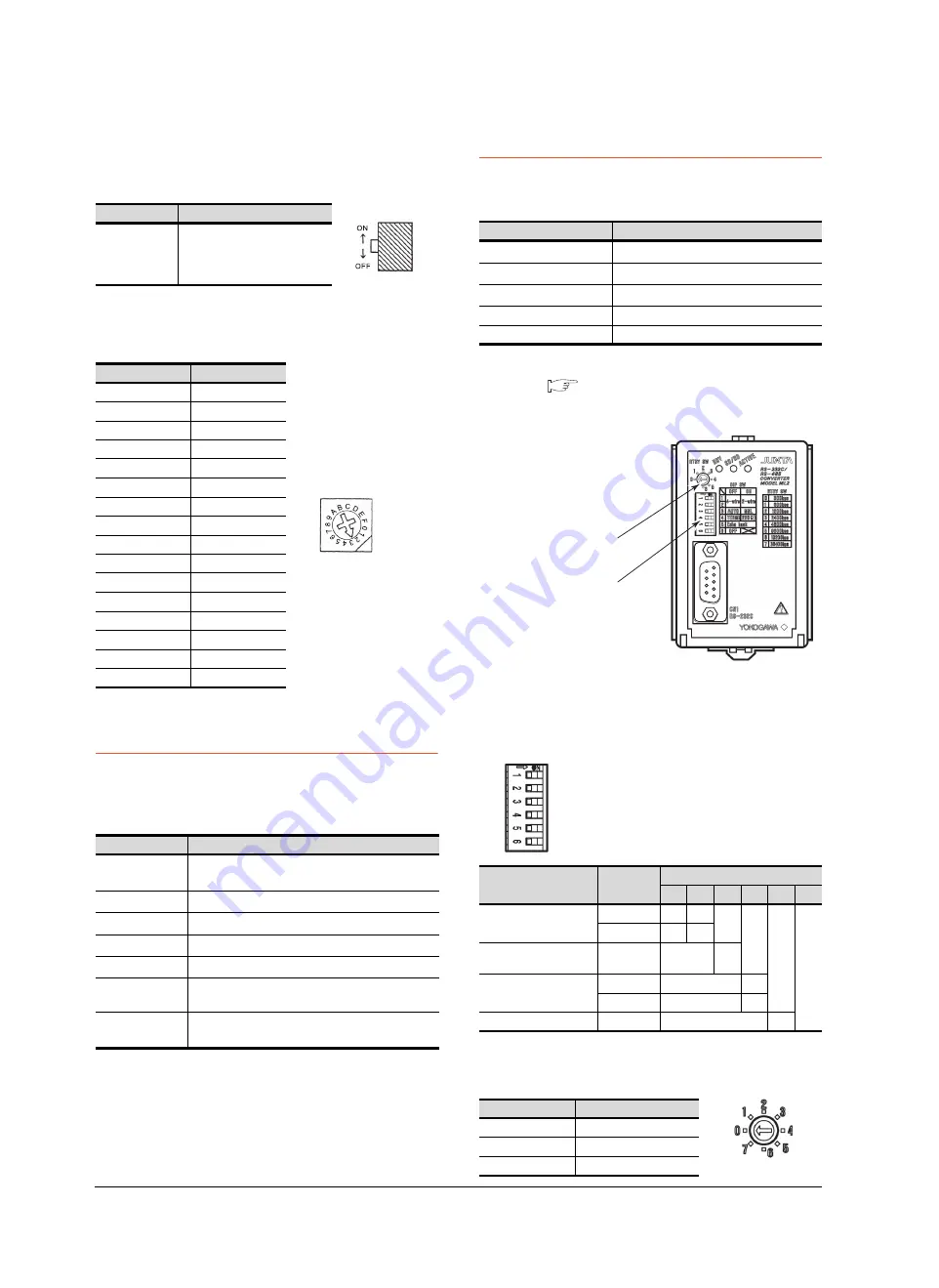
51 - 26
51. CONNECTION TO YOKOGAWA TEMPERATURE CONTROLLER
51.5 Temperature Controller Side Setting
(2) Communication mode settings
Make this setting by operating the communication
mode select DIP SW.
(3) A setting of the station No.
Make this setting by operating the station No. select
Rotary switch.
51.5.4 Connecting to UTAdvanced
Series
Communication settings
Make the communication settings by operating the key
of the temperature controller.
*1
Adjust the settings with GOT settings.
*2
Avoid duplication of the address with any of the other units.
51.5.5 Connecting to converter (ML2-
)
Communication settings
Make the communication settings using a setting switch.
*1
Adjust the settings with GOT settings.
*2
Refer to the following connection diagram for setting.
Settings by switch
(1) Settings of the setting (2-wire/4-wire), the RS-485
driver-active control, the terminating resistor, the
echo back
Make those settings by operating the communication
setting DIP SW.
(2) A setting of the transmission speed
Make this setting by operating the timer change-over
time Rotary switch.
Switch position
Communication mode
ON
PC link communication mode
Switch position
Station No.
0
1
1
2
2
3
3
4
4
5
5
6
6
7
7
8
8
9
9
10
A
11
B
12
C
13
D
14
E
15
F
16
Item
Set value
Transmission
speed
*1
9600bps, 19200bps, 38400bps
Data bit
*1
7bits, 8bits
Parity bit
*1
Even, Odd, None
Stop bit
*1
1bit, 2bits
Address
*1*2
1 to 99
Minimum response
time
0 to 10 (×10 ms)
Protocol
selection
*1
PCL(0): PC link communication (without sum check)
PCLSM(1): PC link communication (with sum check)
Item
Set value
Transmission speed
*1
9600bps, 19200bps, 38400bps
Setting (2-wire/4-wire)
*2
2-wire type or 4-wire type
Terminating resistor
*2
Done, None
Echo back
OFF
RS-485 driver-active control AUTO
Setting item
Set value
Switch No.
1
2
3
4
5
6
Setting (2-wire/4-wire)
4-wire type OFF OFF
-
2-wire
ON
ON
RS-485 driver-active
control
AUTO
OFF
terminating resister
With
ON
Without
OFF
Echo back
OFF
OFF
Switch position
Transmission speed
5
9600bps
6
19200bps
7
38400bps
Timer change-over time
Rotary switch
Communication setting
DIP SW
Summary of Contents for GT14
Page 1: ......
Page 2: ......
Page 34: ...A 32 ...
Page 46: ...1 4 1 OVERVIEW 1 1 Features ...
Page 60: ...3 6 3 SPECIFICATIONS 3 4 Battery specifications ...
Page 72: ...5 8 5 UL cUL STANDARDS AND EMC DIRECTIVE 5 2 EMC Directive ...
Page 108: ...6 36 6 OPTION 6 7 With wall mounting Attachment ...
Page 124: ...8 10 8 COMMUNICATION CABLE 8 2 External Cable Relay Cable ...
Page 172: ...11 16 11 COMMUNICATION INTERFACE SETTING COMMUNICATION SETTING 11 3 Ethernet Setting ...
Page 200: ...12 28 12 DISPLAY AND OPERATION SETTINGS GOT SET UP 12 6 License Management ...
Page 296: ...14 92 14 FILE DISPLAY AND COPY PROGRAM DATA CONTROL 14 2 Various Data Control ...
Page 320: ...15 24 15 GOT SELF CHECK DEBUG AND SELF CHECK 15 4 GOT start time ...
Page 322: ...16 2 16 CLEANING DISPLAY SECTION CLEAN ...
Page 336: ...17 14 17 INSTALLATION OF COREOS BOOTOS AND STANDARD MONITOR OS 17 5 CoreOS ...
Page 360: ...19 8 19 MAINTENANCE AND INSPECTION 19 5 Backlight Shutoff Detection ...
Page 382: ......
Page 450: ...22 34 22 COMPUTER LINK CONNECTION 22 6 Precautions ...
Page 508: ...23 58 23 ETHERNET CONNECTION 23 5 Precautions ...
Page 526: ......
Page 592: ...26 22 26 SERVO AMPLIFIER CONNECTION 26 7 Precautions ...
Page 598: ...27 6 27 ROBOT CONTROLLER CONNECTION 27 6 Precautions ...
Page 607: ...MULTIPLE GOT CONNECTION FUNCTION 29 MULTIPLE GOT CONNECTION FUNCTION 29 1 ...
Page 608: ......
Page 619: ...MULTI CHANNEL FUNCTION 30 MULTI CHANNEL FUNCTION 30 1 ...
Page 620: ......
Page 635: ...FA TRANSPARENT FUNCTION 31 FA TRANSPARENT FUNCTION 31 1 ...
Page 636: ......
Page 688: ...31 52 31 FA TRANSPARENT FUNCTION 31 7 Precautions ...
Page 698: ...App 10 APPENDICES Appendix 2 Usage Condition of Utility Function ...
Page 703: ......
Page 704: ......
Page 705: ......
Page 706: ......
Page 738: ...A 32 ...
Page 748: ......
Page 820: ...33 44 33 CONNECTION TO OMRON PLC 33 4 Device Range that Can Be Set ...
Page 834: ...34 14 34 CONNECTION TO OMRON TEMPERATURE CONTROLLER 34 7 Precautions ...
Page 912: ...37 22 37 CONNECTION TO JTEKT PLC 37 7 Precautions ...
Page 930: ...38 18 38 CONNECTION TO SHARP PLC 38 6 Device Range that Can Be Set ...
Page 980: ...41 16 41 CONNECTION TO TOSHIBA PLC 41 4 Device Range that Can Be Set ...
Page 996: ...43 8 43 CONNECTION TO PANASONIC SERVO AMPLIFIER 43 7 Precautions ...
Page 1052: ...46 10 46 CONNECTION TO HITACHI PLC 46 6 Device Range that Can Be Set ...
Page 1092: ...47 40 47 CONNECTION TO FUJI PLC 47 5 Precautions ...
Page 1108: ...48 16 48 CONNECTION TO FUJI TEMPERATURE CONTROLLER 48 7 Precautions ...
Page 1142: ...49 34 49 CONNECTION TO YASKAWA PLC 49 4 Device Range that Can Be Set ...
Page 1332: ...55 28 55 CONNECTION TO GE PLC 55 7 Precautions ...
Page 1348: ...56 16 56 CONNECTION TO LS INDUSTRIAL SYSTEMS PLC 56 6 Device Range that Can Be Set ...
Page 1352: ...57 4 57 CONNECTION TO SICK SAFETY CONTROLLER 57 5 Device Range that Can Be Set ...
Page 1368: ...58 16 58 CONNECTION TO SIEMENS PLC 58 4 Device Range that Can Be Set ...
Page 1370: ...59 2 59 CONNECTION TO HIRATA CORPORATION HNC CONTROLLER ...
Page 1372: ...60 2 60 CONNECTION TO MURATEC CONTROLLER ...
Page 1374: ......
Page 1515: ...MODBUS CONNECTIONS 63 MODBUS R RTU CONNECTION 63 1 64 MODBUS R TCP CONNECTION 64 1 ...
Page 1516: ......
Page 1537: ...CONNECTIONS TO PERIPHERAL EQUIPMENT 65 VNC R SERVER CONNECTION 65 1 ...
Page 1538: ......
Page 1545: ......
Page 1546: ......