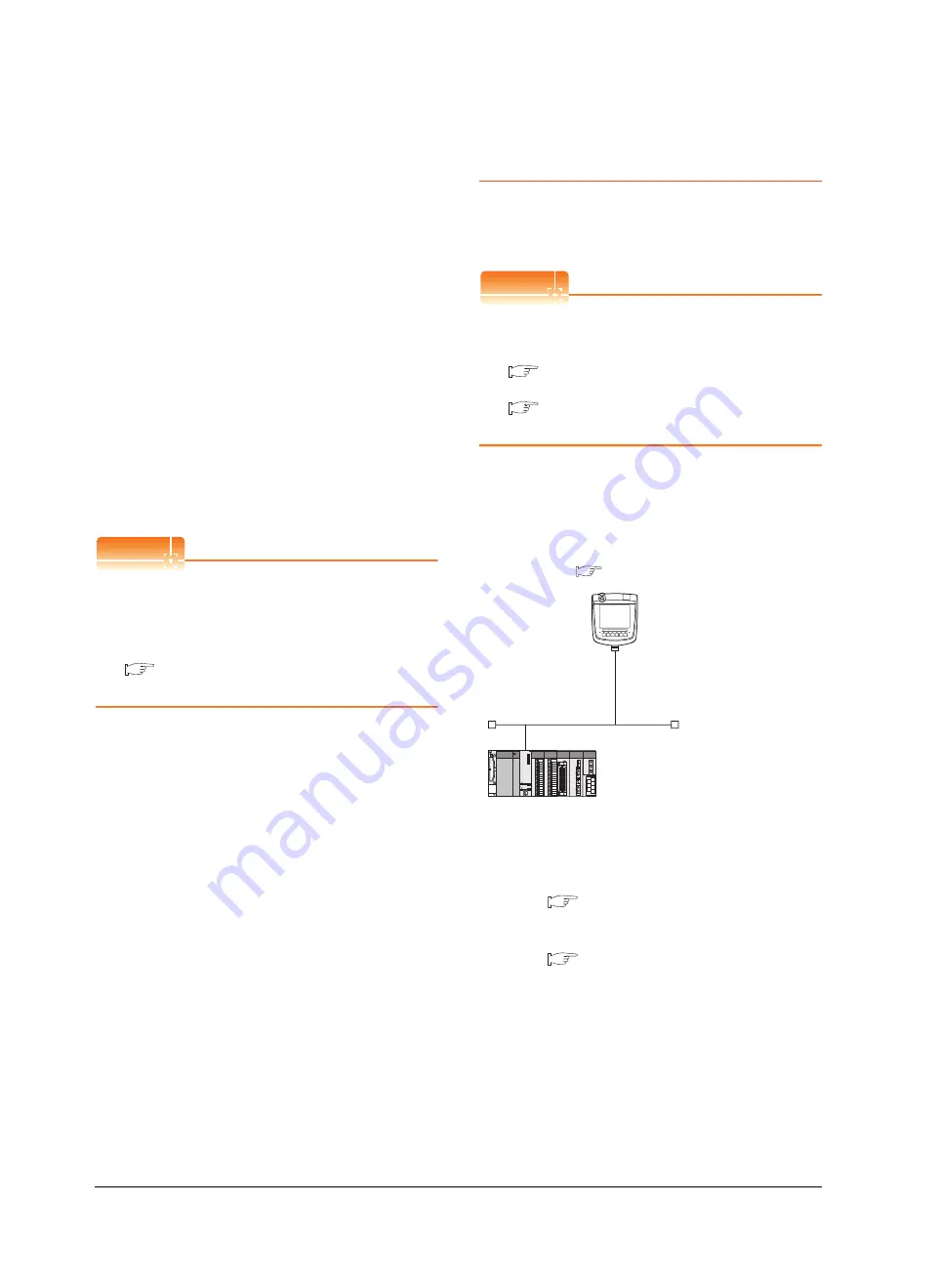
22 - 26
22. ETHERNET CONNECTION
22.4 PLC Side Setting
Checking communication state of C
Controller module (MELSEC iQ-R Series)
(1) When using the Command Prompt of Windows
®
.
Execute a Ping command at the Command Prompt of
Windows
®
.
(a) When normal communication
C:\>Ping 192.168.3.3
Reply from 192.168.0.1: bytes=32 time
<10ms TTL=32
(b) When abnormal communication
C:\>Ping 192.168.3.3
Request timed out.
(2) When abnormal communication
At abnormal communication, check the followings and
execute the Ping command again.
• Cable connecting condition
• Confirmation of switch and network parameter setting
• Operation state of PLC CPU (faulty or not)
• The IP address of C Controller module (MELSEC iQ-
R Series) specified in the ping command
POINT
POINT
POINT
Ethernet diagnostics of CW Configurator
Ethernet diagnostics of CW Configurator is available to
a Ping test from the PLC.
For details of Ethernet diagnostics of CW Configurator,
refer to the following manual.
Manuals of C Controller module (MELSEC iQ-R
Series)
22.4.5
Connecting to Built-in Ethernet
port CPU (one-to-one connection)
This section describes the settings of the GOT and Built-in
Ethernet port CPU in the following case of system
configuration.
POINT
POINT
POINT
Connecting to Built-in Ethernet port CPU
For details of Built-in Ethernet port CPU, refer to the
following manual.
QnUCPU User's Manual (Communication via
Built-in Ethernet Port)
MELSEC-L CPU Module User's Manual
(Built-In Ethernet Function)
System configuration
For connecting one Built-in Ethernet port QCPU to one
GOT, the PLC side settings are not required. Set
[Ethernet] for [Controller Setting] on GT Designer3, and
then connect Built-in Ethernet port QCPU to the GOT.
*1
For the settings when using system devices including a hub
and a transceiver, refer to the following.
22.4.6 Connecting to Built-in Ethernet port CPU
(multiple connection)
*2
These setting items do not exist at the PLC side. However,
the virtual values must be set on the GOT side.
■
[Controller Setting] and [Ethernet] of GT Designer3
<GOT>
(The settings other than the
following are set to the default)
*1
*2
*2
Network No.
: 1
PLC No.
: 1
IP address
: 192.168.3.1
Port No.
: 5001
Communication
format
: UDP (fixed)
Network No.
: 1 (virtual)
PLC No.
: 2 (virtual)
IP address
: 192.168.3.39
Port No.
: 5006 (fixed)
Communication
format
: UDP (fixed)
<Connecting to Built-in Ethernet port CPU>
(The following settings are set to the default)
[Controller Setting] and [Ethernet] of GT
Designer3
■
Summary of Contents for GT16
Page 1: ......
Page 2: ......
Page 46: ...1 4 1 OVERVIEW 1 1 Features ...
Page 54: ...2 8 2 SYSTEM CONFIGURATION 2 2 System Equipment ...
Page 60: ...3 6 3 SPECIFICATIONS 3 4 Battery specifications ...
Page 72: ...5 8 5 UL cUL STANDARDS AND EMC DIRECTIVE 5 2 EMC Directive ...
Page 102: ...6 30 6 OPTION 6 7 Connector Conversion Box ...
Page 106: ...7 4 7 INSTALLATION 7 1 Installing Procedure ...
Page 110: ...8 4 8 COMMUNICATION CABLE 8 1 Overview of Communication Cable ...
Page 130: ...9 20 9 HANDLING OF POWER WIRING AND SWITCH 9 4 Switch Wiring ...
Page 142: ...10 12 10 UTILITY FUNCTION 10 3 Utility Display ...
Page 184: ...11 42 11 DISPLAY AND OPERATION SETTINGS GOT SET UP 11 4 Maintenance Function ...
Page 202: ...12 18 12 COMMUNICATION INTERFACE SETTING COMMUNICATION SETTING 12 3 Ethernet Setting ...
Page 226: ...13 24 13 DEBUG 13 3 Memory Data Control ...
Page 248: ...14 22 14 SELF CHECK 14 2 Batch Self Check ...
Page 350: ...15 102 15 DATA CONTROL 15 3 OS Project Information ...
Page 410: ...19 22 19 TROUBLESHOOTING 19 2 Error Message and System Alarm ...
Page 418: ...App 8 APPENDICES Appendix 3 Transportation Precautions ...
Page 422: ...REVISIONS 4 ...
Page 425: ......
Page 426: ......
Page 427: ......
Page 428: ......
Page 470: ......
Page 510: ...21 22 21 COMPUTER LINK CONNECTION 21 6 Precautions ...
Page 568: ...22 58 22 ETHERNET CONNECTION 22 5 Precautions ...
Page 584: ......
Page 626: ...25 14 25 SERVO AMPLIFIER CONNECTION 25 7 Precautions ...
Page 632: ...26 6 26 ROBOT CONTROLLER CONNECTION 26 6 Precautions ...
Page 647: ...MULTIPLE GOT CONNECTIONS 29 GOT MULTI DROP CONNECTION 29 1 ...
Page 648: ......
Page 659: ...MULTI CHANNEL FUNCTION 30 MULTI CHANNEL FUNCTION 30 1 ...
Page 660: ......
Page 675: ...FA TRANSPARENT FUNCTION 31 FA TRANSPARENT FUNCTION 31 1 ...
Page 676: ......
Page 742: ...31 66 31 FA TRANSPARENT FUNCTION 31 7 Precautions ...
Page 744: ......
Page 766: ...32 22 32 CONNECTION TO IAI ROBOT CONTROLLER 32 7 Precautions ...
Page 802: ...34 10 34 CONNECTION TO OMRON TEMPERATURE CONTROLLER 34 7 Precautions ...
Page 834: ...36 18 36 CONNECTION TO KOYO EI PLC 36 6 Device Range that Can Be Set ...
Page 858: ...38 12 38 CONNECTION TO SHARP PLC 38 6 Device Range that Can Be Set ...
Page 868: ...39 10 39 CONNECTION TO SHINKO TECHNOS INDICATING CONTROLLER 39 7 Precautions ...
Page 902: ...42 6 42 CONNECTION TO TOSHIBA MACHINE PLC 42 6 Device Range that Can Be Set ...
Page 908: ...43 6 43 CONNECTION TO PANASONIC SERVO AMPLIFIER 43 7 Precautions ...
Page 970: ...48 12 48 CONNECTION TO FUJI TEMPERATURE CONTROLLER 48 7 Precautions ...
Page 1052: ...52 26 52 CONNECTION TO AZBIL CONTROL EQUIPMENT 52 7 Precautions ...
Page 1102: ...55 14 55 CONNECTION TO GE PLC 55 7 Precautions ...
Page 1114: ...57 4 57 CONNECTION TO SICK SAFETY CONTROLLER 57 5 Device Range that Can Be Set ...
Page 1128: ...59 2 59 CONNECTION TO HIRATA CORPORATION HNC CONTROLLER ...
Page 1130: ...60 2 60 CONNECTION TO MURATEC CONTROLLER ...
Page 1132: ......
Page 1270: ...62 68 62 MICROCOMPUTER CONNECTION ETHERNET 62 8 Precautions ...
Page 1271: ...MODBUS CONNECTIONS 63 MODBUS R RTU CONNECTION 63 1 64 MODBUS R TCP CONNECTION 64 1 ...
Page 1272: ......
Page 1292: ...64 12 64 MODBUS R TCP CONNECTION 64 7 Precautions ...
Page 1293: ...CONNECTIONS TO PERIPHERAL EQUIPMENT 65 VNC R SERVER CONNECTION 65 1 ...
Page 1294: ......
Page 1298: ...65 4 65 VNC R SERVER CONNECTION 65 4 Setting in Personal Computer ...
Page 1302: ...REVISIONS 4 ...
Page 1305: ......
Page 1306: ......