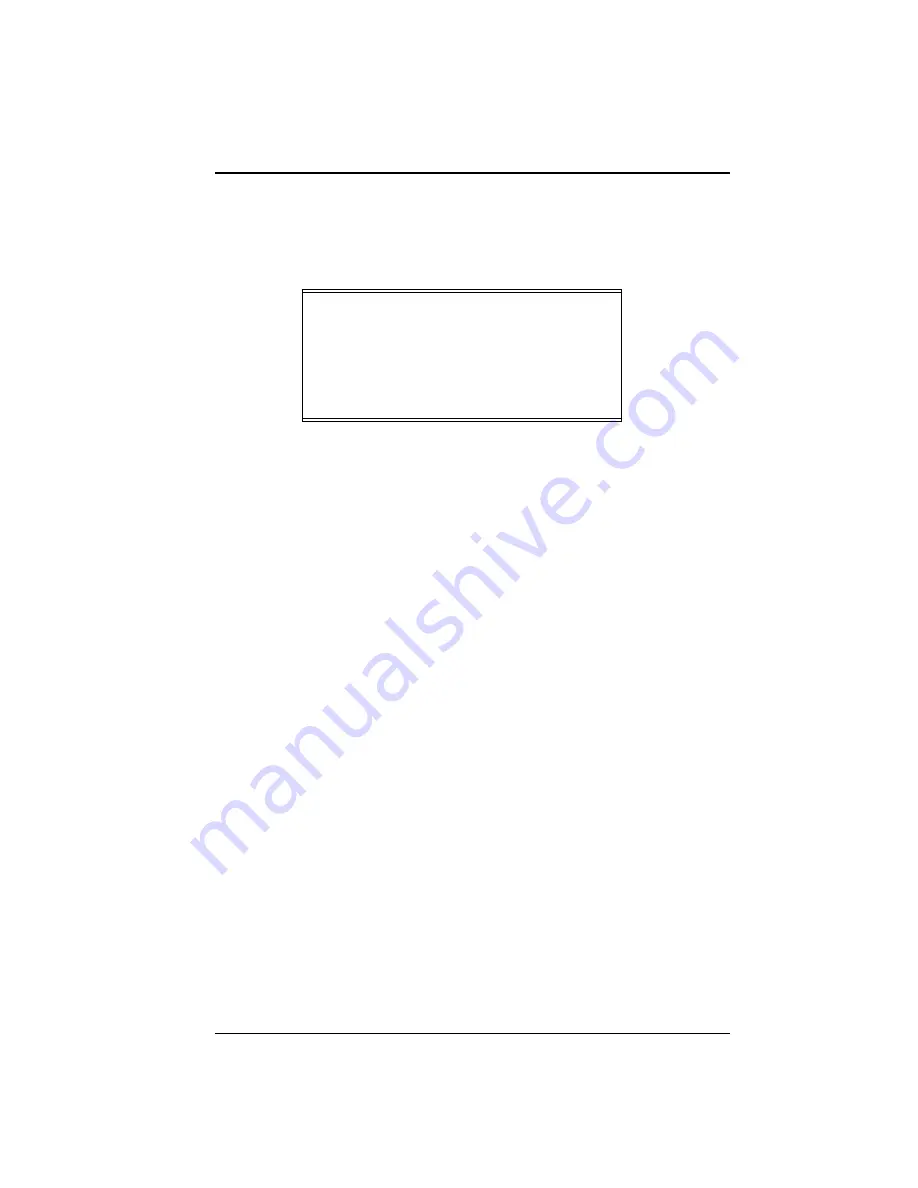
Maintenance
SkanWasher 300 User Guide
33
Microplate Lift Adjustment (Tilt and Vertical)
The microplate lift is factory adjusted for optimal operation and should nor-
mally not need further adjustments. Dispense and aspirate probe placements
can be adjusted for each program through software setup.
Two versions of microplate lift:
Version A: If washer serial number is 1001-1319, proceed to
Section A
.
Version B: If washer serial number is 1320 or higher, proceed to
Section
B.
Section A
Aspiration Probe column angle adjustment.
To be performed when columns 1-12 are not aligned to the aspiration probes.
Step 1
Set aspiration probe height through the program configuration in the
software.
Step 2
Loosen the three screws on the right side of the instrument labeled 1,
2, and 3 (see Figure 14).
Step 3
Adjust the microplate platform by tilting until all probes aligned into
wells.
Step 4
Fasten the screws labeled 1, 2, and 3 (see Figure 14).
Step 5
Verify the aspiration probes are aligned to columns 1 through 12. If
necessary, re-adjust if indicated.
S
CAUTION:
The
Microplate
Lift adjustment
should be
performed only by a qualified
service personnel or when
instructed by a Technical
Support Representative.
Summary of Contents for SkanWasher 300
Page 1: ...SkanWasher 300 User Guide AN ALL INCLUSIVE AUTOMATIC MICROPLATE WASHER...
Page 10: ......
Page 16: ......
Page 22: ......
Page 30: ......
Page 40: ...Maintenance 30 SkanWasher 300 User Guide Figure 11 Wash Head Inlet Channel Seal Block...
Page 48: ...Maintenance 38 SkanWasher 300 User Guide Figure 16 Row Angle Adjustment Lift Version B...
Page 56: ......
Page 62: ......
Page 64: ......
Page 66: ......
Page 68: ......