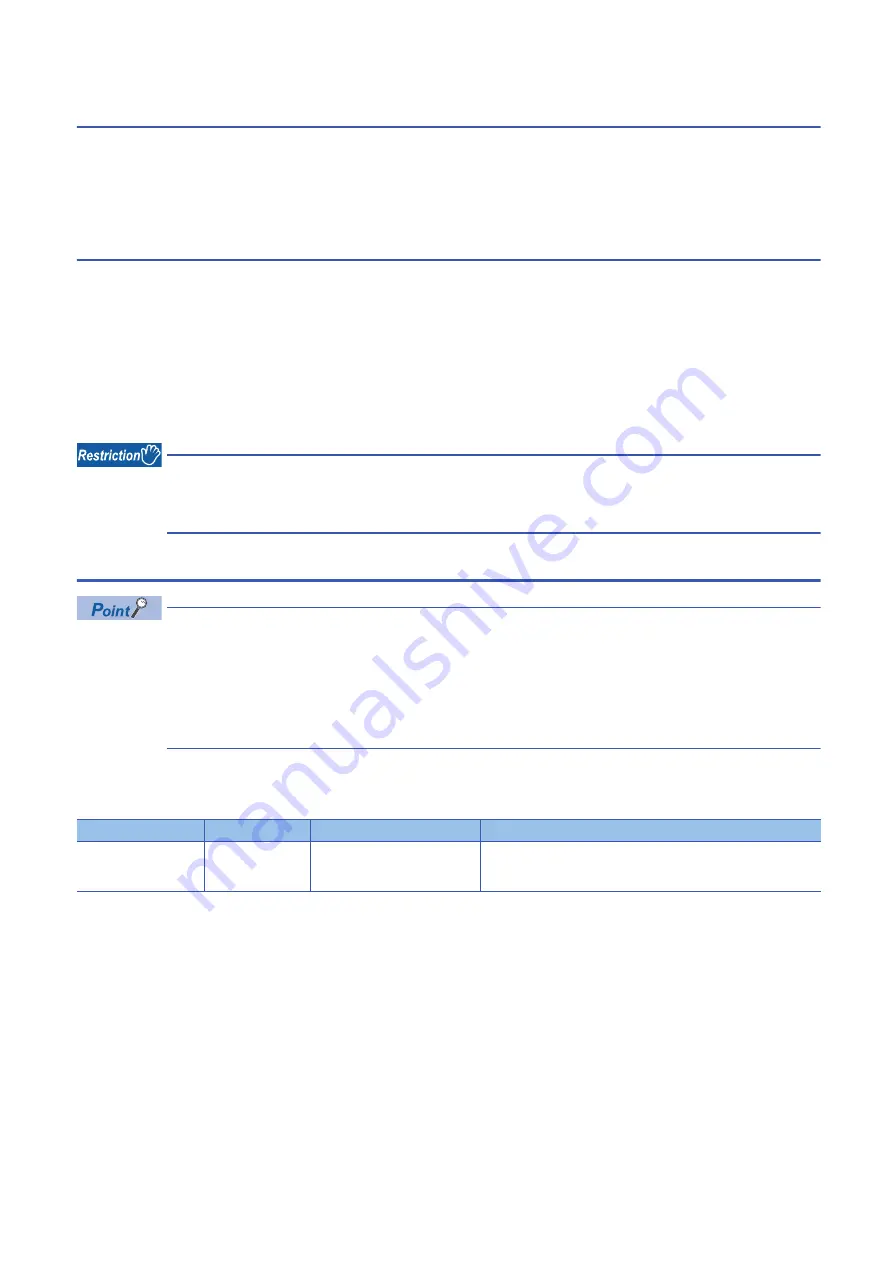
68
3 BASIC FUNCTION
3.11 Electromagnetic brake interlock function
3.11
Electromagnetic brake interlock function
For servo motors with an electromagnetic brake, this function activates the electromagnetic brake at servo-off, upon an error
occurrence, and at other necessary times. By using the electromagnetic brake, the position can be maintained so that the
servo motor will not move due to external force. When this function is used on a system with a vertical axis, a drop in vertical
lift applications can be prevented.
Base circuit shut-off delay time function
The base circuit shut-off delay time function is used in the following cases to prevent the vertical axis from dropping due to
delayed electromagnetic brake operations:
• Under servo-off command
• At forced stop (EM2 is turned off)
• At alarm occurrence
• At network communication shut-off occurrence
The delay time used between the MBR (Electromagnetic brake interlock) shut-off and the base circuit shut-off can be set in
servo parameters.
• This function does not operate on alarms that are not subject to the forced stop deceleration function.
• When the forced stop deceleration function is disabled, this function does not operate at forced stop (EM2 is
turned off) or upon an alarm occurrence or network communication shut-off.
Setting method
For specifications such as the power supply capacity and operation delay time of the electromagnetic brake,
refer to "Electromagnetic brake characteristics" in the following manual.
Rotary Servo Motor User's Manual (HG-KNS/HG-SNS)
For a selection example of a surge absorber for the electromagnetic brake, refer to "Electromagnetic brake
characteristics" in the following manual.
Rotary Servo Motor User's Manual (HG-KNS/HG-SNS)
When the electromagnetic brake is placed in the servo-off state, the MBR and the base circuit both shut off following a short
delay. Set this delay time (Tb) in [Pr. PC02 Electromagnetic brake sequence output]. Refer to the following.
Page 69 When using the forced stop deceleration function
Servo parameter
Symbol
Name
Outline
PC02
MBR
Electromagnetic brake sequence
output
Set the delay time used between the MBR (Electromagnetic brake
interlock) shut-off and the base circuit shut-off.
Initial value: 0 [ms]