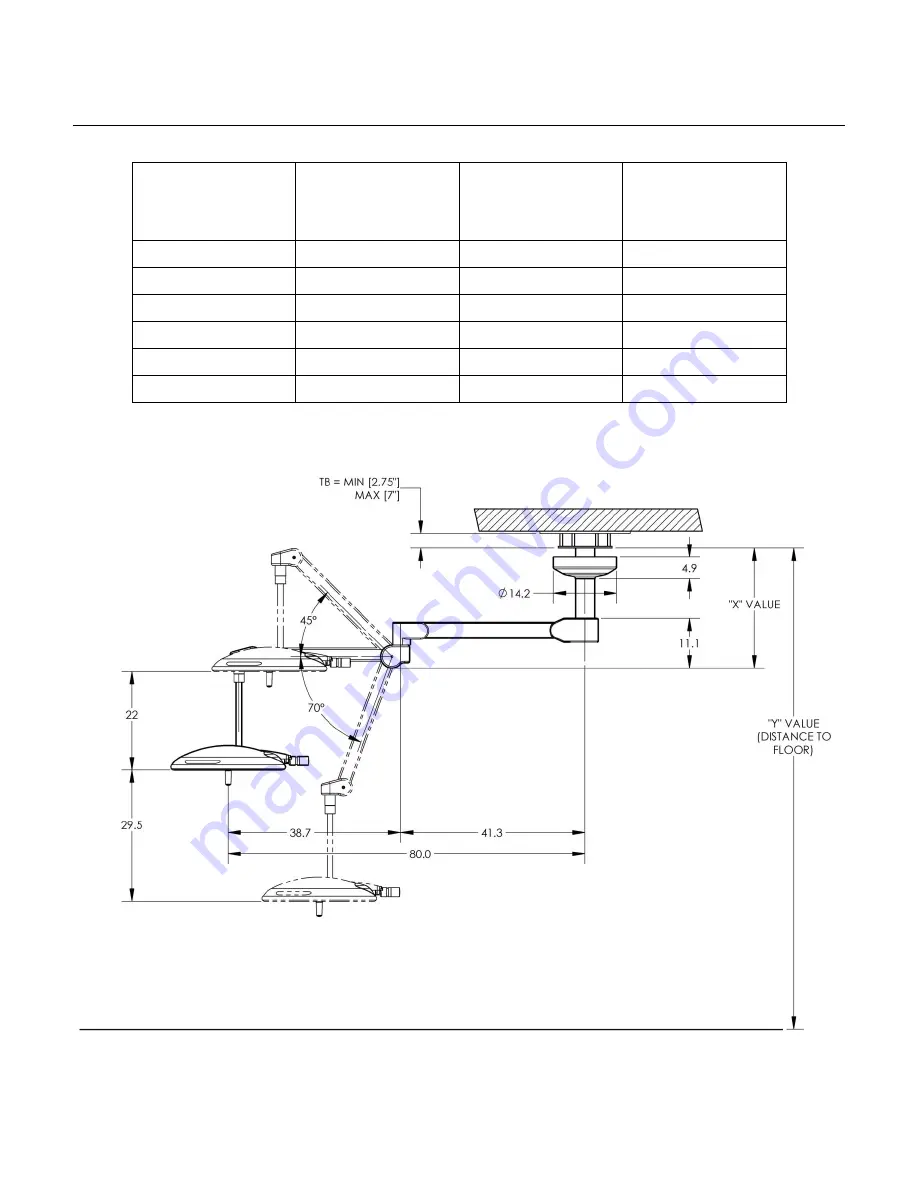
System Two LED Installation and Service Manual (1003385 Rev. C)
Page 21
Section 3
Ceiling Rod Calculation, Single Mount
Use the following table to select the correct length ceiling rod for your application
Ceiling Mounting
Height
“Y”-Value
Ceiling Rod
Length
“X"-Value
Head Room to
Bottom of Extension
Arm
“Y”-Value – X-Value
9'0”/108”
8”
19”
89”
9'6"
/114”
16"
27
”
87
”
10'0”/120”
24"
35
”
85”
10'6"
/126”
32"
43
”
83”
11'0”/132”
39"
50
”
82
”
12'0”/144”
47"
58”
86
”