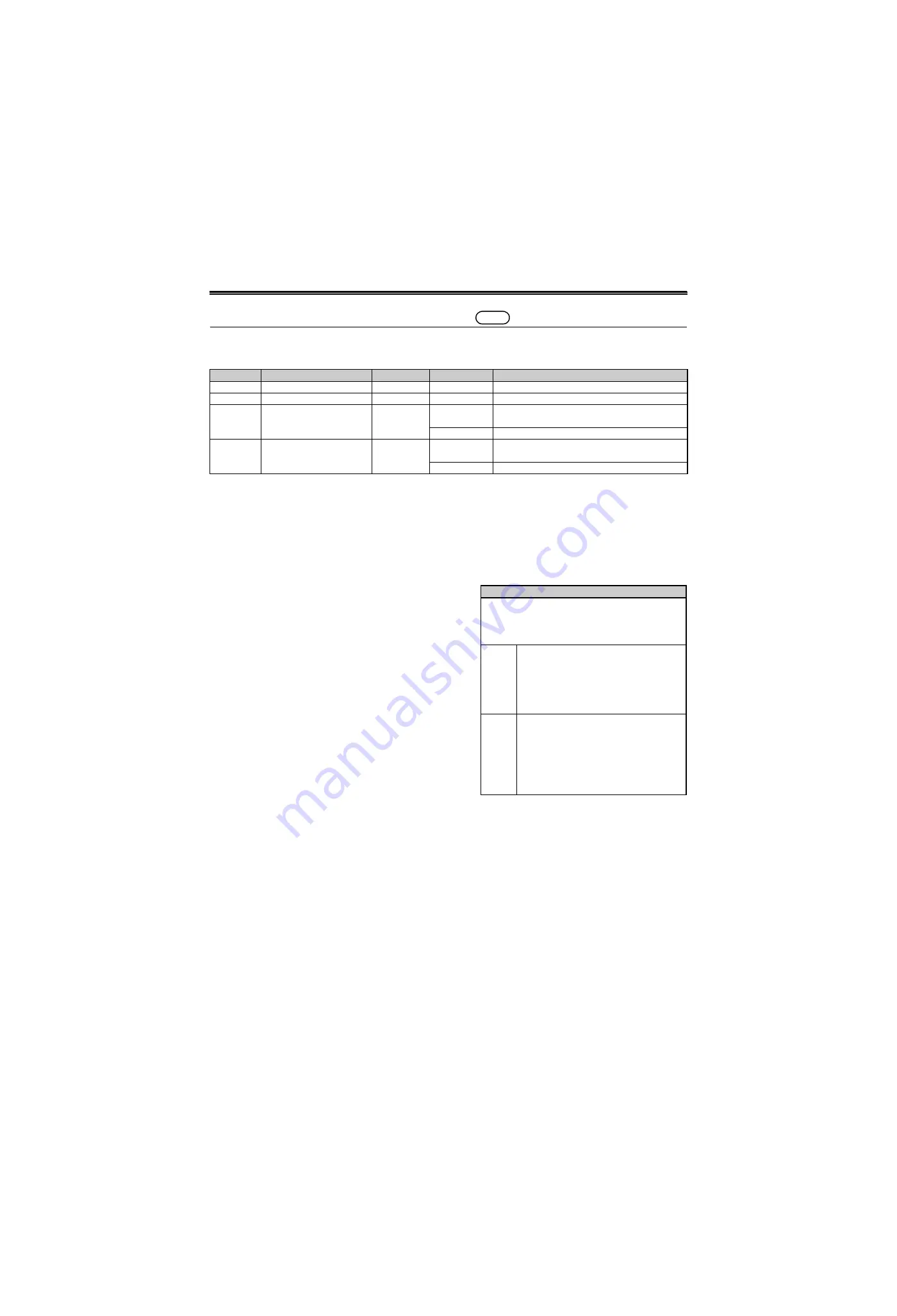
306
PARAMETER
2.10.4 Gain adjustment [Pr. 824, 825, 834, 835]
(A700)
)
Although stable operation is available with the initial value, make adjustment when any of such case as unusual motor and
machine vibration noise and overcurrent has occurred.
(1) Adjustment of current loop proportional
(P) gain
Set the proportional gain for torque control. For
general adjustment, make setting within the range 50
to 200% as a guideline.
Increasing the value improves response to a current
command change and reduces current variation with
disturbance. However, a too large gain will cause
instability, generating harmonic torque pulsation.
(2) Adjustment of current control integral
time
Set the integral time of current control during torque
control.
A small value enhances the torque response level,
but a too small value will cause current fluctuation.
Decreasing the value shortens the time taken to
return to the original torque if current variation with
disturbance occurs.
(3) Use two gains
When you want to change the gain according to
applications, or to switch multiple motors with one
inverter, etc., use [
Pr. 834 Torque control P gain 2
] and
[
Pr. 835 Torque control integral time 2
].
[
Pr. 834 Torque control P gain 2
] and [
Pr. 835 Torque
control P gain 2
] are valid when the RT signal is ON.
(4) Adjustment procedure
Make adjustment when any of unusual motor and
machine vibration, noise, current, and overcurrent
occurs.
1) Check the conditions and simultaneously change
the [
Pr. 824
].
2) If you cannot make proper adjustment, change
the [
Pr. 825
] value and repeat step 1).
[Pr. ]
Name
Initial Value
Setting Range
Description
824
Torque control P gain 1
100%
0 to 200%
Set the current loop proportional gain.
825
Torque control integral time 1
5ms
0 to 500ms
Set the current loop integral compensation time.
834
Torque control P gain 2
9999
0 to 200%
Set the current loop proportional gain when the RT
signal is ON.
9999
Without torque control P gain 2 function
835
Torque control integral time 2
9999
0 to 500ms
Set the current loop integral compensation time when
the RT signal is ON.
9999
Without torque control integral time 2 function
A700
Adjustment Method
Set [
Pr. 824
] a little lower and [
Pr. 825
] a little higher. First
lower [
Pr. 824
] and check the motor for unusual vibration
,
noise and overcurrent. If the problem still persists,
increase [
Pr. 825
] .
[
Pr. 824
]
Decrease the value by 10% until just before
unusual noise and current are improved, and
set about 0.8 to 0.9 of that value.
Note that a too low value will produce current
ripples, causing the motor to generate sound
synchronizing with the cycle of current ripples.
[
Pr. 825
]
Double the current value until just before an
unusual noise and current does not occur, and
set about 0.8 to 0.9 of that value.
Note that taking a too long time will produce
current ripples, causing the motor to generate
sound synchronizing with the cycle of current
ripples.
Summary of Contents for FR-A700 Series
Page 245: ...279 2 PARAMETER PARAMETER MEMO ...
Page 440: ...474 PARAMETER MEMO ...
Page 522: ...556 SELECTION MEMO ...