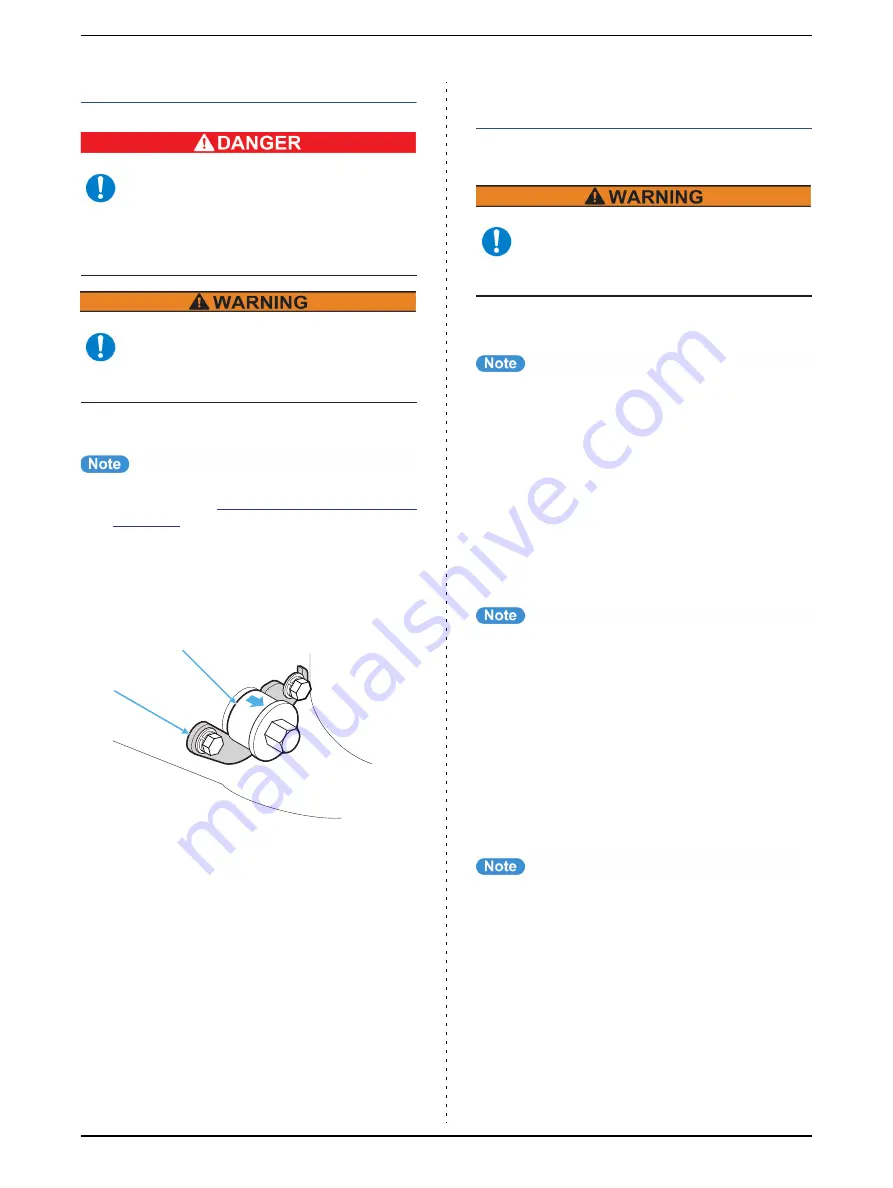
3 OPERATION
Mitsubishi Diesel Engine S16R & S16R2 OPERATION & MAINTENANCE MANUAL
95
Pub. No. K29001-00320 Revision: 1
Manual Turning Gear - Check
Check whether the manual turning gear is pulled
out.
• For the location of the manual turning
1
Check that the manual turning gear
shaft (1) is pulled out and fixed by
the plate (2).
Fig. 3-2 Manual Turning Gear - Check
Air Direct Admission Starting -
Check
■
Starting Air Tank - Check
Drain water from the starting air tank and check the
air pressure.
• The starting air tank may be outside
the scope of our supply. For the details,
refer to such a document as the
specification sheet prepared by the
generator manufacturer.
• If it is not supplied by SME, follow the
instructions in the supplier's operation
manual.
■
Starting Air Compressor - Check
Check the starting air compressor.
• The starting air compressor may be
outside the scope of our supply. For the
details, refer to such a document as the
specification sheet prepared by the
generator manufacturer.
• If it is not supplied by SME, follow the
instructions in the supplier's operation
manual.
■
Air Filter - Check
Check the air filter.
• The air filter may be outside the scope
of our supply. For the details, refer to
such a document as the specification
sheet prepared by the generator
manufacturer.
• If it is not supplied by SME, follow the
instructions in the supplier's operation
manual.
Before starting the engine, pull out
the manual turning gear shaft.
* Starting the engine while the turning gear is
engaged with the ring gear could result in
serious personal injury or destruction of the
engine.
Make sure that the plate of the
manual turning gear is securely
engaged in the shaft groove.
* Otherwise, the devices could be damaged.
(2)
(1)
Be sure to drain water from the
starting air tank.
* Otherwise, water could enter the cylinders
when starting the engine.
Summary of Contents for S16R
Page 215: ......