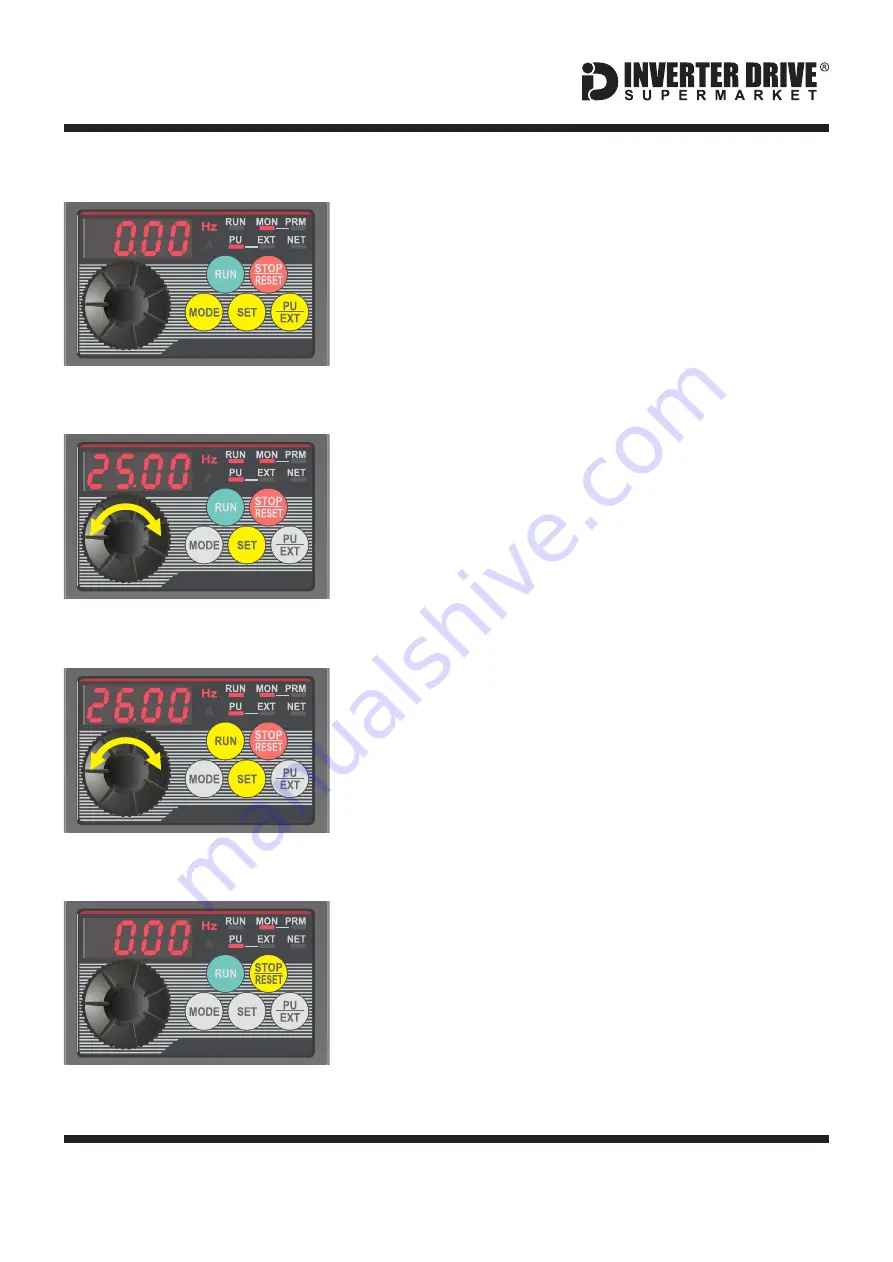
Easy Start Guide
7. How to operate the Inverter from the keypad
Page 7
This guide has been produced by The Inverter Drive Supermarket Ltd.
All content, including but not limited to graphics, text and procedures copyright
The Inverter
©
Drive Supermarket and must not be reproduced or altered without prior written permission.
7.3 Press the green “RUN” key to start the motor.
The green key will start the motor. The time taken for the
motor to accelerate to the desired speed (in seconds) is
proportional to parameter Pr. 7. The “RUN” indicator will
illuminate to indicate that the motor is running.
To change the speed whilst the motor is running, rotate the
dial to select the new speed and press “SET” to confirm.
The motor will accelerate or decelerate to the new speed.
Mitsubishi D700-SC Series Inverter
7.1 Select “MON” and “PU” modes.
With the motor stopped, press the “PU/EXT” key
repeatedly to cycle through operation modes until the
“PU” indicator is illuminated and “0.00" is displayed.
Then, press the “MODE” key repeatedly to cycle through
modes until “MON” is illuminated.
Finally, ensure the display is set to “Hz”. If it is set to “A”
(Amps), use the “SET” key to change to “Hz”.
7.2 Set the desired speed.
Rotate the dial to set the desired speed. In this example,
we have set this to 25.00Hz which is half speed for a
standard 50Hz motor.
Press “SET” to save. The display will alternate between
“F” and your selection for 3 seconds before returning to
0.00 (the current speed). When saving, ensure you don’t
accidentally set the display to “A”. If you do, use the
“SET” key to change back to “Hz”.
7.4 Press the red “Stop” key to stop the motor.
The red key will stop the motor. The time taken (in seconds)
to stop the motor is proportional to parameter Pr. 8.
Note: if you would prefer to continually adjust the speed
using the dial (rather than confirming with set each time)
change parameter Pr. 161 to 1.