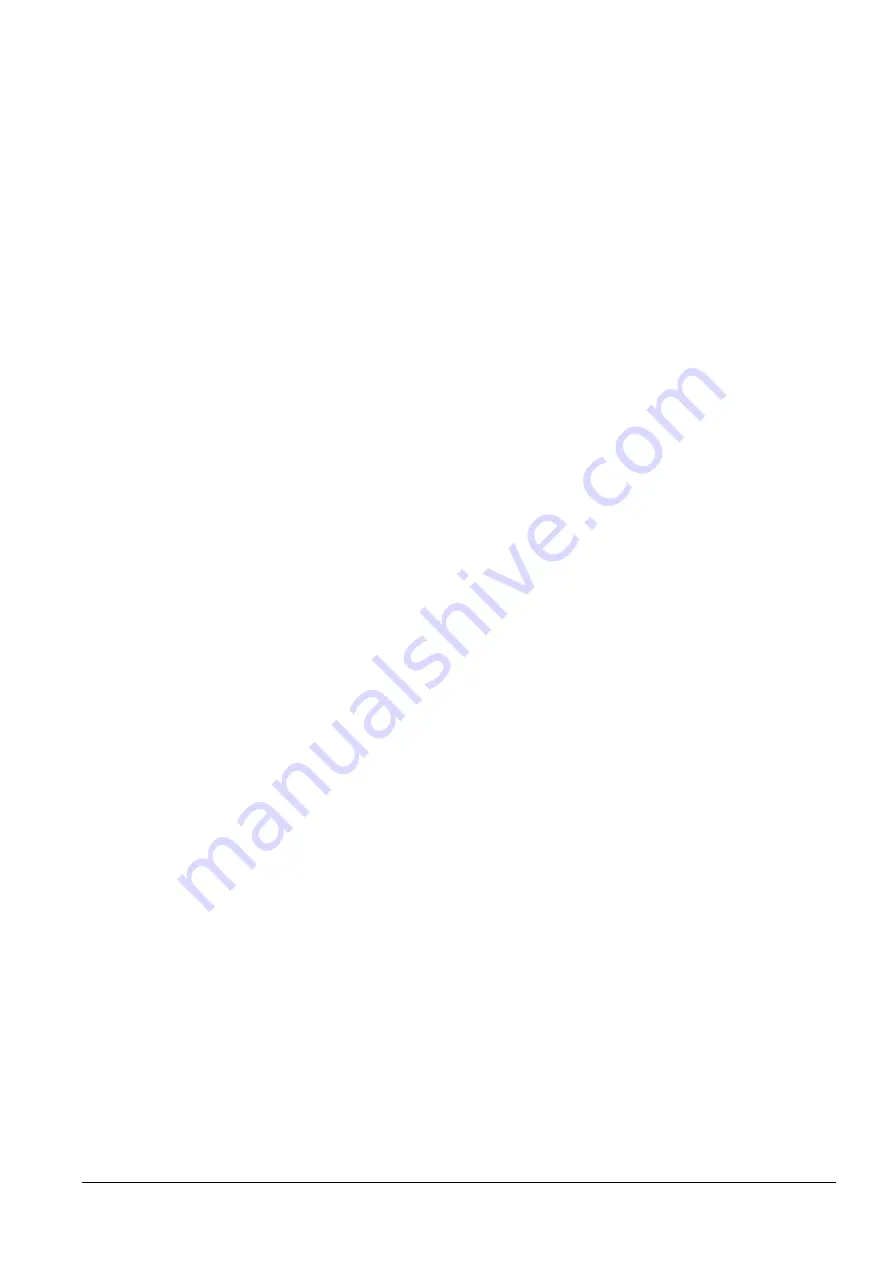
MKS Instruments UK Ltd
V2000-C/E Hardware Manual – SP102005.102 March 2013
20
Carefully note the valve labels regarding orientation and install it so that the port on the axis of the valve is
connected
to the RGA turbo foreline and the “side” port is installed towards the tool foreline.
The integral gauge must sense the pressure in the process tool vacuum line. Finally, when it is permissible to
interrupt the process tool, connect the SurgeProtector to the tool vacuum. Connect the supplied length of 4mm
tubing from the spare fitting on the valve-solenoid manifold block to the SurgeProtector actuator and plug-in its
electrical cable to the matching connector at the harness near the RGA turbopump.
When operating the RGA, it is essential that the tool vacuum be kept <2 torr at all times. Depending upon the
dynamics of tool foreline pressure rises and the length of foreline bellows from the turbopump to the
SurgeProtector, the RGA system can tolerate up to 1 minute of isolation before shutting-down the RGA vacuum
system due to foreline over-pressure condition.
If the tool vacuum line cannot meet these requirements, and independent backing pump will be required for the
RGA. This pump must be appropriate to handle up to 20 sccm of gas flow at <2 torr, and be compatible with the
process gases being sampled. Furthermore, all appropriate safety and environmental regulations regarding
exhaust scrubbing and personnel exposure must be strictly followed.
Heater jackets
The Vision 2000C/E is supplied with two heater jackets fitted: one on the main RGA chamber; and another
around the inlet valve assembly.
There is no need to remove the heater jacket during the installation and testing procedure. The heater jacket
enables the quadrupole chamber to be kept warm during normal operation, and to be baked, which should be
done before attempting to acquire critical data. Note that the heater jacket is designed to be a tight fit.
When properly installed, the main chamber jacket covers from the face of the RGA analyser flange to the radial
tubulation for inlet purge gas fitting. The shorter inlet jacket installs similarly, with the snaps finishing on the same
side as those of the main jacket.
The temperature of the two heater jackets is monitored and controlled via the Interface Module mounted to the
turbo pump. No user adjustments are required.
MicroVision2 installation
Slacken the hex bolt on the clamping ring so the ring can be freely rotated. Line up the slot on the analyser
connector with the pip on the flange of the analyser.
Gently slide the Microvision2 unit on to the analyser. TAKE GREAT CARE the pins on the vacuum feedthrough
are easily damaged. DO NOT force the Microvision2 unit on to the analyser.
When all of the pins are engaged, push the Microvision2 firmly onto the analyser to ensure electrical continuity.
The last 3mm (1/8”) is important. When correctly fitted the front face of the RF/analyser connector should butt up
against the analyser flange.
Finally, tighten the clamping ring enough to securely hold the Microvision2 to the analyser.