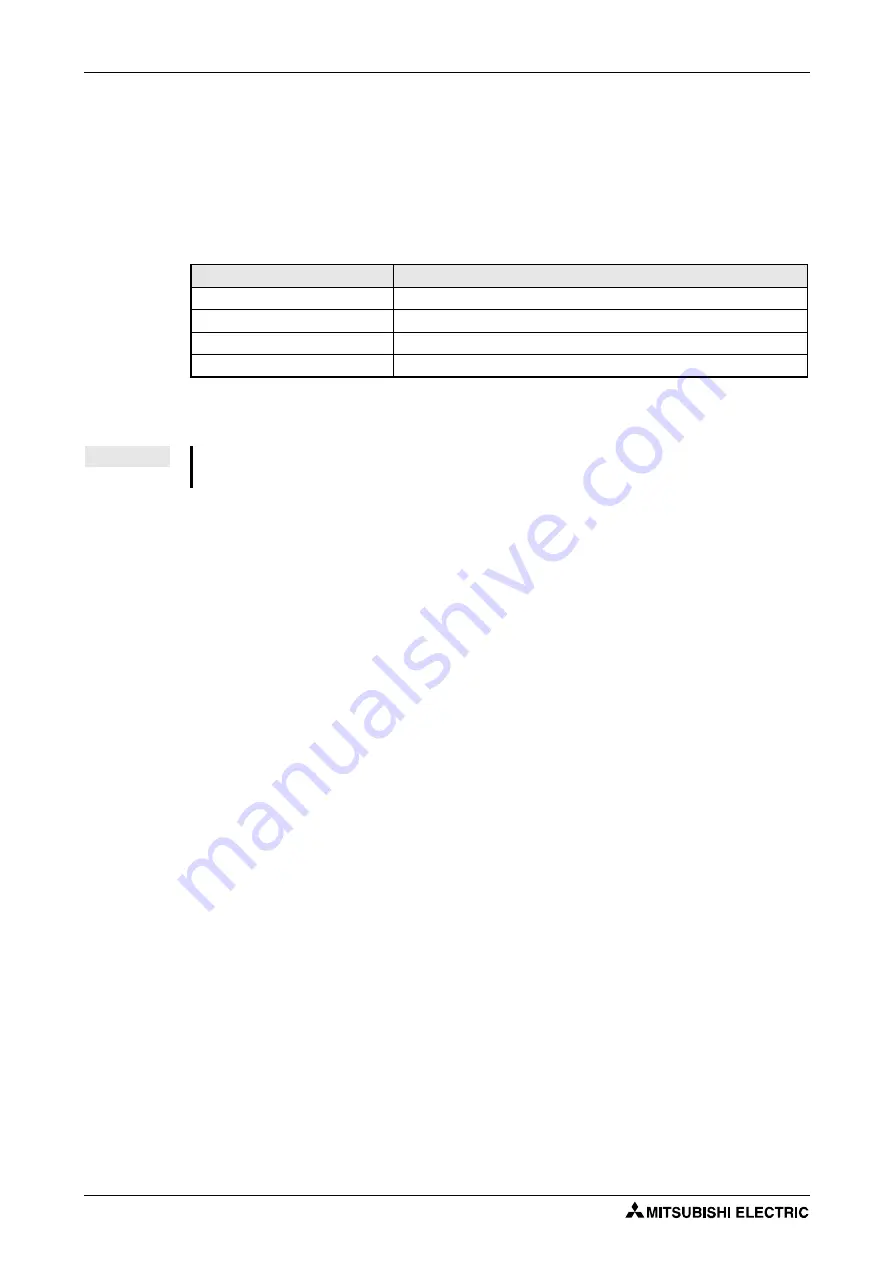
Inspection
Maintenance and inspection
8 - 4
8.1.4
Display of the life of the inverter parts
The self-diagnostic alarm is output when the life span of the control circuit capacitor, cooling fan
and each parts of the inrush current limit circuit is near to give an indication of replacement time.
For the life check of the main circuit capacitor, the alarm signal (Y90) will not be output if a meas-
uring method using Parameter 259 is not performed. (Refer to the description below.)
The life alarm output can be used as a guideline for life judgement:
Parts
Judgement Level
Main circuit capacitor
85% of the initial capacity
Control circuit capacitor
Estimated 10% life remaining
Inrush current limit circuit
Estimated 10% life remaining (Power on: 100,000 times left)
Cooling fan
Less than 50% of the predetermined speed
Tab. 8-2:
Guideline for the alarm signal output
NOTE
Refer to section 6.20.2 "Display of the life of the inverter parts" to perform the life check of
the inverter parts.
Summary of Contents for FR-D720S SC EC
Page 2: ......
Page 4: ......
Page 24: ...Description of the case Product checking and part identification 1 4 ...
Page 108: ...Operation panel Operation 4 20 ...
Page 436: ...Setting for the parameter unit and operation panel Parameter 6 286 ...
Page 484: ...Measurements on the main circuit Maintenance and inspection 8 14 ...
Page 504: ...Specification change Appendix A 20 ...
Page 505: ......
Page 506: ......
Page 510: ...Index Appendix A 24 ...
Page 511: ......