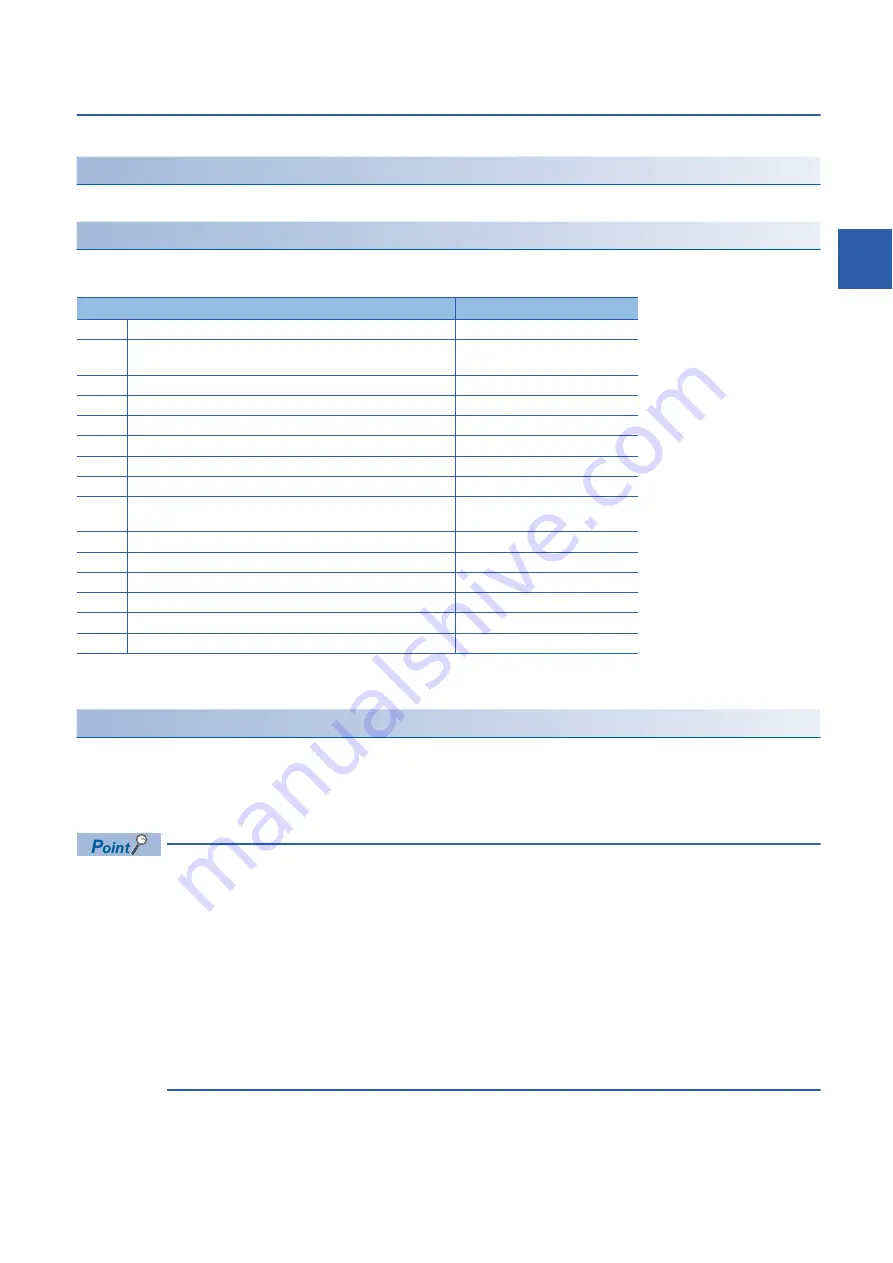
3 MAJOR POSITIONING CONTROL
3.2 Setting the Positioning Data
141
3
LOOP
The LOOP is used for loop control by the repetition of LOOP to LEND.
Operation
The LOOP to LEND loop is repeated by set repeat cycles.
Setting positioning data
When using the LOOP, set the following positioning data.
: Always set,
: Set as required,
: Setting not required
*1
Refer to the following for information on the setting details.
Restrictions
• The error "Control method LOOP setting error" (error code: 1A33H) will occur if a "0" is set for the repeat cycles.
• Even if LEND is absent after LOOP, no error will occur, but repeat processing will not be carried out.
• Nesting is not allowed between LOOP-LEND's. If such setting is made, only the inner LOOP-LEND is processed
repeatedly.
The setting by this control method is easier than that by the special start "FOR loop". (
• For special start: Positioning start data, special start data, condition data, and positioning data
• For control method: Positioning data
For the special start FOR to NEXT, the positioning data is required for each of FOR and NEXT points. For the
control method, loop can be executed even only by one data.
Also, nesting is enabled by using the control method LOOP to LEND in combination with the special start FOR
to NEXT. However LOOP to LEND cannot be set across block. Always set LOOP to LEND so that the
processing ends within one block.
For details of the "block", refer to the following.
Page 143 HIGH-LEVEL POSITIONING CONTROL
Setting item
Setting required/not required
[Da.1]
Operation pattern
[Da.2]
Control method
(Set the LOOP.)
[Da.3]
Acceleration time No.
[Da.4]
Deceleration time No.
[Da.6]
Positioning address/movement amount
[Da.7]
Arc address
[Da.8]
Command speed
[Da.9]
Dwell time/JUMP destination positioning data No.
[Da.10]
M code/Condition data No./Number of LOOP to LEND repetitions/
Number of pitches
(Set the repeat cycles.)
[Da.20]
Axis to be interpolated No.1
[Da.21]
Axis to be interpolated No.2
[Da.22]
Axis to be interpolated No.3
[Da.27]
M code ON signal output timing
[Da.28]
ABS direction in degrees
[Da.29]
Interpolation speed designation method
Summary of Contents for RD77MS16
Page 1: ...MELSEC iQ R Simple Motion Module User s Manual Application RD77MS2 RD77MS4 RD77MS8 RD77MS16 ...
Page 2: ......
Page 316: ...314 9 COMMON FUNCTIONS 9 4 External Input Signal Select Function Program example ...
Page 317: ...9 COMMON FUNCTIONS 9 4 External Input Signal Select Function 315 9 ...
Page 575: ...13 PROGRAMMING 13 4 Positioning Program Examples 573 13 Error reset program Axis stop program ...
Page 643: ......