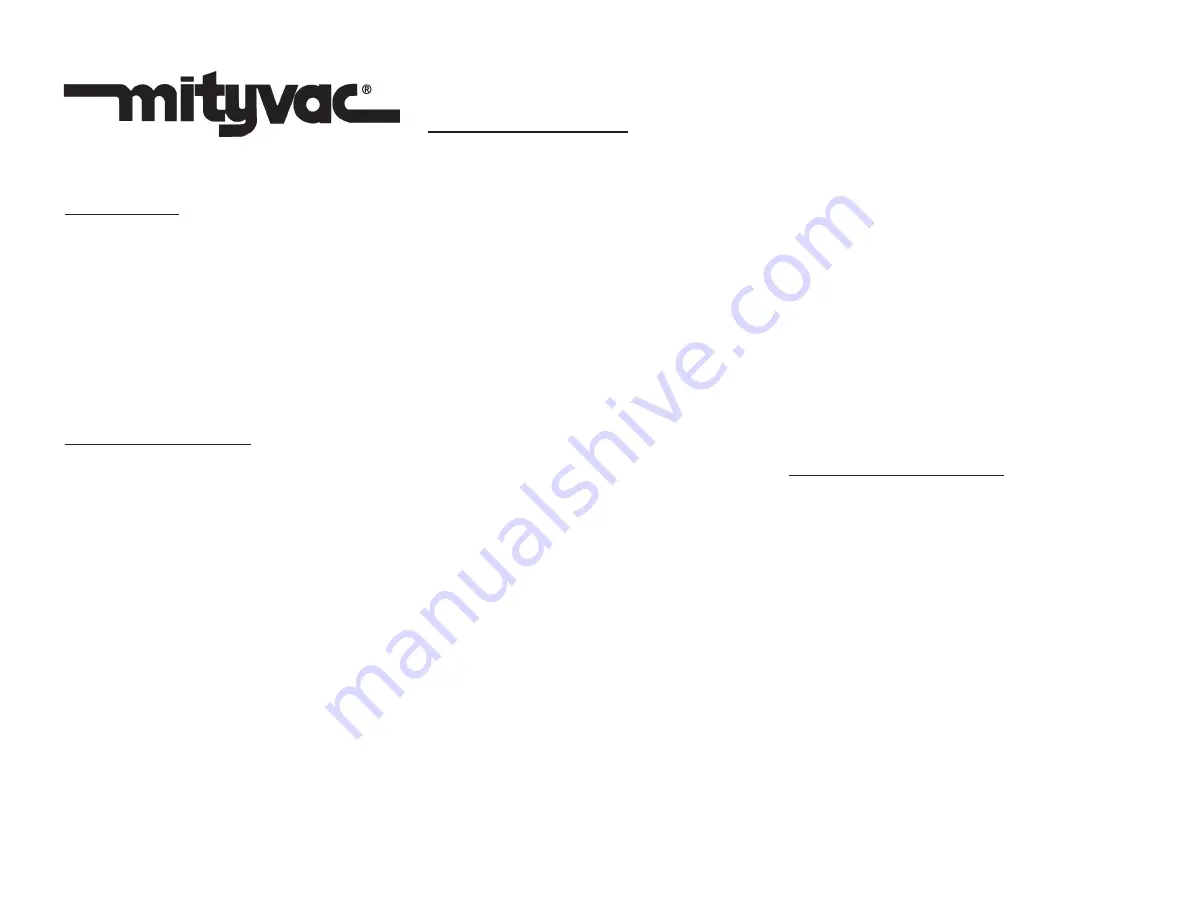
COMPRESSION TEST KIT P/N MV5520
Always read instructions carefully prior to use.
General Description
The
Mityvac
Compression Tester measures how much pres-
sure a cylinder of the engine will produce. The dial face of the
tester gauge has three scales of measure: pounds per square
inch (psi), bar and kilograms per centimeter squared (kg/cm²).
To test the compression level of a given cylinder, thread the
compression test hose assembly into the spark plug hole of the
cylinder to be tested.
The
Mityvac
Compression Test Kit can perform two tests: the
dry compression test and the wet compression test. The result
of performing these tests will provide an indication of the condi-
tion of the piston rings, the cylinders, and valve-train.
Precautions & Diagnostic Notes:
WARNING: DO NOT use the ignition switch during the
compression test on fuel injected vehicles. Use of a re-
mote starter switch to crank the engine is recommended.
Fuel injectors on many late model vehicles are triggered
by the ignition switch during the cranking mode, this
could result in a fire hazard or contamination of the en
-
gine’s oil crankcase with fuel.
Always use eye protection when performing compression
tests.
An engine in good operating condition will produce a certain
amount of pressure in each cylinder. Normally, the cylinders
should be within 10 percentage points of one another and
within the manufacturer’s specifications. The pressure should
rise smoothly on each stroke of the engine, until it reaches a
peak.
If the pressure reading fails to rise, or it remains the same
for several strokes of the engine and begins to rise, the likely
cause of the problem is a sticking valve.
If two adjacent cylinders show pressure readings of 20 or more
pounds below the other cylinder readings, suspect a blown
head gasket.
If a cylinder shows a pressure reading of 15 or more pounds
higher than the other cylinders, the probable cause is carbon
build-up inside the cylinder
Dry Compression Test Procedures:
1. Refer to the appropriate service manual for the compres-
sion specifications specific to the engine you are testing.
2. Start engine and allow engine to run until it reaches normal
operating temperature (usually about 15 minutes.) Turn
engine OFF.
3. Install an auxiliary starter switch in the starting circuit.
4. Loosen all spark plugs approximately one turn. While wear-
ing eye protection, use compressed air to carefully remove
dirt and debris from the area around the spark plugs.
5. Remove spark plugs one at a time, marking the number of
the cylinder they were removed from, and place them on
a clean flat surface. This will aid you in identifying problem
cylinders, by allowing the comparison of spark plug appear-
ance to the compression level of a given cylinder.
NOTE: When testing engines with two spark plugs per
cylinder, it is only necessary to remove the spark plugs
located on the exhaust side.
6. On vehicles with standard distributors, disconnect the coil
wire (high tension lead) from the distributor cap and secure
it to a suitable ground or disable the ignition by disconnect-
ing the positive (BAT) terminal from the ignition coil.
7. On vehicles with a distributorless ignition, disable the igni-
tion system by removing the electronic ignition (control)
module fuse or disconnect the crank angle sensor.
NOTE: Refer to the appropriate service manual to
determine which fuse or component to temporarily
remove or disconnect.
8. Remove air cleaner from carburetor or throttle body and
secure throttle linkage in wide-open throttle (WOT) position.
NOTE: NEVER place anything inside the throttle body;
damage to the fuel injector(s) could result. On vehicles
equipped with port fuel injection, remove throttle link-
age covers (as necessary) and secure throttle linkage
in the wide-open throttle (WOT) position.
9. Crank engine several times to ensure removal of any
foreign matter that may have fallen into the cylinders during
preparation for test.
10. Select the appropriate adapter fitting (14mm, 18mm, or
14mm long-reach) and thread adapter into spark plug hole
of cylinder head.
11. Connect test hose to gauge assembly (using Quick-Discon-
nect Coupler.)
12. Crank the engine at least five compression strokes or until
the pressure reading stops increasing on
gauge.
13. Read the pressure level in the gauge and record
reading along with the cylinder number being tested.
Example: #1-150 psi, #2-145 psi, etc.
14. Repeat this test on each cylinder. If any of the cylin-
der readings are found to be low or uneven, perform
wet compression test.
15. When compression test is complete, return the
spark plugs to their respective cylinders, the throttle
and ignition components to their normal positions.
Wet Compression Test Procedure
CAUTION: DO NOT perform the wet compression
test on any diesel engine. The higher compression
in a diesel engine may cause engine damage or
injury to the technician.
The wet compression is a way to remove the influence
of the piston rings, pistons and cylinders from the com-
pression test. After completing the dry compression test,
squirt approximately one teaspoon of engine oil into
the spark plug holes and crank engine several times to
seal piston rings. Repeat the above listed steps of the
dry compression test.
NOTE:
If the readings during the
wet compression test are greater, then air is leaking
around worn or damaged piston rings. If the reading is
approximately the same for both wet and dry tests then
the valves, valve lifters or the camshaft lobes are worn.
Any low reading of cylinder compression indicates worn
or damaged parts.
To order call 1-800-548-1191 or visit www.partdeal.com - [email protected]