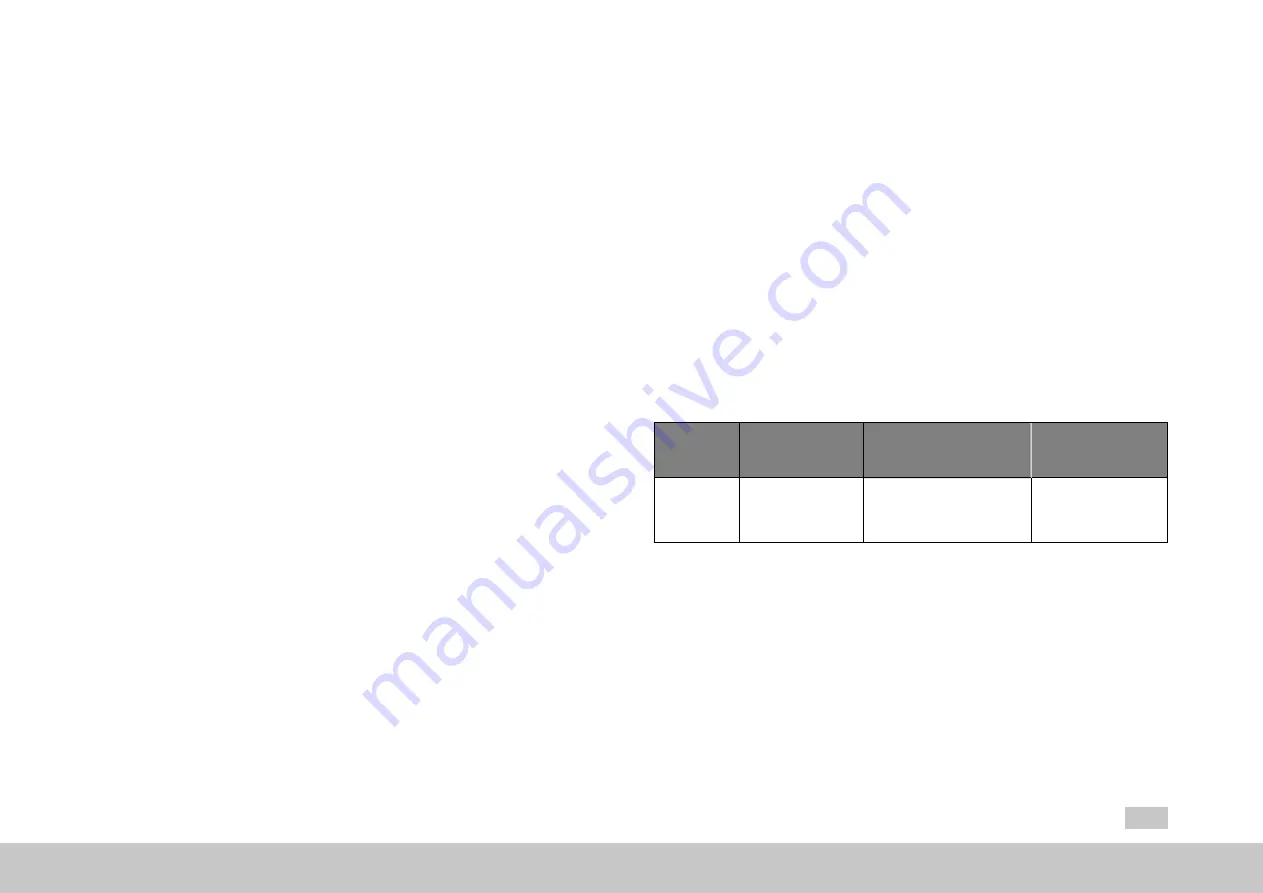
6.12 Multi-turn encoder as a single-turn
encoder
By way of parameters P 548[0] - ENC_CH1_MTEnable = 1 (for Channel 1) and
P 585[0] - ENC_CH3_MTEnable = 1 (for Channel 3) a multi-turn encoder can be run
as a single-turn encoder. This function is used primarily for testing purposes.
MOOG
ID
No.:
CB40859-001
Date:
02/2018
MSD Servo Drive - Device Help
101
6 Encoder
6.13 Distance-coded reference marks
In the case of encoders with distance-coded reference marks, multiple reference
marks are distributed evenly across the entire travel distance. The absolute position
information, relative to a specific zero point of the measuring system, is determined
by counting the individual increments (measuring steps) between two reference
marks. The absolute position of the scale defined by the reference mark is assigned
to precisely one measuring step. Before an absolute reference can be created or the
last selected reference point found, the reference mark must be passed over. In the
worst-case scenario this requires a rotation of up to 360°. To determine the
reference position over the shortest possible distance, encoders with increment-
coded reference marks are supported (e.g. HEIDENHAIN ROD 280C).
The reference mark track contains multiple reference marks with defined increment
differences. The tracking electronics determines the absolute reference when two
adjacent reference marks are passed over after just a few degrees of rotation.
Number of
pulses (P
542)
Number of ref-
erence marks
Basic increment G Nom-
inal Increment A (P 610)
Basic increment G
Nominal increment
B (P 611)
18 x 1000
lines
18 basic marks
+ 18 coded
marks = Σ 36
Reference measure A =
1000 lines
corresponding to 20°
Reference
measure B =
1001 lines
Table 6.37: Example of a rotary system on encoder channel Ch1