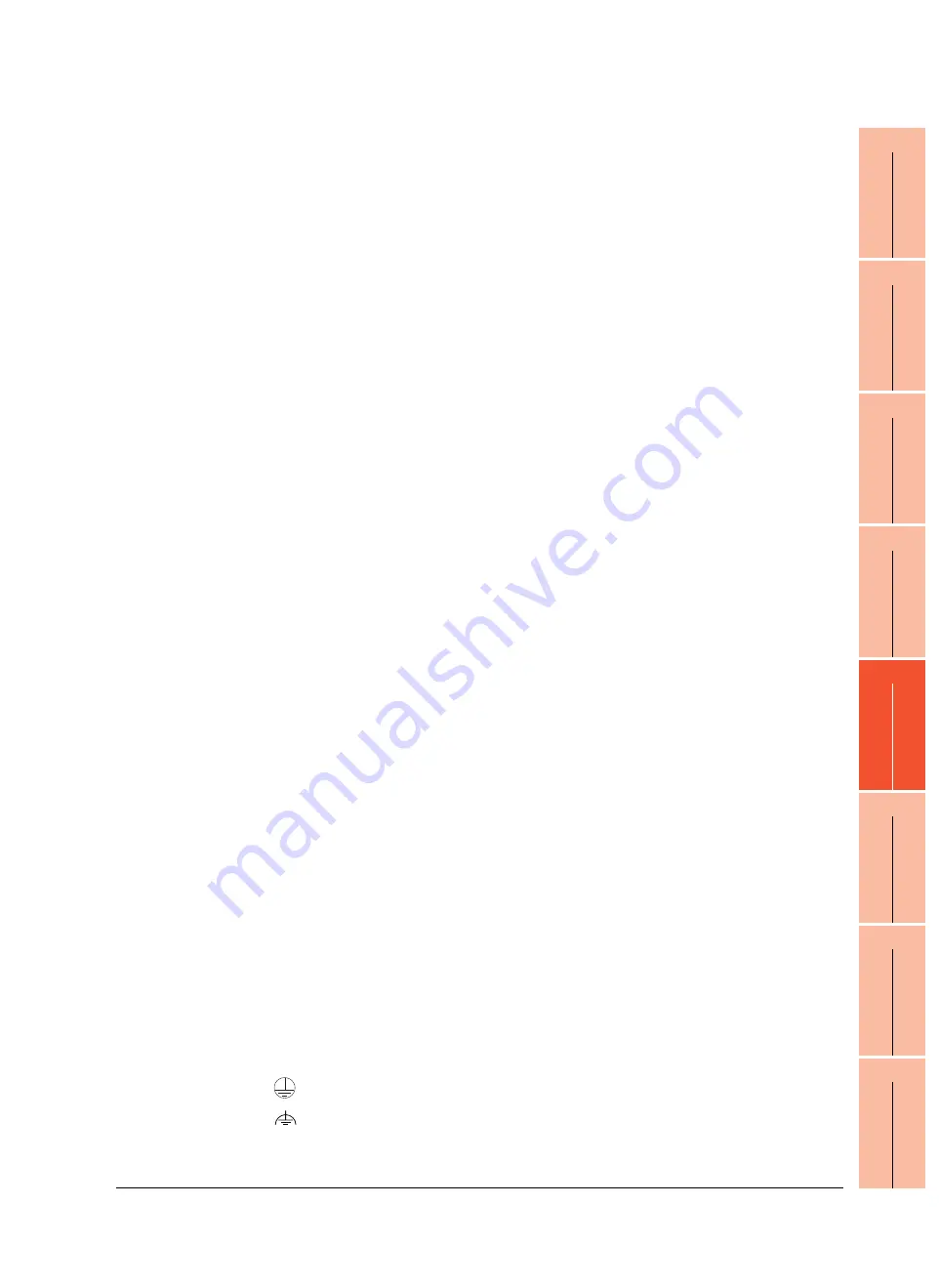
1
OV
ER
VI
EW
2
SY
STEM
CONFIGURA
TION
3
SP
ECI
F
IC
A
T
IO
NS
4
PA
R
T
S
N
A
M
E
5
UL,
cU
L
ST
A
N
D
AR
D
S AN
D
E
MC DIRECTIV
E
6
OPT
ION
7
INS
TAL
LA
T
IO
N
8
COMMUNICA
TION
CABL
E
5. UL, cUL STANDARDS AND EMC DIRECTIVE
5.2 EMC Directive
5 - 3
Control panel
Make sure to combine the GT14 Handy GOT with the Connector Conversion Box to comply with the EMC directive.
The Connector conversion box is an open type device (device installed to another device) and must be installed in a
conductive control panel.
It not only assure the safety but also has a large effect to shut down the noise generated from GOT, on the control
panel.
(1) Control panel
(a) The control panel must be conductive.
(b) When fixing a top or bottom plate of the control panel with bolts, do not coat the plate and bolt surfaces so
that they will come into contact.
And connect the door and box using a thick grounding cable in order to ensure the low impedance under
high frequency.
(c) When using an inner plate to ensure electric conductivity with the control panel, do not coat the fixing bolt
area of the inner plate and control panel to ensure conductivity in the largest area as possible.
(d) Ground the control panel using a thick grounding cable in order to ensure the low impedance under high
frequency.
(2) Connection of power and ground wires
Ground and power supply wires for the GOT must be connected as described below.
Provide a grounding point near the GOT. Short-circuit the FG terminals of the GOT (FG: frame ground) and
ground them with the thickest and shortest wire possible (The wire length must be 30cm (11.81in.) or shorter.)
The FG terminals function is to pass the noise generated in the PC system to the ground, so an impedance that
is as low as possible must be ensured. As the wires are used to relieve the noise, the wire itself carries a large
noise content and thus short wiring means that the wire is prevented from acting as an antenna.
Note) A long conductor will become a more efficient antenna at high frequency.
(3) Shock protection
In order to prevent those who are unfamiliar with power facility, e.g., an operator, from getting a shock, make
sure to take the following measures on the control panel.
(a) Store the GOT within the control panel locked, and allow only those who are familiar with power facility to
unlock the panel.
(b) Build the structure in order that the power supply will be shut off when the control panel is opened.
(4) Dustproof and waterproof features
The control panel also provides protection from dust, water and other substances. Insufficient ingression
protection may lower the insulation withstand voltage, resulting in insulation destruction. The insulation in the
GOT is designed to cope with the pollution level 2, so use in an environment with pollustion level 2 or better.
Grounding
The following are applicable ground terminals. Use them in the grounded state.
Be sure to ground the GOT for ensuring the safety and complying with the EMC Directive.
Pollution level1 :
An environment where the air is dry and conductive dust does not exist.
Pollution level2 :
An environment where conductive dust does not usually exist, but occasional
temporary conductivity occurs due to the accumulated dust.
Generally, this is the level for inside the control panel equivalent a control room or
on the floor of a typical factory.
Pollution level3 :
An environment where conductive dust exits and conductivity may be generated
due to the accumulated dust.
An environment for a typical factory floor.
Pollution level4 :
Continuous conductivity may occur due to rain, snow, etc. An outdoor environment.
Protective grounding
:
Ensures the safety of the GOT and improves the noise resistance.
Functional grounding
:
Improves the noise resistance.
Summary of Contents for GT14
Page 1: ......
Page 2: ......
Page 34: ...A 32 ...
Page 46: ...1 4 1 OVERVIEW 1 1 Features ...
Page 60: ...3 6 3 SPECIFICATIONS 3 4 Battery specifications ...
Page 72: ...5 8 5 UL cUL STANDARDS AND EMC DIRECTIVE 5 2 EMC Directive ...
Page 108: ...6 36 6 OPTION 6 7 With wall mounting Attachment ...
Page 124: ...8 10 8 COMMUNICATION CABLE 8 2 External Cable Relay Cable ...
Page 172: ...11 16 11 COMMUNICATION INTERFACE SETTING COMMUNICATION SETTING 11 3 Ethernet Setting ...
Page 200: ...12 28 12 DISPLAY AND OPERATION SETTINGS GOT SET UP 12 6 License Management ...
Page 296: ...14 92 14 FILE DISPLAY AND COPY PROGRAM DATA CONTROL 14 2 Various Data Control ...
Page 320: ...15 24 15 GOT SELF CHECK DEBUG AND SELF CHECK 15 4 GOT start time ...
Page 322: ...16 2 16 CLEANING DISPLAY SECTION CLEAN ...
Page 336: ...17 14 17 INSTALLATION OF COREOS BOOTOS AND STANDARD MONITOR OS 17 5 CoreOS ...
Page 360: ...19 8 19 MAINTENANCE AND INSPECTION 19 5 Backlight Shutoff Detection ...
Page 382: ......
Page 450: ...22 34 22 COMPUTER LINK CONNECTION 22 6 Precautions ...
Page 508: ...23 58 23 ETHERNET CONNECTION 23 5 Precautions ...
Page 526: ......
Page 592: ...26 22 26 SERVO AMPLIFIER CONNECTION 26 7 Precautions ...
Page 598: ...27 6 27 ROBOT CONTROLLER CONNECTION 27 6 Precautions ...
Page 607: ...MULTIPLE GOT CONNECTION FUNCTION 29 MULTIPLE GOT CONNECTION FUNCTION 29 1 ...
Page 608: ......
Page 619: ...MULTI CHANNEL FUNCTION 30 MULTI CHANNEL FUNCTION 30 1 ...
Page 620: ......
Page 635: ...FA TRANSPARENT FUNCTION 31 FA TRANSPARENT FUNCTION 31 1 ...
Page 636: ......
Page 688: ...31 52 31 FA TRANSPARENT FUNCTION 31 7 Precautions ...
Page 698: ...App 10 APPENDICES Appendix 2 Usage Condition of Utility Function ...
Page 703: ......
Page 704: ......
Page 705: ......
Page 706: ......
Page 738: ...A 32 ...
Page 748: ......
Page 820: ...33 44 33 CONNECTION TO OMRON PLC 33 4 Device Range that Can Be Set ...
Page 834: ...34 14 34 CONNECTION TO OMRON TEMPERATURE CONTROLLER 34 7 Precautions ...
Page 912: ...37 22 37 CONNECTION TO JTEKT PLC 37 7 Precautions ...
Page 930: ...38 18 38 CONNECTION TO SHARP PLC 38 6 Device Range that Can Be Set ...
Page 980: ...41 16 41 CONNECTION TO TOSHIBA PLC 41 4 Device Range that Can Be Set ...
Page 996: ...43 8 43 CONNECTION TO PANASONIC SERVO AMPLIFIER 43 7 Precautions ...
Page 1052: ...46 10 46 CONNECTION TO HITACHI PLC 46 6 Device Range that Can Be Set ...
Page 1092: ...47 40 47 CONNECTION TO FUJI PLC 47 5 Precautions ...
Page 1108: ...48 16 48 CONNECTION TO FUJI TEMPERATURE CONTROLLER 48 7 Precautions ...
Page 1142: ...49 34 49 CONNECTION TO YASKAWA PLC 49 4 Device Range that Can Be Set ...
Page 1332: ...55 28 55 CONNECTION TO GE PLC 55 7 Precautions ...
Page 1348: ...56 16 56 CONNECTION TO LS INDUSTRIAL SYSTEMS PLC 56 6 Device Range that Can Be Set ...
Page 1352: ...57 4 57 CONNECTION TO SICK SAFETY CONTROLLER 57 5 Device Range that Can Be Set ...
Page 1368: ...58 16 58 CONNECTION TO SIEMENS PLC 58 4 Device Range that Can Be Set ...
Page 1370: ...59 2 59 CONNECTION TO HIRATA CORPORATION HNC CONTROLLER ...
Page 1372: ...60 2 60 CONNECTION TO MURATEC CONTROLLER ...
Page 1374: ......
Page 1515: ...MODBUS CONNECTIONS 63 MODBUS R RTU CONNECTION 63 1 64 MODBUS R TCP CONNECTION 64 1 ...
Page 1516: ......
Page 1537: ...CONNECTIONS TO PERIPHERAL EQUIPMENT 65 VNC R SERVER CONNECTION 65 1 ...
Page 1538: ......
Page 1545: ......
Page 1546: ......