Power Company...
Page 196: ...Page 196 User Manual DUET_FL DUET_FL 48 10 Version 1 1 Motor Power Company...